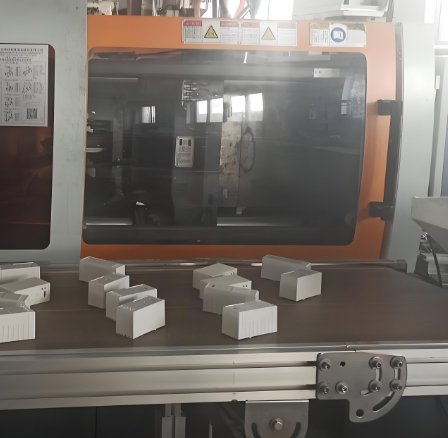
Electronics production impacts the environment. Electronic injection molding can reduce waste and energy use. A skilled mold maker plays a key role in sustainable manufacturing. This article explores green molding techniques and materials.
1. Why Sustainability Matters in Electronics Manufacturing
1.1 Reducing Plastic Waste
Electronics use a lot of plastic. Electronic injection molding helps minimize waste.
1.2 Lowering Carbon Footprint
Traditional molding consumes energy. A mold maker uses efficient machines to cut emissions.
1.3 Meeting Environmental Regulations
Governments demand greener production. Electronic injection molding must adapt to new laws.
2. Sustainable Molding Techniques
2.1 Recycled Plastic Injection Molding
Old plastics become new parts. A mold maker selects recyclable materials to reduce waste.
2.2 Bio-Based Resin Molding
Bioplastics replace petroleum-based resins. Electronic injection molding benefits from plant-based alternatives.
2.3 Energy-Efficient Molding Machines
New machines use less power. A mold maker ensures lower energy consumption.
3. Green Materials for Electronic Components
3.1 Recycled ABS and Polycarbonate
Recycled plastics work well. Electronic injection molding ensures quality and strength.
3.2 Biodegradable Polymers
Some plastics break down naturally. A mold maker explores compostable options.
3.3 Non-Toxic Additives
Traditional plastics use harmful chemicals. Electronic injection molding can eliminate toxic substances.
4. Energy-Saving Strategies in Injection Molding
4.1 Low-Heat Processing
Less heat means less energy use. A mold maker optimizes temperature control.
4.2 Hybrid and Electric Molding Machines
Electric machines waste less energy. Electronic injection molding benefits from modern equipment.
4.3 Smart Sensors for Process Control
AI-powered monitoring improves efficiency. A mold maker reduces defects and material waste.
5. Sustainable Mold Design
5.1 Lightweight Molds
Lighter molds use less material. Electronic injection molding becomes more resource-efficient.
5.2 Modular Mold Systems
Reusable mold parts reduce waste. A mold maker designs flexible tooling.
5.3 Long-Lasting Mold Materials
Durable molds cut production costs. Electronic injection molding benefits from high-quality steel and alloys.
6. Waste Reduction Strategies
6.1 Regrinding and Reusing Scrap Plastic
Leftover plastic gets reused. A mold maker prevents unnecessary waste.
6.2 Precision Molding for Less Material Loss
Tighter control means less excess plastic. Electronic injection molding ensures precise material use.
6.3 Closed-Loop Recycling in Factories
Scrap materials go back into production. A mold maker ensures a circular system.
7. Water Conservation in Molding
7.1 Cooling System Optimization
Better cooling saves water. Electronic injection molding benefits from advanced cooling designs.
7.2 Recycled Water Systems
Factories reuse water. A mold maker helps reduce water waste.
7.3 Eco-Friendly Mold Release Agents
Some lubricants harm the environment. Electronic injection molding uses biodegradable alternatives.
8. Challenges in Sustainable Electronic Injection Molding
8.1 Higher Material Costs
Eco-friendly materials cost more. A mold maker finds budget-friendly solutions.
8.2 Maintaining Performance Standards
Green plastics must stay strong. Electronic injection molding ensures quality control.
8.3 Adapting to New Regulations
Laws change frequently. A mold maker stays updated on sustainability rules.
9. The Future of Green Injection Molding
9.1 AI for Sustainable Production
AI improves efficiency. Electronic injection molding becomes smarter.
9.2 Carbon-Neutral Manufacturing
Factories aim for zero emissions. A mold maker integrates green practices.
9.3 3D Printing and Injection Molding
Hybrid methods reduce waste. Electronic injection molding evolves with new technology.
Sustainability is the future of electronic injection molding. A skilled mold maker helps reduce waste, save energy, and use greener materials. The industry must keep innovating for a cleaner planet.