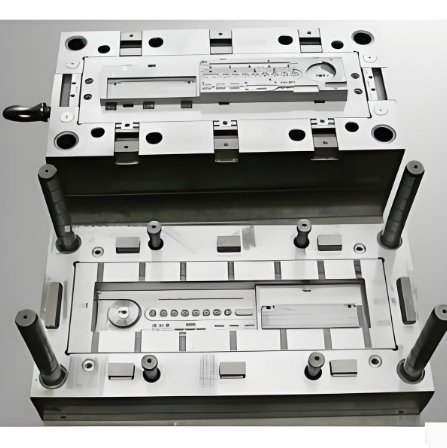
Electronic devices need precise components. Electronic injection molding ensures accuracy and consistency. Mold makers play a vital role in achieving this precision.
This article explains the science behind electronic injection molding, covering materials, processes, and innovations.
1. Understanding Electronic Injection Molding
1.1 What Is Electronic Injection Molding?
- A specialized process for electronic components.
- Uses high-precision molds to form plastic parts.
- Ensures tight tolerances for delicate applications.
1.2 Why Precision Matters
- Electronic parts must fit perfectly.
- Small variations can cause malfunctions.
- Reliable production minimizes defects.
2. The Role of Mold Makers
2.1 High-Precision Mold Design
- Uses CNC machining, EDM, and laser cutting.
- Ensures cavities match exact specifications.
2.2 Material Selection for Molds
- Hardened steel and aluminum enhance durability.
- Surface coatings improve performance.
2.3 Mold Maintenance and Quality Checks
- Regular cleaning prevents defects.
- Dimensional inspections maintain accuracy.
3. Materials Used in Electronic Injection Molding
3.1 High-Performance Polymers
- LCP (Liquid Crystal Polymer) for heat resistance.
- PBT (Polybutylene Terephthalate) for electrical insulation.
- PPS (Polyphenylene Sulfide) for stability.
3.2 Conductive Plastics
- Used for electromagnetic shielding.
- Helps in static protection.
3.3 Flame-Retardant Materials
- Meets safety standards.
- Prevents overheating and fire hazards.
4. The Injection Molding Process
4.1 Mold Design and Prototyping
- Engineers create CAD models.
- Rapid prototyping tests designs.
4.2 Material Preparation
- Resins are dried to remove moisture.
- Additives improve conductivity and strength.
4.3 Injection and Cooling
- Heated plastic is injected into the mold.
- Cooling ensures part stability.
4.4 Ejection and Finishing
- Automated systems remove parts.
- Post-processing removes excess material.
5. Process Control in Electronic Injection Molding
5.1 Temperature Control
- Precise heat management prevents defects.
- Infrared sensors monitor real-time conditions.
5.2 Pressure Regulation
- Ensures complete mold filling.
- Prevents air pockets and voids.
5.3 Automated Quality Control
- Vision systems inspect dimensions.
- Laser scanning detects irregularities.
6. Advanced Technologies in Electronic Injection Molding
6.1 Micro-Molding for Miniature Parts
- Produces small, detailed components.
- Used in microelectronics and sensors.
6.2 Overmolding for Complex Designs
- Combines multiple materials in one part.
- Improves durability and functionality.
6.3 AI and Machine Learning
- Predicts defects before they occur.
- Optimizes process parameters.
6.4 Real-Time Monitoring with IoT
- Tracks production data remotely.
- Reduces downtime and waste.
7. Applications of Electronic Injection Molding
7.1 PCB Connectors
- Precise molding ensures a secure fit.
7.2 LED Housings
- Protects delicate light components.
7.3 Medical Electronics
- Used in diagnostic and wearable devices.
7.4 Consumer Electronics
- Keyboards, chargers, and smartphone parts.
7.5 Automotive Electronics
- Sensors, circuit enclosures, and safety systems.
8. Future Trends in Electronic Injection Molding
8.1 Smart Factories
- AI-driven automation increases efficiency.
8.2 Sustainable Materials
- Biodegradable plastics reduce waste.
8.3 Nano-Molding Technology
- Produces ultra-small components.
8.4 3D Printing for Prototyping
- Speeds up mold development.
Electronic injection molding is essential for precision manufacturing. Mold makers ensure accuracy through high-quality molds and materials. As technology advances, AI and automation will further improve the process. The future promises even greater efficiency and sustainability in electronic injection molding.