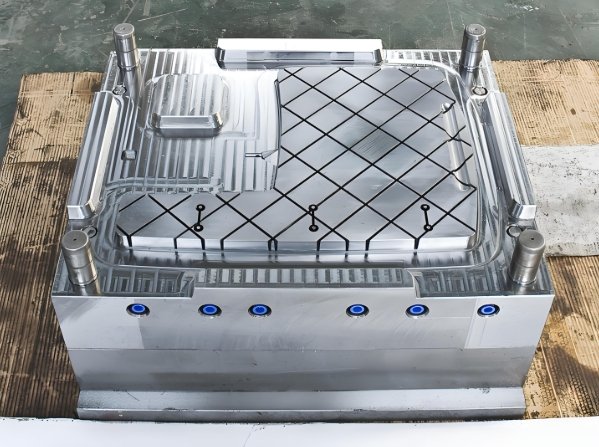
Precision drives automotive success. Automotive injection molds shape critical components. A skilled mold maker ensures strength, accuracy, and efficiency. High-quality molds create durable, flawless parts.
Why Mold Quality Matters in Automotive Manufacturing
1. Precision for Safety
Vehicle parts must fit perfectly. Automotive injection molds ensure exact dimensions. A mold maker eliminates defects.
2. Consistency for Performance
Uniformity ensures reliability. Automotive injection molds produce identical parts. A mold maker controls every detail.
3. Cost Efficiency
Defects increase waste. Automotive injection molds reduce material loss. A mold maker prevents expensive errors.
4. Faster Production
Speed matters in manufacturing. Automotive injection molds streamline production. A mold maker optimizes efficiency.
Key Features of High-Quality Automotive Injection Molds
1. High-Grade Materials
Durable steel improves longevity. Automotive injection molds use hardened alloys. A mold maker selects the best materials.
2. Advanced Cooling Systems
Heat affects performance. Automotive injection molds use efficient cooling channels. A mold maker prevents warping.
3. Precision Machining Techniques
Accuracy is critical. Automotive injection molds rely on CNC machining. A mold maker ensures flawless shaping.
4. Surface Treatment for Longevity
Wear resistance extends mold life. Automotive injection molds get special coatings. A mold maker improves durability.
Common Automotive Parts Made with Injection Molding
1. Dashboard Components
Perfect finishes matter. Automotive injection molds create smooth panels. A mold maker ensures consistency.
2. Bumpers and Grilles
Impact strength is key. Automotive injection molds shape tough bumpers. A mold maker enhances durability.
3. Engine Covers and Air Ducts
Heat resistance is vital. Automotive injection molds form strong engine parts. A mold maker selects heat-resistant plastics.
4. Interior Trim and Door Panels
Aesthetics require precision. Automotive injection molds shape elegant designs. A mold maker guarantees smooth surfaces.
5. Lighting and Lens Covers
Clarity ensures visibility. Automotive injection molds produce clear housings. A mold maker prevents defects.
Advanced Techniques in Automotive Injection Molding
1. Gas-Assisted Injection Molding
Hollow parts reduce weight. Automotive injection molds use gas assistance. A mold maker enhances efficiency.
2. Two-Shot Molding
Multi-layer designs need precision. Automotive injection molds combine materials. A mold maker ensures strong bonds.
3. Insert Molding
Metal and plastic integrate seamlessly. Automotive injection molds create hybrid parts. A mold maker improves structural strength.
4. Overmolding for Soft Touch Components
Comfort enhances user experience. Automotive injection molds add soft layers. A mold maker refines finishes.
How Mold Makers Ensure High Standards
1. Design Optimization
Every detail affects performance. Automotive injection molds undergo rigorous design checks. A mold maker analyzes weak points.
2. Mold Flow Simulation
Software predicts material behavior. Automotive injection molds use simulations for accuracy. A mold maker prevents defects early.
3. Automated Quality Control
Technology detects inconsistencies. Automotive injection molds integrate AI inspections. A mold maker ensures precision.
4. Maintenance and Upgrades
Longevity depends on care. Automotive injection molds require routine servicing. A mold maker prevents breakdowns.
Materials Used in Automotive Injection Molding
1. Polypropylene (PP)
Lightweight and strong. Automotive injection molds use PP for dashboards. A mold maker ensures flexibility.
2. Acrylonitrile Butadiene Styrene (ABS)
Toughness matters. Automotive injection molds rely on ABS for trim panels. A mold maker enhances impact resistance.
3. Polycarbonate (PC)
Transparency is essential. Automotive injection molds shape clear lenses. A mold maker prevents scratches.
4. Nylon (PA)
Heat-resistant and durable. Automotive injection molds use nylon for engine parts. A mold maker ensures strength.
Challenges in Automotive Injection Molding
1. Tight Tolerances
Minor errors affect assembly. Automotive injection molds must be precise. A mold maker maintains strict tolerances.
2. Heat and Cooling Issues
Uneven temperatures cause defects. Automotive injection molds need efficient cooling. A mold maker prevents warping.
3. Material Selection
Not all plastics work. Automotive injection molds require specialized resins. A mold maker chooses the right formula.
4. Sustainability Requirements
Eco-friendly solutions matter. Automotive injection molds now use recycled plastics. A mold maker reduces waste.
The Future of Automotive Injection Molding
1. Smart Molding Technology
Automation enhances efficiency. Automotive injection molds now feature AI adjustments. A mold maker ensures perfect results.
2. Lightweight Materials for EVs
Electric cars need weight reduction. Automotive injection molds use composite plastics. A mold maker adapts to new demands.
3. Recycled and Bio-Based Plastics
Sustainability drives innovation. Automotive injection molds integrate green materials. A mold maker focuses on eco-friendly production.
4. 3D-Printed Molds for Faster Prototyping
Speed matters in development. Automotive injection molds now use rapid prototyping. A mold maker accelerates design validation.
High-quality automotive injection molds improve vehicle performance. A skilled mold maker ensures precision, durability, and efficiency. Advanced techniques and smart technology drive the future of automotive manufacturing.