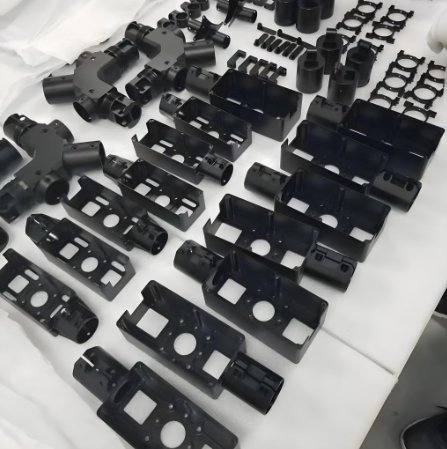
Prototypes are vital.
They test ideas fast.
They show shape and fit.
They catch problems early.
Now 3D printing changes the game.
It speeds up prototyping.
It helps every Mold Maker work smarter.
It transforms Electronic Injection Molding from idea to product.
What Is 3D Printing?
3D printing builds parts layer by layer.
It uses plastic, resin, or metal.
It follows a digital file.
This process is fast.
No molds needed.
Perfect for early design.
Traditional Prototyping vs. 3D Printing
Old methods took weeks.
CNC or soft tooling were slow.
Each change needed time and money.
3D printing is quicker.
Print one version.
Change the file.
Print again.
The Mold Maker can review and update easily.
Fewer delays.
More speed.
Helping the Mold Maker See Design Issues Early
3D printing gives physical samples fast.
You can hold the part.
You can test it.
You can check how it fits with other parts.
This helps the Mold Maker see flaws before steel is cut.
It avoids rework.
It saves cost.
Speeding Up Design Approvals
Customers want speed.
They want to see real parts.
3D printed samples make that possible.
They reduce back-and-forth emails.
They get fast sign-off.
Electronic Injection Molding projects start sooner.
Time-to-market drops.
Fit Testing and Functional Trials
Printed parts help with testing.
Fit in PCB boards.
Click into cases.
Snap onto sensors.
This is key for Electronic Injection Molding.
Fit problems slow production.
But with 3D prints, you test fast.
No risk for the Mold Maker.
No guesswork.
Supporting Low-Volume Builds
Not all jobs need thousands.
Some need just 10.
3D printing helps there.
It handles short runs.
That gives freedom.
The Mold Maker can hold off on steel tooling.
They can test market demand first.
Faster Mold Design Cycles
3D printing doesn’t just help parts.
It also helps mold design.
Engineers can print core and cavity shapes.
They can hold them.
They can check clearance and ejection.
This helps the Mold Maker fine-tune everything.
Before metal cutting starts.
Reducing Mold Revisions
Revisions are expensive.
Cutting steel again wastes time.
But 3D printing catches flaws.
Before the mold is made.
That saves money.
That helps every Mold Maker build right the first time.
3D Printed Inserts for Molds
In some cases, 3D printing helps molds directly.
You can print inserts.
You can test them in aluminum or hybrid molds.
It works for Electronic Injection Molding with complex parts.
Channels.
Slots.
Tiny features.
Fast testing.
No steel waste.
Creating Better Cooling Layouts
3D printing can help with mold cooling.
You can test cooling paths.
You can see flow.
The Mold Maker can print samples of core-cooling parts.
They try new layouts.
They avoid hot spots.
This helps the injection molding process stay consistent.
Testing Advanced Materials
Some parts need heat resistance.
Some need electrical insulation.
3D printing can test material behavior.
Try different filaments.
See how they react.
No need for long trials.
That helps Electronic Injection Molding find the right match.
Before final production.
Visualizing Assembly
3D prints help teams see how parts fit.
Mechanical parts.
Electronic boards.
Connectors.
They bring the whole unit together.
No confusion.
No wrong guesses.
The Mold Maker gets real-world clarity.
Communication Between Teams
Design.
Engineering.
Sales.
All teams need to be in sync.
3D prints help.
They show the same model.
No screen needed.
Electronic Injection Molding projects run smoother.
Decisions are faster.
Reducing Cost in the Long Run
3D printing adds up.
Not in cost—but in savings.
Less rework.
Faster tooling.
Fewer errors.
It helps every Mold Maker avoid lost time.
Better quality.
More profit.
Real-World Use Cases
Many companies use this method.
They print USB case samples.
They print test sockets.
They test switches and housings.
Electronic Injection Molding grows fast with this help.
3D printing leads the way.
Smart Integration with CAD and Simulation
3D printing works well with design tools.
CAD files go straight to the printer.
No delay.
Simulation can predict warpage.
Printing confirms shape.
The Mold Maker gets a powerful feedback loop.
Design–print–refine.
Supporting IoT and Wearables
Small parts.
Tiny circuits.
New shapes.
3D printing helps test them fast.
It’s perfect for wearables and smart tech.
Electronic Injection Molding must keep pace.
This tech helps the Mold Maker stay on track.
Reducing Material Waste
Machining removes material.
3D printing adds it.
That means less waste.
Eco-friendly.
More control.
Less cost.
It’s a big win for mold shops.
Prototype Tools for Pilot Runs
You can even print simple molds.
They are good for soft material.
They work for pilot runs.
Quick tests.
The Mold Maker gets real-world feedback.
Before final mold steel is ordered.
3D printing is not replacing molds.
But it’s changing how molds are made.
It supports design.
It speeds up approval.
It reduces errors.
Electronic Injection Molding becomes faster and smarter.
The Mold Maker becomes more efficient and precise.
Together, these tools shape the future.
One printed layer at a time.