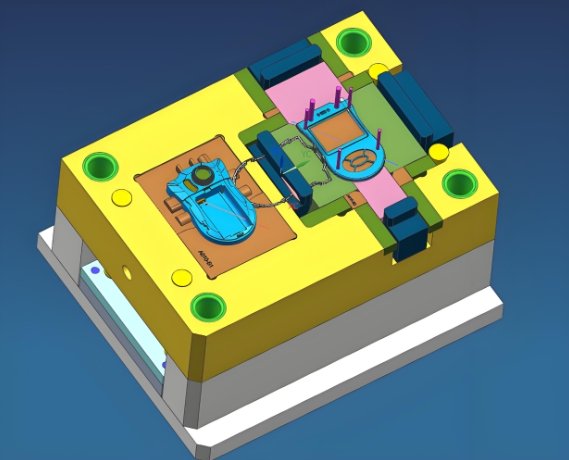
Plastics are everywhere.
They help build electronic products.
But plastic waste is a problem.
It stays in landfills.
It harms the planet.
Now, things are changing.
Biodegradable polymers are coming.
They break down over time.
They are better for the earth.
This change affects the whole industry.
Especially Electronic Injection Molding.
And every skilled Mold Maker.
Why Biodegradable Polymers Matter
Today’s electronics use a lot of plastic.
Housings.
Connectors.
Mounts.
Switch bases.
These parts are molded.
Electronic Injection Molding creates them fast.
But old plastics last forever.
That’s the issue.
Biodegradable polymers don’t stay forever.
They decay safely.
Some even compost.
That’s great for the planet.
It’s also good for smart business.
Green products are in demand.
The Role of the Mold Maker
The Mold Maker helps shape the future.
They build tools for new materials.
They test how polymers flow.
They make sure parts come out right.
Biodegradable plastics act differently.
They may melt at lower temps.
They may need special pressure.
The Mold Maker must adapt designs.
They use experience and testing.
That keeps quality high.
Popular Biodegradable Polymers
Many green plastics exist now.
Each one has strengths.
Each one needs the right setup.
PLA (Polylactic Acid)
Made from corn.
It’s easy to mold.
Used in light-duty parts.
But it’s brittle.
PHA (Polyhydroxyalkanoates)
Made by microbes.
Breaks down well.
Good for electronics.
Tougher than PLA.
PBS (Polybutylene Succinate)
Strong and flexible.
Good heat resistance.
Works in more mold types.
A smart Mold Maker learns each one.
They study flow.
They adjust cooling.
They avoid defects.
Challenges in Electronic Injection Molding
Biodegradable polymers aren’t easy.
They bring new problems.
Heat Sensitivity
They melt fast.
Too much heat ruins them.
Mold Makers lower mold temps.
Moisture Absorption
Some absorb water.
That weakens them.
Mold shops must store them dry.
Shrinkage
They may shrink unevenly.
That means warps or cracks.
Tooling must be precise.
Limited Use
They don’t suit all parts.
Some break down in heat.
So, not ideal near batteries or CPUs.
Mold Makers must know the limits.
And design with care.
Designing for Green Polymers
Design starts with knowledge.
The Mold Maker studies the plastic.
They adjust the mold shape.
They may add extra vents.
They tune runner systems.
They change gate styles.
Electronic Injection Molding works best with care.
Especially when using new plastics.
Machine Setup Matters
Molding machines must adjust too.
Lower barrel temps.
Slower speeds.
Tighter moisture control.
Cycle times may change.
Cooling may take longer.
Or shorter, based on polymer type.
The Mold Maker helps test setups.
They guide machine teams.
That means fewer defects.
Testing Is Key
Green plastics need extra testing.
Each batch behaves a little different.
Before production, test:
- Flow rate
- Shrink rate
- Cooling time
- Surface finish
The Mold Maker uses trial molds.
They fine-tune cavity design.
They stop problems early.
Benefits of Going Green
Why use biodegradable polymers at all?
They cost more.
They are harder to mold.
But the benefits are big.
Environmental Impact
Less long-term waste.
Lower carbon footprint.
Cleaner land and water.
Customer Demand
People want eco products.
They care about the planet.
Green electronics sell better.
Brand Image
Companies gain trust.
They stand out in the market.
Government Support
Some countries give tax breaks.
Or make laws for green materials.
All of this makes Electronic Injection Molding more responsible.
And the Mold Maker more valuable.
Future of Biodegradable Plastics in Electronics
Right now, it’s just starting.
Only a few parts use green plastics.
But that will grow fast.
In 5–10 years, many products will use them.
Chargers.
Cables.
Shells.
Even keyboards.
New blends are coming.
They will be stronger.
And cheaper too.
Mold Makers must stay ready.
They must learn new trends.
And master new plastics.
Recycling with Biodegradable Polymers
Some green plastics can be reused.
But not all.
PLA, for example, degrades over time.
Not ideal for regrind.
So waste control is key.
Mold Makers must help reduce scrap.
Use hot runners.
Use high-cavity molds.
Use precise ejection.
That means fewer bad parts.
Less plastic waste.
Partnering for Success
The journey is not solo.
The factory.
The Mold Maker.
The material supplier.
All must work together.
They must test.
They must share data.
They must plan each step.
Success in Electronic Injection Molding means teamwork.
Especially with new polymers.
The future is green.
Electronics will change.
So will the plastics inside them.
Electronic Injection Molding is moving forward.
And every smart Mold Maker must lead the way.
It’s not easy.
But it’s worth it.
Cleaner products.
Better planet.
Stronger business.
Biodegradable polymers are the future.
Are you ready?