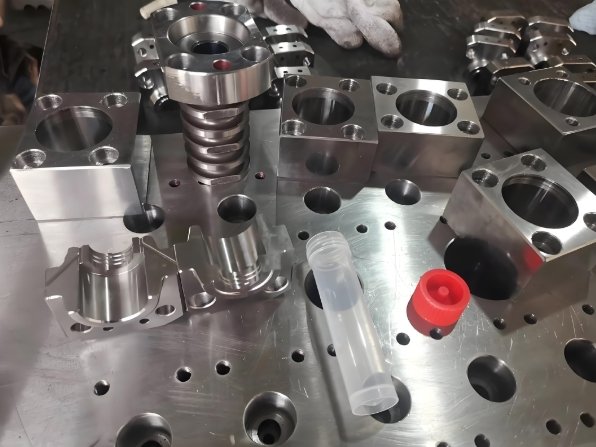
The medical industry is evolving rapidly. Medical injection molding remains the dominant method for producing medical devices. However, 3D printing is reshaping the way mold makers design, test, and manufacture parts. The future will see a stronger integration of these technologies. This combination will improve precision, reduce costs, and speed up production.
Why 3D Printing Matters in Medical Injection Molding
1. Faster Prototyping
3D printing allows quick design testing before full-scale molding begins. This reduces development time and costs.
2. Improved Customization
Medical devices can be tailored to individual patient needs. 3D-printed molds allow for greater design flexibility.
3. Lower Production Costs
Traditional mold-making can be expensive. 3D printing reduces tooling costs and material waste.
4. Complex Geometries
3D-printed molds enable intricate designs that are difficult to achieve with traditional methods.
5. Hybrid Manufacturing
Combining 3D printing with injection molding enhances efficiency and quality.
How 3D Printing Enhances Medical Injection Molding
1. Rapid Mold Prototyping
- Shortens development time.
- Allows multiple iterations before final mold production.
- Reduces cost of traditional steel molds.
2. Bridge Tooling for Low-Volume Production
- 3D-printed molds work for small production runs.
- Ideal for clinical trials or personalized medical devices.
- Eliminates the need for expensive traditional tooling.
3. Complex Mold Design
- Enables undercuts, micro-details, and fine textures.
- Reduces the number of mold components.
- Improves cooling efficiency in injection molding.
4. Lightweight and Durable Materials
- 3D printing uses high-strength polymers and metal powders.
- Provides durable mold inserts for long-term use.
- Improves efficiency in medical injection molding.
5. Faster Production Cycles
- Reduces lead times for mold production.
- Enhances efficiency in the manufacturing process.
- Enables quick adjustments to design flaws.
Advancements in 3D Printing for Medical Molding
1. High-Performance 3D Printing Materials
- Biocompatible resins for medical device molds.
- Metal 3D printing for long-lasting mold components.
- Heat-resistant polymers for injection mold tooling.
2. Multi-Material 3D Printing
- Combines soft and hard materials in a single print.
- Enables overmolding applications in medical products.
- Creates medical parts with different textures and flexibility.
3. 3D-Printed Conformal Cooling Channels
- Improves cooling efficiency in molds.
- Reduces cycle times in medical injection molding.
- Increases part quality by minimizing shrinkage.
4. AI-Driven Mold Design Optimization
- AI helps design complex mold structures.
- Reduces material waste and improves efficiency.
- Enhances precision in medical device production.
5. 3D Bioprinting for Custom Medical Devices
- Creates patient-specific implants and prosthetics.
- Works with bio-compatible materials for safer medical use.
- Could lead to personalized medical injection molding applications.
Challenges of Integrating 3D Printing with Injection Molding
1. Material Limitations
- Not all 3D-printed materials can withstand high-pressure molding.
- Research is needed for heat-resistant and durable polymers.
2. Scalability Issues
- 3D printing is slower for mass production.
- Traditional medical injection molding remains the best option for high-volume manufacturing.
3. Cost of Advanced 3D Printers
- Industrial-grade 3D printers are expensive.
- High-end materials increase production costs.
4. Regulatory Compliance
- Medical-grade 3D-printed molds must meet FDA and ISO standards.
- Extensive testing is required for approval.
5. Durability Concerns
- 3D-printed molds may wear out faster than metal molds.
- Hybrid solutions with printed inserts may be required.
How Mold Makers Are Adapting to 3D Printing
1. Hybrid Mold Manufacturing
- Uses 3D printing for complex mold features.
- Combines traditional machining for durability.
- Reduces lead times for mold production.
2. Digital Twin Technology
- Creates a virtual model of the mold before production.
- Predicts potential defects using AI simulations.
- Enhances accuracy in medical injection molding.
3. Smart Manufacturing Integration
- IoT-enabled 3D printers optimize mold design.
- Real-time monitoring reduces defects and improves efficiency.
- Ensures precise and repeatable manufacturing.
4. Sustainable Mold Production
- 3D printing reduces material waste.
- Uses eco-friendly, recyclable materials for mold inserts.
- Lowers carbon footprint in medical device production.
Future Trends in 3D Printing and Medical Injection Molding
1. Fully 3D-Printed Injection Molds
- Stronger materials will enable longer-lasting printed molds.
- Reduces reliance on traditional metal molds.
2. AI-Driven Design Automation
- AI will create optimized mold designs with minimal waste.
- Enhances efficiency in medical injection molding.
3. 3D Printing for On-Demand Medical Parts
- Hospitals will use 3D printing for emergency medical devices.
- Reduces supply chain issues and delivery delays.
4. Personalized Medical Injection Molding
- Patient-specific implants and prosthetics will be mass-produced.
- Improves treatment outcomes with custom medical devices.
5. Bio-Compatible 3D-Printed Molds
- Advanced materials will improve the lifespan of printed molds.
- Hybrid molds will combine printed and machined components.
The future of medical injection molding is evolving with 3D printing. Mold makers are using advanced materials, AI, and automation to improve precision and efficiency. As technology advances, hybrid manufacturing will become the standard. This integration will create safer, high-quality medical devices at a faster pace. The combination of 3D printing and injection molding is shaping the future of medical manufacturing.