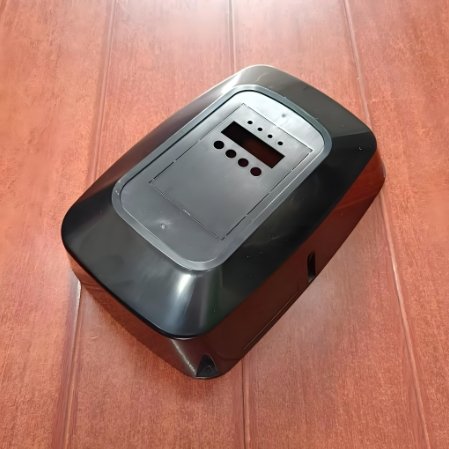
Electronic Injection Molding is a precise and intricate process. It is used to create parts for electronic devices. However, it comes with its own set of challenges. These challenges can affect the final product’s quality and performance. Overcoming these issues requires knowledge and skill. A skilled mold maker is key to finding solutions.
1. Material Selection and Shrinkage
One of the biggest challenges in electronic injection molding is material selection. The right material must be chosen for the part’s intended function. Shrinkage can occur as the material cools in the mold. Different materials have different shrinkage rates. This can lead to dimensional inaccuracies.
To overcome this challenge, mold makers must choose materials that suit the design requirements. Understanding the material’s shrinkage properties helps in mold design. Moreover, using advanced simulation software can predict shrinkage and help adjust the mold design accordingly.
2. Precision and Tolerance Issues
Electronic components must be manufactured to tight tolerances. Even a small deviation can cause the part to malfunction. For instance, connectors, insulators, and housings must fit precisely. Achieving this level of accuracy in electronic injection molding is challenging.
To tackle precision issues, mold makers must ensure the mold is designed with high precision. Regular maintenance of molds is also critical. The use of high-quality molds and advanced technologies, such as laser engraving, ensures better precision in the final product.
3. Warping and Deformation
Warping occurs when the molded part cools unevenly. This can cause the part to bend or distort. Warping is particularly problematic in electronic injection molding because it affects the functionality of the part. For example, it can distort the shape of connectors or casings.
The solution to warping lies in mold design. The cooling system within the mold must be carefully controlled. By ensuring uniform cooling, warping can be minimized. Mold makers can also adjust the mold’s wall thickness to ensure the material cools evenly.
4. Complex Geometries and Thin Walls
Many electronic parts have complex geometries or thin walls. These designs are difficult to mold accurately. Thin walls are particularly prone to issues like uneven cooling and flow inconsistencies. In electronic injection molding, this challenge is even more pronounced.
To overcome this challenge, mold makers need to design molds that can handle complex geometries. This includes using advanced techniques such as multi-cavity molds and hot runner systems. These techniques help manage the flow of material and ensure uniform cooling across all parts.
5. Short Shots and Incomplete Filling
Short shots happen when the mold cavity doesn’t fill completely. This is a major issue in electronic injection molding because it leads to defective parts. The parts may be incomplete or have weak spots. This problem can be caused by low injection pressure, improper gate design, or issues with the material flow.
To fix short shots, mold makers must focus on optimizing the mold design. The gate design must be carefully planned to allow the material to flow evenly. Increasing injection pressure and improving material flow can also help prevent short shots.
6. Contamination and Defects
Contamination can occur during the electronic injection molding process. Dust, debris, or even improper handling of materials can lead to defects. Contamination can cause surface imperfections or internal defects. These defects can compromise the performance of electronic components.
Proper cleaning and handling procedures are essential to prevent contamination. Mold makers must ensure the mold is clean and free from debris. Additionally, proper storage and handling of materials before molding are crucial for maintaining part quality.
7. Cycle Time and Efficiency
Long cycle times can reduce the efficiency of the molding process. In electronic injection molding, cycle times can be affected by material properties, mold design, and cooling rates. Longer cycles lead to higher production costs and lower throughput.
To reduce cycle times, mold makers must design molds that allow for faster material flow and cooling. Using advanced cooling techniques, such as conformal cooling channels, can help reduce cooling time. Automation in the injection molding process also plays a role in improving efficiency.
8. Environmental and Regulatory Considerations
In electronic injection molding, manufacturers must adhere to environmental and regulatory standards. These standards often require the use of eco-friendly materials and compliance with safety regulations. Adhering to these regulations while maintaining product quality can be a challenge.
Mold makers can help by selecting materials that meet environmental standards. They can also design molds that minimize waste and energy consumption. Staying updated with regulatory requirements ensures that the final products are both safe and eco-friendly.
9. Tool Wear and Maintenance
Molds experience wear and tear over time. This wear can lead to poor-quality parts, increased defects, and downtime. Mold makers must regularly maintain and repair molds to prevent issues from arising. Tool wear can be particularly problematic in electronic injection molding because even small changes in the mold can affect the part’s functionality.
Regular inspection and maintenance schedules are essential to prevent tool wear. Using durable materials for mold construction can also extend the life of the mold. Coatings and treatments can be applied to molds to reduce wear and improve performance.
10. Cost Management
The cost of producing electronic injection molding parts can be high. Material costs, mold design, and maintenance can add up quickly. It’s essential to manage these costs to maintain profitability while ensuring high-quality products.
To control costs, mold makers must focus on optimizing the mold design and improving efficiency. Reducing cycle times and material waste can help cut costs. Additionally, investing in high-quality molds and maintenance practices ensures that the mold lasts longer and requires fewer repairs.
Conclusion: Overcoming the Challenges in Electronic Injection Molding
Electronic injection molding is a complex process that requires precision and expertise. The challenges discussed above, such as shrinkage, warping, short shots, and cycle times, can affect the quality of electronic components. However, with the right strategies, these challenges can be overcome.
A skilled mold maker plays a critical role in addressing these issues. By focusing on mold design, material selection, and process optimization, mold makers can ensure the production of high-quality electronic components. With continuous improvements in technology and practices, the challenges in electronic injection molding can be minimized, leading to better, more reliable electronic products.