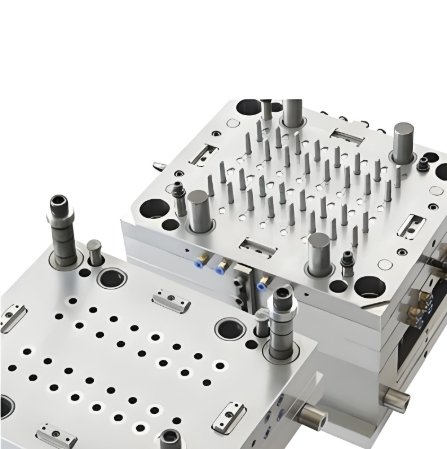
Medical devices require precision. Medical injection molding ensures accuracy. A skilled mold maker delivers high-quality parts. This process is vital for healthcare advancements.
1. What is Medical Injection Molding?
Definition
Medical injection molding creates plastic medical components. It ensures consistency and precision.
How It Works
Molten plastic is injected into a mold. The shape hardens into a precise medical part.
Importance in Healthcare
Medical products need strict standards. This process guarantees safety and accuracy.
2. Benefits of Medical Injection Molding
High Precision Production
Even the smallest details are accurate. Perfect for surgical tools and implants.
Cost-Effective Manufacturing
Mass production reduces costs. More products, less waste.
Biocompatibility
Materials used are safe for human contact. Ensures no harmful reactions.
Scalability
Production can be small or large. Adaptable to demand.
Fast Production Cycles
Automation speeds up manufacturing. Critical for urgent medical needs.
3. Role of a Mold Maker in Medical Injection Molding
Custom Mold Design
A mold maker creates precise molds. Designs fit medical specifications.
Material Selection Expertise
Choosing the right plastic is crucial. Biocompatible and durable materials are required.
Ensuring Tight Tolerances
Molds must be exact. Even minor defects can cause failure.
Long Mold Lifespan
A high-quality mold lasts for many cycles. Ensures consistent production.
4. Common Medical Products Made with Injection Molding
Surgical Instruments
Scalpels, forceps, and retractors need high precision.
Implantable Devices
Pacemakers, joint replacements, and stents use biocompatible plastics.
Diagnostic Equipment
Test tubes, sample containers, and lab trays require strict accuracy.
Drug Delivery Systems
Syringes, inhalers, and insulin pens must be defect-free.
IV Components
Valves, tubing, and connectors are mass-produced efficiently.
5. Materials Used in Medical Injection Molding
Thermoplastics
- Polycarbonate (PC) – Strong and impact-resistant.
- Polypropylene (PP) – Lightweight and chemical-resistant.
- Polyetheretherketone (PEEK) – High heat resistance.
Silicone Rubber
Flexible and biocompatible. Used in medical tubing.
Bio-Resorbable Polymers
Dissolve in the body over time. Used for sutures and implants.
6. Cleanroom Injection Molding
Why Cleanrooms Matter
Medical parts must be sterile. Contaminants can cause infections.
Types of Cleanroom Molding
- ISO Class 7 (10,000 particles per cubic foot)
- ISO Class 8 (100,000 particles per cubic foot)
Strict Hygiene Protocols
Workers wear protective gear. Machines are sterilized regularly.
7. Quality Control in Medical Injection Molding
Inspection Techniques
- Visual Inspections – Detects surface defects.
- Automated Scanning – Ensures precision.
- Dimensional Testing – Confirms exact measurements.
Compliance with Regulations
- FDA Approval – Ensures product safety.
- ISO 13485 Certification – Guarantees quality standards.
- Good Manufacturing Practices (GMP) – Maintains consistency.
8. Advanced Injection Molding Techniques for Healthcare
Micro-Molding
Used for tiny medical parts. Critical for minimally invasive surgery.
Overmolding
Combines materials for better functionality. Common in medical grips.
Insert Molding
Encapsulates metal components in plastic. Used for surgical handles.
9. Choosing the Right Medical Mold Maker
Experience in Medical Molding
A reliable mold maker has years of expertise. Specialization ensures quality.
Technology and Equipment
Modern facilities use automated systems. Increases accuracy and speed.
Prototyping Capabilities
Testing before production reduces risks. Ensures perfect designs.
Regulatory Compliance
Certified manufacturers follow strict guidelines. Guarantees patient safety.
10. Medical Injection Molding for Emergency Situations
Rapid Production of Medical Supplies
Pandemics require fast manufacturing. Injection molding meets demand.
Scalability for High Demand
Large-scale production ensures supply. Crucial for emergency response.
Cost-Effective Mass Production
More products at lower costs. Helps reduce healthcare expenses.
11. Innovations in Medical Injection Molding
3D Printing for Prototyping
Speeds up mold development. Reduces trial-and-error.
AI-Powered Quality Control
Automated systems detect defects. Ensures zero errors.
Sustainable Medical Plastics
Eco-friendly materials reduce waste. Biodegradable options available.
12. Reducing Errors in Medical Injection Molding
Strict Quality Checks
Every part undergoes inspection. Ensures accuracy.
Advanced Sensor Technology
Detects molding defects instantly. Reduces product failures.
Regular Mold Maintenance
A well-maintained mold lasts longer. Prevents manufacturing issues.
13. Future Trends in Medical Injection Molding
Smart Medical Devices
Wearable tech requires precision molding. Increases patient monitoring efficiency.
Biodegradable Implants
Dissolvable medical plastics improve treatment. Eliminates secondary surgeries.
Nano-Molding for Microscopic Devices
Tiny devices improve drug delivery. Revolutionizing medical treatments.
14. Selecting the Best Injection Molding Partner
Check Certifications
ISO 13485 and FDA approval ensure quality.
Review Case Studies
Successful projects prove reliability.
Assess Production Capabilities
High-volume production ensures scalability.
Ensure Strong Communication
A good partner offers full transparency.
Medical injection molding is essential for healthcare. A skilled mold maker ensures high precision, safety, and cost-efficiency. Choosing the right manufacturer guarantees top-quality medical products.