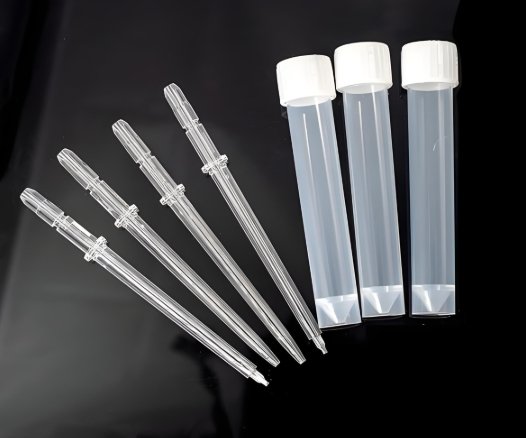
Medical devices require high precision. They must be safe, durable, and sterilization-resistant. Medical injection molding ensures high-quality production. A skilled mold maker selects the right materials. Proper material choice improves performance. It also ensures compliance with strict regulations.
1. Why Material Selection Matters
Ensuring Patient Safety
Medical plastics must be biocompatible. They cannot cause allergic reactions or toxicity.
Durability and Strength
Medical devices face stress, impact, and chemicals. The right plastic prevents cracks and failures.
Sterilization Resistance
Medical tools undergo heat, radiation, or chemical sterilization. Materials must withstand these processes.
Regulatory Compliance
The FDA and ISO set strict standards. Medical plastics must meet safety requirements.
2. Key Properties of Medical-Grade Plastics
1. Biocompatibility
Plastics must not harm the body. They must pass USP Class VI and ISO 10993 testing.
2. Chemical Resistance
Medical plastics must resist drug exposure. They cannot degrade when in contact with chemicals.
3. Heat Resistance
Autoclave sterilization uses high heat. The material must not warp or degrade.
4. Impact Strength
Devices must not break under pressure. A strong mold maker ensures precise molding.
5. Transparency or Opacity
Some applications need clear plastics. Others require opaque materials for protection.
3. Common Medical-Grade Plastics
1. Polycarbonate (PC)
- High impact resistance.
- Transparent and strong.
- Withstands gamma and chemical sterilization.
2. Polypropylene (PP)
- Lightweight and flexible.
- Can be autoclaved.
- Used in syringes and IV components.
3. Polyether Ether Ketone (PEEK)
- Extreme strength and heat resistance.
- Handles repeated sterilization.
- Used in implants and surgical tools.
4. Polysulfone (PSU)
- Tough and transparent.
- Resists chemicals and heat.
- Used in filtration devices.
5. Polyvinyl Chloride (PVC)
- Flexible and low cost.
- Used in tubing and blood bags.
- Compatible with chemical sterilization.
6. Acrylonitrile Butadiene Styrene (ABS)
- Rigid and lightweight.
- Used in diagnostic equipment.
- Resists gamma and EtO sterilization.
7. Silicone
- Soft and biocompatible.
- Used in implants and catheters.
- Handles heat and chemical sterilization.
4. Choosing the Right Material for Medical Injection Molding
Application-Based Selection
Different devices require different plastics. A mold maker selects materials based on function.
Sterilization Compatibility
Some plastics degrade under heat or radiation. The right material must withstand sterilization.
Mechanical and Chemical Properties
Plastics must resist stress, impact, and chemicals.
Cost vs. Performance
Some medical plastics are expensive. A mold maker finds cost-effective solutions.
5. Role of a Mold Maker in Medical Injection Molding
Material Testing and Selection
A mold maker tests plastics for durability and safety.
Mold Design and Engineering
The mold must ensure precise, defect-free production.
Injection Molding Process Control
Molding conditions affect material performance.
Quality Assurance and Compliance
Devices must meet FDA and ISO standards. Testing ensures safety.
6. Challenges in Medical Injection Molding
Material Degradation
Some plastics weaken over time. A mold maker selects stable materials.
Strict Regulatory Approval
Meeting medical standards requires extensive testing.
High Manufacturing Costs
Advanced medical plastics are expensive. Optimizing production reduces costs.
Complex Mold Designs
Medical parts require high precision. A skilled mold maker ensures accuracy.
7. Innovations in Medical Injection Molding Materials
Biodegradable Medical Plastics
Eco-friendly materials reduce medical waste.
Smart Polymers
Self-healing and drug-releasing plastics improve medical applications.
Nanotechnology-Enhanced Plastics
Nanomaterials improve strength and antimicrobial properties.
Material selection is critical in medical injection molding. A skilled mold maker ensures quality, durability, and compliance. Advanced plastics improve medical device performance.