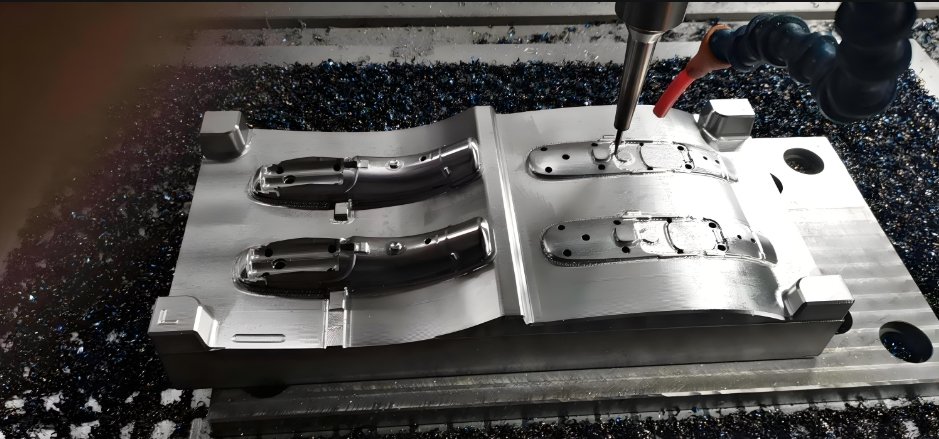
Electronics are getting smaller.
They also need more precision.
Each part must fit just right.
Every detail matters.
That’s where Electronic Injection Molding comes in.
And to do it well, we need Mold Flow Analysis.
Every skilled Mold Maker knows this.
It’s now a must in every project.
What Is Mold Flow Analysis?
It’s a digital test.
Before we cut any steel.
This software simulates plastic flow.
It shows how it fills the mold.
We see:
- Pressure
- Flow speed
- Cooling behavior
- Warping risk
And much more.
Why Use It in Electronic Injection Molding?
Electronic parts need accuracy.
Even small warps ruin circuits.
Mold Flow helps avoid problems early.
It finds weak points in designs.
It also helps the Mold Maker fine-tune the mold.
No guesswork.
Only results.
Benefits for the Mold Maker
Designing a mold is hard.
Mistakes are costly.
Mold Flow gives clear answers.
It saves:
- Time
- Material
- Money
It also speeds up testing.
And shortens production lead times.
Every Mold Maker wants that.
Getting the Gate Right
The gate is where plastic enters.
Wrong spot = bad flow.
Mold Flow shows the best location.
It also picks the right gate size.
This avoids:
- Air traps
- Short shots
- Weld lines
In Electronic Injection Molding, that’s key.
Preventing Defects Early
Defects cost time.
And money.
Mold Flow helps stop:
- Sink marks
- Voids
- Flash
- Warping
You catch them before production.
This makes the Mold Maker’s job easier.
Simulating Temperature and Pressure
Plastic behaves differently under pressure.
The software shows pressure maps.
It also shows heat zones.
You adjust settings before running the mold.
That saves energy.
And improves part quality.
Choosing the Right Material
Not all plastics act the same.
Some flow fast.
Some cool slow.
Mold Flow helps pick the right plastic.
It tests them in the simulation.
This step is key in Electronic Injection Molding.
Because many parts are thin.
Optimizing Cooling Channels
Cooling takes the most time.
It can also cause warping.
Mold Flow shows where cooling is uneven.
You then adjust channels.
The Mold Maker adds:
- Baffles
- Inserts
- Spiral cores
This improves cooling.
And cuts cycle time.
Multiple Cavities, One Solution
Need more parts fast?
Use multi-cavity molds.
But uneven flow ruins parts.
Mold Flow tests flow balance.
It shows if cavities fill together.
This helps the Mold Maker balance layout.
Family Molds in Electronics
Some molds make different parts together.
These are family molds.
But they don’t always fill evenly.
Mold Flow checks this.
It matches sizes and shapes.
So parts fill at the same rate.
That’s important in Electronic Injection Molding.
Thin Walls and Tiny Details
Electronics often need thin parts.
And sharp edges.
These are hard to mold.
Air traps can form.
Plastic might not flow fully.
Mold Flow shows these trouble zones.
The Mold Maker fixes them before cutting.
Reducing Scrap Rates
Scrap wastes money.
And slows output.
Mold Flow predicts where scrap may form.
You can fix the design early.
That reduces trial and error.
And brings better results.
A skilled Mold Maker always uses this step.
Better Part Strength
Some parts must handle heat or pressure.
Weak spots can cause cracks.
The simulation checks:
- Fiber orientation
- Wall thickness
- Stress lines
This helps build better, stronger parts.
Especially important in Electronic Injection Molding.
Faster Time to Market
Less testing = faster delivery.
Customers want fast.
And perfect.
Mold Flow reduces mold trial rounds.
So parts get approved faster.
That helps the Mold Maker meet deadlines.
Reducing Downtime
Bad molds stop machines.
Repairs take time.
And money.
Mold Flow prevents errors before they happen.
That keeps machines running.
And workers happy.
Saving Energy
Every extra second wastes power.
By improving flow and cooling,
Mold Flow cuts cycle time.
Lower energy use helps profits.
And the planet.
That’s a win-win.
Communication with Clients
Clients want data.
They want proof.
Mold Flow reports show why changes are made.
They include:
- Fill time
- Pressure drops
- Cooling maps
This builds trust.
It helps the Mold Maker explain decisions.
Future Upgrades
Need to upgrade a mold?
Use Mold Flow first.
It checks if the changes work.
Without touching the mold.
That saves time.
And protects the mold.
How to Start
Work with a team that uses Mold Flow.
Pick a trusted Mold Maker.
Ask for simulation reports.
Check:
- Flow balance
- Cooling patterns
- Gate location
Make sure it all fits your product.
Conclusion
Mold Flow Analysis is not optional.
It is now essential.
In Electronic Injection Molding, every detail matters.
Every second counts.
Mold Flow gives control.
It shows what works.
And what doesn’t.
Every Mold Maker should use it.
Fewer defects.
Faster cycles.
Stronger parts.
That’s the future.
Start using Mold Flow today.
And build better electronic parts tomorrow.