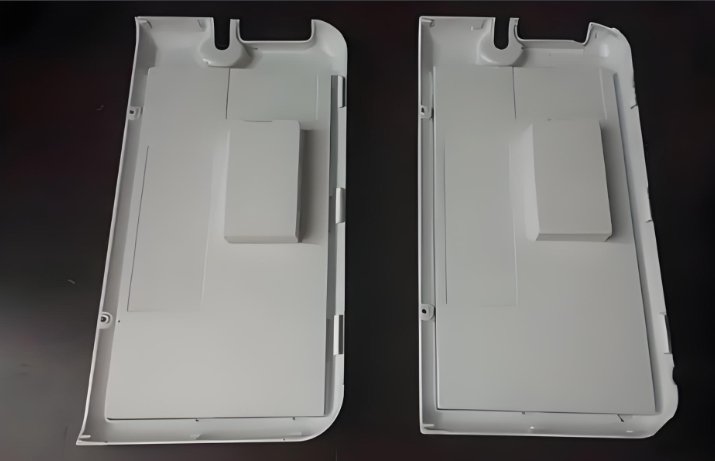
In today’s high-tech manufacturing world, smart materials are making a big difference. They respond to changes in temperature, pressure, electricity, and even light. These materials are now entering the field of Electronic Injection Molding. As a result, every Mold Maker must understand how this change impacts design, tooling, and production processes.
This article explains how smart materials are affecting Electronic Injection Molding, and how this impacts the role of the modern Mold Maker. With the growing demand for flexible, durable, and high-performance electronics, smart materials are no longer a niche solution—they are becoming the standard.
What Are Smart Materials?
Smart materials have properties that can change under different conditions. Some can return to their original shape after being bent. Others change color or hardness when exposed to electricity or heat. Some common types include:
- Shape memory polymers
- Conductive polymers
- Thermochromic plastics
- Piezoelectric materials
- Self-healing polymers
These advanced materials open new doors in the electronics industry. For example, devices can become smaller, more flexible, and more energy-efficient. But molding them is not always simple. That’s where innovation in Electronic Injection Molding and the skills of a top Mold Maker come into play.
Why Smart Materials Matter in Electronics
Electronics are getting smaller, smarter, and more efficient. Smart materials support this shift by offering new performance features. For example, a polymer that responds to heat can help regulate the temperature in a device. Or a flexible conductive plastic can help create bendable electronics.
With Electronic Injection Molding, these materials can be formed into exact shapes. This makes it easier to mass-produce smart electronic parts. But they require special handling. Not all molds or molding machines can manage their unique behaviors.
This means the Mold Maker has a larger responsibility. Molds must account for how the material reacts during and after molding. This includes shrinkage, cooling, and post-mold performance.
New Challenges for the Mold Maker
Smart materials are not like traditional plastics. They can be sensitive to processing temperatures. They may need special flow paths inside the mold. Some even require multi-material overmolding or precise alignment of embedded circuits.
For a Mold Maker, this creates new challenges. They must design molds that can process the material without damaging it. They must ensure perfect surface finishes, exact cavity temperatures, and tight tolerances. If not, the smart properties might not work as expected.
In Electronic Injection Molding, poor mold design could lead to failed functionality in the final product. So, the Mold Maker must now combine mechanical expertise with an understanding of material science and electronics.
Better Designs with Simulation and Testing
To deal with smart materials, simulation has become more important than ever. Engineers use computer tools to test mold flow, shrinkage, and warpage before the mold is made. This helps the Mold Maker make better design choices early in the process.
In Electronic Injection Molding, even a small mistake can lead to costly rework or electronic failure. Smart materials are sensitive to process settings. Using simulation allows for faster corrections and helps meet the demands of high-performance parts.
Post-mold testing is also critical. After molding, parts made from smart materials may need to be tested under heat, pressure, or electrical fields. This ensures the material behaves as expected.
Hybrid Molding with Smart Materials
Smart materials are often used alongside traditional plastics or electronic components. This creates a need for hybrid molding—where multiple materials or inserts are molded together.
For example, a flexible display might include a smart polymer over a rigid frame. Or a sensor part may need both a conductive polymer and a clear protective cover. Electronic Injection Molding processes can combine these in one cycle.
The Mold Maker must design for this complexity. Molds must allow precise placement of each material. They must ensure no short shots, no burning, and no material contamination. Hybrid molds are complex, but they save time and cost in assembly.
Sustainability and Waste Reduction
Smart materials can also contribute to greener manufacturing. Some are biodegradable or recyclable. Others reduce the need for additional parts, simplifying product design. This cuts down on materials and energy use.
In Electronic Injection Molding, using fewer parts means fewer assembly steps and less packaging waste. A single molded part made from a smart material might replace several older parts.
For the Mold Maker, this means designing molds for multi-functional components. These components not only do more but also last longer and break down more easily when disposed of.
Cost and Market Growth
Today, smart materials may cost more than regular plastics. But as demand rises, prices are falling. Industries like consumer electronics, medical devices, and automotive are all driving growth.
This growth is bringing more Electronic Injection Molding work. Every Mold Maker who invests in smart material processing stands to benefit. Customers want parts that offer better performance and lower weight, and smart materials make this possible.
Mold shops that stay ahead of this curve will attract new clients, especially in high-tech fields.
Training for the Future
Handling smart materials means the Mold Maker must keep learning. It’s not just about steel and cavities anymore. It’s about understanding how smart plastics behave during molding and in final use.
Training programs now include topics like advanced materials, electronics integration, and process simulation. The most successful Mold Maker will combine hands-on skill with technical knowledge.
As smart materials evolve, so will the tools, machines, and methods used to mold them.
Smart materials are changing the future of electronics. From sensors to flexible displays, they bring new possibilities to product design. Electronic Injection Molding helps bring these ideas to life—turning raw materials into useful, reliable parts.
But this shift also challenges the industry. It demands better designs, tighter control, and a deeper understanding of materials. Every Mold Maker must rise to meet this demand. The work is harder, but the reward is greater.
By mastering smart materials, a Mold Maker becomes more than just a toolmaker. They become a vital part of modern electronic innovation.
Would you like this article turned into a brochure or case study format as well?