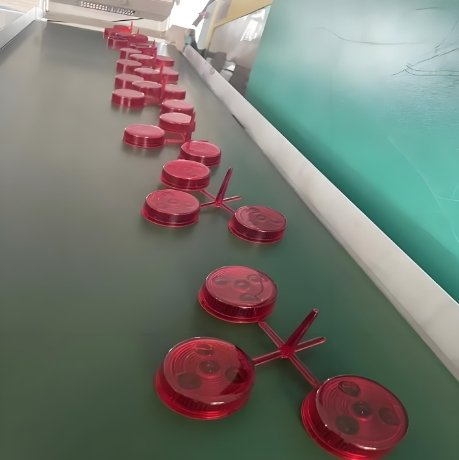
In Electronic Injection Molding, temperature matters.
It affects flow, cooling, shrinkage, and strength.
Mold temperature is a key factor.
It changes how parts look and how they work.
Every Mold Maker must focus on this.
If temperature is wrong, defects will follow.
Let’s explore why temperature control is so important.
What Is Mold Temperature Control?
Mold temperature control means managing heat inside the mold.
It keeps the tool at a steady heat level.
This helps molten plastic flow better.
It also helps the part cool the right way.
In Electronic Injection Molding, this is a big deal.
Electronics need precise shapes.
They also need good surface finishes.
Any mistake in heat control can ruin the part.
Why Temperature Affects Molded Electronic Parts
Plastic flows better at the right temperature.
If it’s too cold, it stops early.
If it’s too hot, it burns or warps.
Proper heat also affects cooling.
Faster cooling can lead to warping.
Slower cooling can cause sink marks.
In Electronic Injection Molding, balance is everything.
A skilled Mold Maker understands this.
They set the temperature just right.
Common Issues from Bad Temperature Control
Here are some common problems caused by poor control:
1. Warping
Uneven cooling leads to bending.
Electronic housings must stay flat.
If not, they won’t fit other parts.
2. Short Shots
Plastic may not reach all areas.
This makes the part incomplete.
It often happens when the mold is too cold.
3. Sink Marks
Thicker areas cool slowly.
This causes dents or marks on the surface.
It ruins the look of the product.
4. Flash
If the mold gets too hot, plastic leaks out.
This extra material is called flash.
It must be trimmed, wasting time and money.
5. Poor Surface Finish
The part may look dull or rough.
A bad finish hurts the final product.
A good Mold Maker prevents these problems.
They use smart heat control tools.
Benefits of Proper Mold Temperature Control
Better Flow
Plastic moves smoothly into all areas.
This reduces air traps and short shots.
Higher Strength
Controlled cooling makes stronger parts.
This is key in Electronic Injection Molding.
Electronics often face heat and stress.
Tight Tolerances
Correct temperature prevents shrinkage issues.
This keeps the part within specs.
Better Surface Quality
Shiny and smooth surfaces look more professional.
They also improve function in touch-sensitive parts.
Fewer Defects
Less warping, fewer sink marks, and no flash.
That saves time and cost.
Tools for Mold Temperature Control
Mold Makers use different tools to manage temperature.
1. Water Lines
Cool water flows through mold channels.
It removes heat after each cycle.
2. Oil Heating
Oil is used for higher temperature needs.
It stays more stable at high heat.
3. Thermocouples
These sensors check real-time temperatures.
They help keep things steady.
4. Temperature Controllers
They manage heat levels automatically.
They adjust flow based on need.
These tools help in every stage of Electronic Injection Molding.
Choosing the Right Temperature
Every material needs a different mold temperature.
ABS, PC, and Nylon all behave differently.
A good Mold Maker checks the material first.
They look at thickness, flow length, and shape.
Then they test different temperatures.
They find the best one for part quality.
They also monitor changes during production.
Even small changes can cause big issues.
Temperature Zones in the Mold
Most molds have multiple heat zones.
These zones may need different settings.
Core and Cavity
The cavity might need more heat.
The core might need faster cooling.
Gate Area
This part needs steady flow.
If it cools too fast, it can block flow.
Thin Walls
Thin sections cool fast.
Too much cooling leads to short shots.
Mold Makers plan each zone carefully.
They use thermal simulations to help.
Electronic Parts That Need Tight Control
Some electronic parts need extra care:
- Connectors
- Sensor housings
- Switch covers
- Light guides
- Circuit board holders
These parts must meet strict sizes.
They must also be strong and heat-resistant.
Electronic Injection Molding must deliver all that.
So mold temperature becomes critical.
How a Mold Maker Solves Temperature Problems
A good Mold Maker does many things:
- Chooses the right mold steel
- Plans water line paths
- Adds sensors in key spots
- Designs for even wall thickness
- Tests for hot spots and cold zones
They also work with production teams.
They help adjust settings as needed.
This keeps quality high every time.
Tips for Maintaining Temperature Control
Here are some best practices:
- Clean water lines often
- Check sensors and controllers regularly
- Use flow meters to monitor coolant
- Avoid sharp corners in mold design
- Insulate hot runner areas when needed
Every step helps.
In Electronic Injection Molding, small changes make big effects.
Long-Term Impact of Poor Control
Ignoring temperature leads to:
- More rejects
- Slower cycles
- Shorter mold life
- Higher costs
A smart Mold Maker avoids all this.
They plan ahead and monitor closely.
Temperature control is not a side task.
It’s a core part of mold design.
Electronic Injection Molding demands perfection.
Every part must fit and function.
Temperature plays a key role.
It affects flow, shape, strength, and finish.
A skilled Mold Maker knows this well.
They design molds with heat in mind.
They also manage heat during production.
Good temperature control means:
- Better parts
- Less waste
- Lower costs
If you want top-quality electronic parts,
start with proper mold temperature control.
And always work with a trusted Mold Maker.