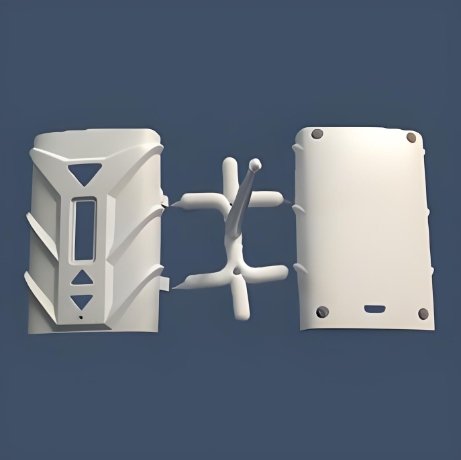
Electronics are part of daily life.
We use them everywhere.
Phones.
Laptops.
TVs.
Smart devices.
But electronics create waste.
Plastic parts add to pollution.
That needs to change.
Electronic Injection Molding is part of that change.
And the Mold Maker plays a key role.
Together, they build a greener future.
What Is Sustainability in Molding?
Sustainability means less harm.
Less waste.
Lower energy use.
Smarter materials.
In Electronic Injection Molding, this matters.
Every step must help the planet.
From design to production.
The Mold Maker helps make that possible.
They shape parts.
They reduce waste.
They design for efficiency.
Why Sustainability Matters Now
The world is watching.
Customers care about the planet.
Governments pass green laws.
Brands want cleaner processes.
Electronics must evolve.
They must become eco-friendly.
Plastic use is under pressure.
Recycling is rising.
And waste reduction is a goal.
Electronic Injection Molding must adapt.
The Mold Maker must lead.
How the Mold Maker Supports Sustainability
A good Mold Maker thinks ahead.
They ask:
- Can this part be smaller?
- Can this design reduce waste?
- Can we run faster cycles?
They shape the mold.
They guide the material.
They reduce defects.
Every mold they make impacts energy.
Impacts plastic use.
Impacts cost and waste.
Smart Mold Design for Greener Parts
Design affects everything.
Good design saves material.
It prevents short shots.
It avoids overflows.
A smart Mold Maker does more.
They optimize wall thickness.
They improve gate placement.
They control cooling paths.
These steps cut energy.
And reduce cycle time.
Material Choices in Electronic Injection Molding
Materials are key.
Not all plastics are equal.
Some harm more.
Some help more.
Today, greener plastics exist.
Bio-based resins.
Recycled polymers.
Biodegradable blends.
Each needs the right mold.
Each needs care.
The Mold Maker learns these materials.
They adapt tools to match.
That keeps parts strong and green.
Using Recycled Plastic
Recycled plastic saves the planet.
It cuts waste.
It uses less oil.
Electronic Injection Molding can use recycled resins.
But it needs precision.
Recycled plastic flows differently.
The Mold Maker adjusts gates.
They manage flash risks.
They test flow speed.
This makes sure parts stay high-quality.
Energy Efficiency in Molding
Molding uses energy.
Machines heat plastic.
Cool tools.
Run hydraulics.
That takes power.
The Mold Maker can help save it.
How?
By designing fast-cooling molds.
By using fewer cycles.
By avoiding rework.
Hot runner systems help too.
They waste less plastic.
They improve flow.
Each smart choice saves energy.
That’s green progress.
Reducing Scrap
Scrap is waste.
It wastes plastic.
Time.
Money.
Good molds make good parts.
They avoid short shots.
Burn marks.
Warping.
That’s the job of a great Mold Maker.
They fine-tune designs.
They test before mass runs.
Less scrap means greener molding.
Automation and Sustainability
Automation helps the planet.
It cuts errors.
It speeds up work.
It reduces downtime.
Electronic Injection Molding runs better with automation.
Robots remove parts.
Sensors check quality.
Systems adjust temps and speed.
The Mold Maker supports automation.
They design molds for ejector arms.
For sensors.
For feedback.
This builds a better process.
With less waste.
Maintenance and Mold Life
Longer mold life helps the earth.
A strong mold runs longer.
It makes more parts.
It wastes less steel.
A good Mold Maker builds tough tools.
They use the right steel.
They coat surfaces.
They protect from wear.
This means fewer replacements.
Less downtime.
More savings.
Designing for End-of-Life
What happens after use?
That matters too.
Designing parts for recycling helps.
Simple shapes.
No mixed materials.
Clear resin types.
Electronic Injection Molding can help here.
The Mold Maker can shape better parts.
Ones that are easy to recycle.
That’s long-term sustainability.
Eco Certifications and Standards
Green molding follows rules.
Some include:
- ISO 14001 (Environmental Management)
- RoHS (No hazardous substances)
- REACH (Safe chemicals)
The Mold Maker supports this.
They use certified steel.
They avoid banned materials.
They record every step.
This builds trust.
And meets global laws.
Partnering for Green Success
No one does it alone.
Factory.
Mold Maker.
Resin supplier.
Machine maker.
They all must work together.
Share data.
Share goals.
Test new ideas.
Teamwork leads to green wins.
Looking Ahead: What’s Next?
Green tech keeps growing.
Soon we’ll see:
- More plant-based plastics
- Fully closed-loop recycling
- Carbon-neutral molding lines
Electronic Injection Molding will evolve.
The Mold Maker must stay ready.
They must train.
And innovate.
That’s how we reach a better future.
The path is clear.
Green is the way forward.
Electronics must change.
Plastic must change.
Electronic Injection Molding can lead the change.
The Mold Maker is the driver.
Together, they cut waste.
Save energy.
Build cleaner products.
The earth needs action.
And the molding world must deliver.
Choose sustainability.
Shape the future.
One mold at a time.