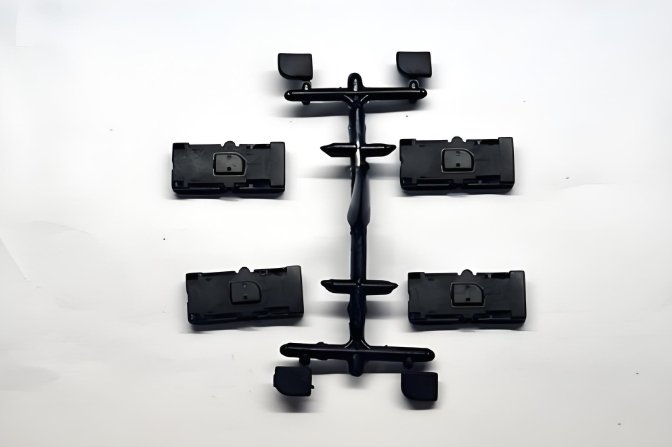
In Electronic Injection Molding, temperature matters.
A lot.
Every mold must stay at the right temperature.
Too hot or too cold can cause problems.
Big problems.
This is where the Mold Maker plays a key role.
They set up the system to keep the mold just right.
Let’s look at why mold temperature is so important.
Why Temperature Control Is So Important
Electronic parts are sensitive.
They need precise shapes and smooth surfaces.
They must also fit perfectly into other components.
If the mold is too cold, the plastic freezes too fast.
This causes short shots, sink marks, or warping.
If it’s too hot, the part may not cool properly.
This leads to deformation, burns, and long cycle times.
In Electronic Injection Molding, every part must be perfect.
Even small defects can ruin an entire device.
That’s why Mold Maker professionals always focus on temperature.
The Role of the Mold Maker
A skilled Mold Maker doesn’t just make molds.
They build smart systems.
Systems that keep the mold temperature stable.
They choose the right materials.
They design good cooling channels.
They test the system before production.
Their work keeps the mold from overheating.
It also helps the parts stay consistent and strong.
What Happens If Temperature Is Not Controlled?
Without good temperature control, problems appear fast.
1. Poor Surface Finish
Cold molds can cause rough surfaces.
The plastic doesn’t flow properly.
Parts look dull or scratched.
2. Warping and Shrinking
Hot spots in the mold cause uneven cooling.
This leads to warping or shrink marks.
In Electronic Injection Molding, this is a serious issue.
3. Inconsistent Part Sizes
Even small changes in temperature affect the final part size.
That’s a big problem in electronics.
All parts must be exact.
4. Longer Cycle Time
If the mold is too hot, parts take longer to cool.
This means slower production and higher costs.
A Mold Maker helps fix all of these issues.
The Science Behind Mold Temperature
Plastics shrink as they cool.
If cooling is uneven, shrinkage varies.
That leads to part defects.
The mold temperature controls how fast the plastic cools.
It also affects how the material flows in the mold.
For example:
- A higher mold temperature improves flow for thin parts.
- A lower mold temperature can reduce cycle time.
In Electronic Injection Molding, balance is key.
The Mold Maker must choose the right range.
How the Mold Maker Designs for Temperature Control
Good temperature control starts with the mold design.
1. Cooling Channels
These are built into the mold.
They carry water or oil to cool the mold.
A smart Mold Maker places them near hot spots.
2. Thermal Insulation
Insulation keeps the heat where it’s needed.
It prevents heat loss and maintains stable conditions.
3. Material Choice
Some steels conduct heat better.
Others hold heat longer.
The Mold Maker selects materials based on the product.
Tools for Mold Temperature Control
Modern molds use advanced systems to manage heat.
1. Temperature Controllers
These keep the coolant at the right level.
They adjust flow and heat as needed.
2. Sensors
Sensors measure temperature inside the mold.
Data goes to the controller to make changes.
3. Flow Meters
They monitor the coolant flow.
Poor flow can cause hot or cold spots.
These tools help the Mold Maker keep everything under control.
Special Cases in Electronic Injection Molding
Some electronic parts need overmolding.
This means one material covers another.
Overmolding needs very tight temperature control.
The two materials must bond well.
Too much heat? They separate.
Too little? They don’t stick.
Temperature is also key for insert molding.
Here, plastic goes around a metal insert.
Good heat flow prevents defects.
A skilled Mold Maker knows how to manage all of this.
How to Maintain Temperature Over Time
Even the best system needs maintenance.
1. Check for Blocked Channels
Scale or rust can clog cooling channels.
That changes the flow and heat.
2. Inspect Seals and Fittings
Leaks can lead to temperature drops.
Fixing them helps keep the mold working right.
3. Calibrate Sensors
Wrong sensor data means bad temperature control.
Regular calibration avoids this.
The Mold Maker usually sets up a maintenance schedule.
Benefits of Good Temperature Control
When the mold temperature is just right, everything works better.
- Parts look better.
- Parts fit better.
- Production is faster.
- Less waste.
- Less machine downtime.
In Electronic Injection Molding, that means big savings.
It also means happier customers.
Mold temperature is not just a number.
It’s a major part of making good electronic parts.
Too hot or too cold can ruin the product.
It can also damage the mold.
A smart Mold Maker knows how to keep it under control.
They design the mold to handle the heat.
They use tools to monitor and adjust temperatures.
They make sure every part is right.
In Electronic Injection Molding, temperature control means quality.
It also means speed, safety, and success.
So if you want better parts, start with better temperature control.
And trust a skilled Mold Maker to get the job done right.