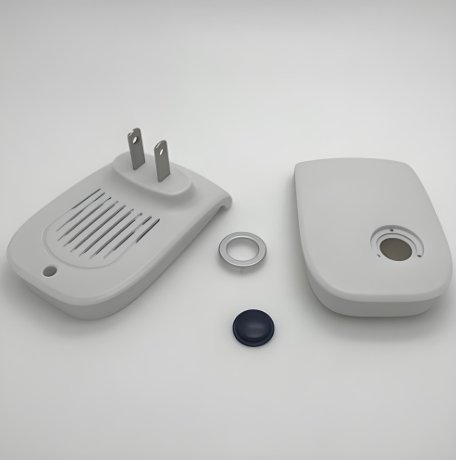
Nanomaterials are reshaping the future of Electronic Injection Molding. These tiny materials, often smaller than 100 nanometers, are offering massive benefits for manufacturers and every Mold Maker involved in the process. Their unique properties—like improved strength, conductivity, and thermal resistance—are helping create better electronic parts while supporting more efficient and sustainable production methods.
This article will explore how nanomaterials are changing Electronic Injection Molding, what it means for today’s Mold Maker, and why this trend is only expected to grow in the years ahead.
What Are Nanomaterials?
Nanomaterials are materials that contain particles so small they can only be seen with powerful microscopes. Despite their tiny size, they often show powerful properties that differ greatly from the same material in larger form.
For example, carbon becomes stronger and more conductive at the nanoscale. Silver gains antibacterial properties. Polymers become tougher and more resistant to heat. These advanced features are making nanomaterials very useful in modern manufacturing—including Electronic Injection Molding.
Why Nanomaterials Matter in Electronic Injection Molding
Electronic Injection Molding is all about precision. Products like circuit housings, sensors, switch casings, and electronic connectors must meet tight tolerances and high performance standards. Small changes in material quality can have a big impact on final performance.
Nanomaterials offer several advantages in this area:
1. Enhanced Mechanical Strength
Adding nanoparticles to plastic resins improves their mechanical strength. This means the molded parts are more resistant to stress, impacts, or warping. For a Mold Maker, this means longer tool life and more consistent part quality.
2. Better Thermal Conductivity
Many electronic components generate heat. Nanomaterials like graphene or boron nitride improve the thermal conductivity of molded parts, helping electronics stay cool. These heat-dissipating materials allow engineers to pack more features into smaller spaces.
3. Improved Electrical Conductivity
Certain nanomaterials, like carbon nanotubes or silver nanoparticles, allow molded plastics to conduct electricity. This helps in making advanced electronic parts like EMI shielding, static-control housings, or flexible circuit components.
4. Enhanced Barrier Properties
Nanomaterials also improve moisture resistance. This is crucial for electronics that need to perform in humid or harsh environments. For Electronic Injection Molding, better barrier protection helps increase product life.
Nanomaterials and the Mold Maker
The growing use of nanomaterials is also changing the work of the Mold Maker. Here’s how:
1. Tool Surface Engineering
Some nanofilled resins are more abrasive than traditional plastics. This means molds must be designed with stronger steel or special coatings to reduce wear and tear. A Mold Maker must now consider not just the part shape but also the resin composition when choosing tool materials.
2. Improved Mold Design
Nanocomposite materials sometimes flow differently than standard resins. A Mold Maker must understand how these materials behave in the mold cavity. They might need to redesign gates, runners, or venting systems to ensure proper filling and avoid defects.
3. Quality Control and Repeatability
Nanomaterials require strict processing conditions. Even small temperature or pressure changes can affect their performance. For Electronic Injection Molding, this means the Mold Maker must design molds that support precise process control and repeatability.
Applications of Nanomaterials in Electronics
The use of nanomaterials in Electronic Injection Molding is already growing across multiple sectors:
Consumer Electronics
Nanocomposites are used in smartphone housings, connectors, and internal parts to reduce size and weight without sacrificing strength.
Automotive Electronics
Modern vehicles rely on a wide range of electronic sensors and control units. Nanomaterials help reduce part size while improving durability under extreme temperatures.
Medical Devices
Medical electronics demand biocompatibility and reliability. Nanomaterials offer both, especially when used in device enclosures and flexible circuits.
Telecommunications
High-speed devices need electromagnetic shielding. Nanofilled plastics can replace metal parts, offering the same protection with less weight and more design freedom.
Environmental Benefits of Nanomaterials
Nanomaterials also support sustainability in Electronic Injection Molding:
- Material Efficiency: Since they enhance performance, less raw material is needed.
- Lighter Products: Lower product weight reduces shipping and energy costs.
- Durable Parts: Products last longer, reducing electronic waste.
- Lower Processing Temps: Some nanocomposites mold at lower temperatures, saving energy.
These benefits align well with the goals of a green Mold Maker and an eco-conscious manufacturing process.
Challenges to Consider
Despite the benefits, using nanomaterials also presents some challenges:
Cost
Nanomaterials can be expensive, especially those like graphene or silver. Manufacturers must balance performance gains with material cost.
Safety and Handling
Because nanoparticles are so small, they may pose inhalation risks if not handled properly. Safe material handling practices are essential.
Process Control
Precise molding conditions are required to keep the nanomaterials evenly dispersed. This increases the need for tight process monitoring and skilled operators.
For every Mold Maker, understanding these challenges helps prevent surprises during tool trials or production runs.
Future Outlook
The use of nanomaterials in Electronic Injection Molding is expected to grow rapidly in the next 5–10 years. As the cost of nanoparticles falls and processing methods improve, they will become more accessible to a wider range of manufacturers.
For the Mold Maker, this presents both a challenge and an opportunity. Staying up to date with nanomaterial trends can lead to better mold designs, stronger customer relationships, and entry into more advanced markets.
The Mold Maker of the future will not only be a tooling expert but also a material advisor—working closely with clients to choose the right resin, filler, and molding process to meet technical and environmental goals.
Nanomaterials are redefining what is possible in Electronic Injection Molding. They are helping manufacturers produce lighter, stronger, smarter, and greener electronic components.
For the Mold Maker, this means a new level of responsibility and expertise. Designing molds for nanocomposite materials requires more precision, better planning, and a deep understanding of material behavior.
As demand for high-performance electronics increases, nanomaterials will play a bigger role in shaping the future of manufacturing. Those who embrace this change—especially in the world of Electronic Injection Molding—will find new opportunities to grow, innovate, and lead.