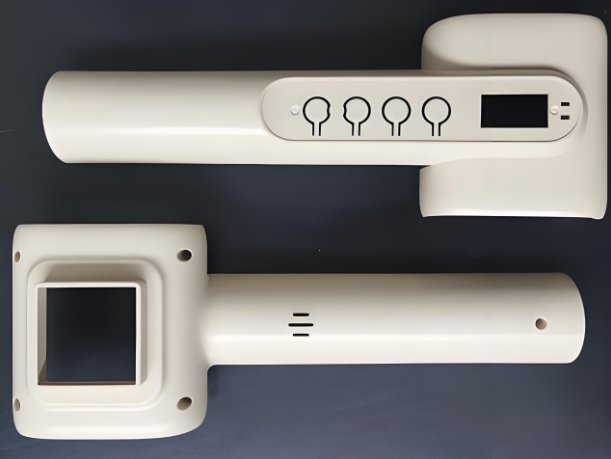
The manufacturing world is changing fast. New technology, market demands, and sustainability goals are reshaping how products are made. Electronic Injection Molding is at the heart of this transformation. It plays a key role in producing components for smartphones, computers, smart home devices, and electric vehicles.
To keep up with these changes, every Mold Maker must understand what the future holds. From smart machines to greener materials, the world of molding is evolving. Let’s explore the trends shaping the future of Electronic Injection Molding and how the Mold Maker will continue to be the driving force behind innovation.
1. Smart Manufacturing Will Become Standard
Automation is no longer optional. Smart factories are becoming the norm. Machines now come with sensors, cameras, and real-time monitoring systems. These tools help reduce waste and improve efficiency. In Electronic Injection Molding, smart machines can control pressure, temperature, and cycle time with high accuracy.
This level of control helps reduce defects and makes production more sustainable. The Mold Maker must adapt by designing molds that work with smart technology. These molds may include sensors and digital features to collect data during every cycle.
2. Miniaturization of Electronic Components
Electronic devices are getting smaller and thinner. This creates a need for ultra-precise parts with tight tolerances. Electronic Injection Molding must meet these high standards while maintaining fast production rates.
Micro-molding will become more common. These tiny components often require very small gates, intricate cavity designs, and special materials. A skilled Mold Maker must create detailed tools that can produce flawless micro-parts. This requires deep knowledge of mold flow, gate positioning, and venting.
3. Sustainability Will Drive Material Choices
The world is pushing for greener solutions. Governments and customers are demanding products made with recycled or biodegradable materials. As a result, Electronic Injection Molding will move toward eco-friendly plastics.
This creates challenges and opportunities. Some sustainable materials behave differently from traditional plastics. They may require new processing temperatures or have different shrink rates. The Mold Maker must design molds that handle these materials without causing defects or delays.
As companies seek to reduce their carbon footprint, the role of the Mold Maker becomes even more important in supporting sustainable manufacturing goals.
4. Customization Through 3D Printing and Rapid Tooling
Customization is on the rise. Consumers want products that are unique. This trend is driving the need for shorter production runs and faster mold changes. Rapid tooling and 3D printing will help meet this need.
In Electronic Injection Molding, quick mold development means faster time to market. 3D-printed mold inserts and aluminum prototypes allow testing before full-scale production. The Mold Maker must be skilled in both traditional machining and modern rapid tooling techniques.
By offering both, a Mold Maker becomes more valuable to manufacturers needing speed and flexibility.
5. Integration of Electronics and Plastics
As smart products become more common, the lines between electronic circuits and plastic housing are blurring. The future will see more parts with electronics embedded directly inside plastic components.
This requires advanced Electronic Injection Molding techniques, such as overmolding and insert molding. These processes place wires, sensors, or chips inside a mold before injection.
The Mold Maker must design tools that safely hold electronic parts while ensuring perfect plastic flow. A mistake can damage the electronics or cause short circuits. Precision and knowledge are critical.
6. AI and Machine Learning in Process Control
Artificial intelligence (AI) is becoming a powerful tool. In the future, AI will monitor Electronic Injection Molding machines in real time. It will adjust parameters automatically to prevent defects. It may also predict when a mold will need maintenance.
This makes the process more reliable and less wasteful. However, AI still needs quality data to work. The Mold Maker helps by designing tools with built-in sensors. These sensors collect accurate data, improving AI decision-making.
A good Mold Maker works closely with engineers to ensure the mold supports smart systems from day one.
7. Higher Demand for Cleanroom Manufacturing
Electronics are often sensitive to dust and particles. In industries like medical devices or semiconductors, parts must be made in clean environments. As more devices include sensors or microchips, cleanroom molding will become more common.
Electronic Injection Molding in cleanrooms requires special mold features. The Mold Maker must design tools that resist contamination and are easy to clean. They must also prevent plastic burns, flashing, or any defects that could affect the device’s performance.
This trend means more molds must meet strict standards—something only an expert Mold Maker can ensure.
8. Advanced Cooling Technologies
Cycle time is one of the biggest costs in molding. Advanced cooling methods like conformal cooling, which use 3D-printed channels, help reduce cooling time. This allows faster cycles and saves energy.
For Electronic Injection Molding, faster cooling means more parts produced with less power. The Mold Maker must use modern software and metal printing to design and create these cooling systems. It’s a new skill set, but one that brings big benefits.
9. Better Surface Finishes and Textures
Electronic devices must not only work well but also look and feel great. More companies are requesting special textures, glossy finishes, or anti-fingerprint coatings on molded parts.
The Mold Maker must create molds with detailed surface patterns. This could involve laser engraving or EDM processing. These textures must be consistent from one part to the next. Any defect on the surface could hurt the product’s value.
10. Global Collaboration and Digital Twins
Global supply chains are more connected than ever. Engineers in one country may design a product, while molds are made in another. Digital twins—a virtual copy of a mold—make it easier to share updates and solve problems.
The Mold Maker uses digital twin software to simulate mold behavior. This helps identify flow issues or hot spots before steel is cut. It saves time, money, and material.
Electronic Injection Molding companies that adopt digital collaboration will be faster and more flexible. The Mold Maker must be ready to work with global teams and digital tools.
The future of Electronic Injection Molding is bright, but also full of change. Smart factories, greener materials, embedded electronics, and fast mold cycles will become the new standard. Success will depend on innovation, precision, and adaptability.
At the center of this evolution stands the Mold Maker. They are more than just tool builders. They are problem solvers, designers, and technology experts. Their skills make it possible to produce advanced electronics at scale—quickly, sustainably, and with high quality.
By understanding the trends ahead, every Mold Maker can stay one step ahead and continue to drive the industry forward.
Would you like a downloadable PDF version of this article for sharing with clients or your team?