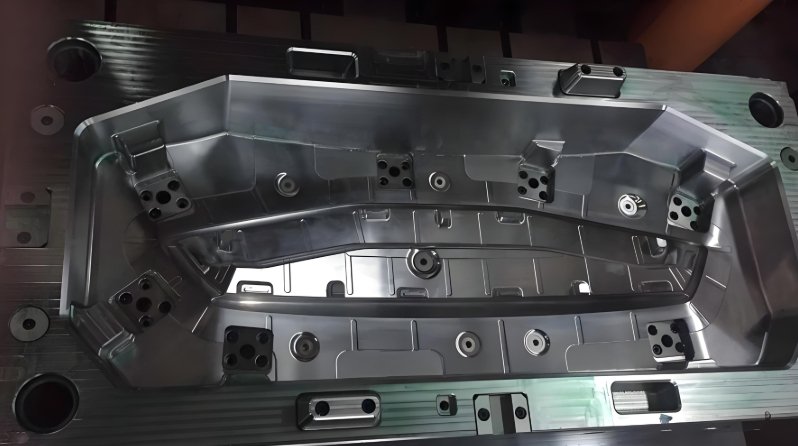
Automotive manufacturing needs precision. It demands efficiency and cost-effectiveness. Automotive Injection Molds make this possible. Skilled Mold Makers create molds for various parts. These molds enhance production speed and quality. This article explores how injection molds streamline production.
Why Choose Automotive Injection Molds?
1. Consistency
Injection molds ensure every part is identical. This eliminates variations.
2. Durability
Molded parts last longer. They resist wear and tear.
3. Efficiency
Injection molding speeds up production. It allows high-volume manufacturing.
4. Cost-Effectiveness
Once a mold is made, costs drop significantly. Large batches become affordable.
The Role of a Skilled Mold Maker
1. Design Expertise
A Mold Maker creates accurate designs. They understand automotive requirements.
2. Material Knowledge
Mold Makers select the best materials. This ensures the mold’s longevity.
3. Precision Engineering
They use advanced tools for precision. This leads to high-quality molds.
4. Customization
A skilled Mold Maker adapts designs to client needs. This flexibility is crucial for diverse parts.
Key Parts Made with Automotive Injection Molds
1. Bumpers
Bumpers require strength and durability. Injection molding delivers both.
2. Grilles
Grilles have intricate designs. Injection molds ensure precision.
3. Dashboard Panels
Panels need uniformity. Injection molds guarantee this.
4. Engine Components
Certain plastic engine parts come from molds. These parts are lightweight and heat-resistant.
Materials Used in Automotive Injection Molds
1. ABS Plastic
ABS plastic is durable and impact-resistant.
2. Polycarbonate
This material offers strength and transparency.
3. Nylon
Nylon is flexible and heat-resistant.
4. Polypropylene
Polypropylene is affordable and lightweight.
The Injection Molding Process
1. Designing the Mold
A Mold Maker starts with detailed designs.
2. Material Selection
The right plastic material is chosen.
3. Injection
Molten plastic is injected into the mold.
4. Cooling
The mold cools the plastic into shape.
5. Trimming
Excess material is removed for a smooth finish.
Benefits of Using Injection Molds
1. High Production Speed
Injection molding produces many parts quickly.
2. Precision and Accuracy
Each part matches the exact specifications.
3. Low Waste
The process reduces material waste.
4. Versatility
Molds can create complex and simple shapes.
Challenges in Automotive Injection Molds
1. High Initial Costs
Mold creation can be expensive. However, it pays off with volume production.
2. Material Limitations
Not all plastics suit every application. Choosing the right one is crucial.
3. Maintenance
Molds need regular care. This ensures consistent quality.
The Role of Technology
1. 3D Printing
3D printing helps create prototype molds faster.
2. Automation
Robots improve production speed and accuracy.
3. Advanced Software
Software enhances mold design precision.
Applications of Injection Molds in Automotives
1. Interior Components
Seats, panels, and trims use injection molds.
2. Exterior Parts
Bumpers, grilles, and mirrors rely on molds.
3. Engine Parts
Certain lightweight engine components come from molds.
4. Lighting Components
Headlight and taillight housings use precise molds.
Sustainability with Injection Molds
1. Recycled Materials
Molds can use recycled plastics.
2. Energy Efficiency
Modern machines consume less energy.
3. Waste Reduction
The process minimizes material waste.
The Future of Automotive Injection Molds
1. Eco-Friendly Materials
Bio-based plastics are gaining attention.
2. Faster Production
Advanced machines will reduce production time further.
3. Customization
Future molds will cater to unique designs and functions.
Automotive Injection Molds revolutionize automotive manufacturing. They bring speed, precision, and cost-efficiency. Skilled Mold Makers ensure every mold meets high standards. As technology advances, the process will become even more efficient. For durable, high-quality parts, injection molding remains essential.