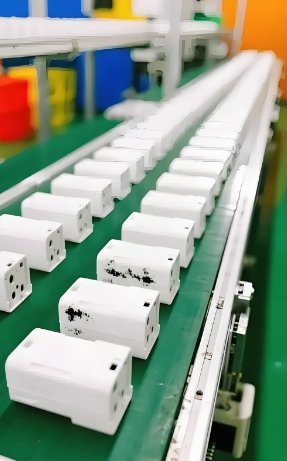
In the world of plastic product manufacturing, selecting the right injection molding method is crucial—especially for complex parts like plastic housings. Whether you’re producing electronic casings, automotive panels, or medical device enclosures, your success depends on two critical factors: the injection molding method and the quality of your mold maker.
This article explains the major types of housing injection molding techniques. It compares their benefits, limitations, and applications. We’ll also discuss how a professional mold maker shapes the outcome of your project. You’ll find out which method best fits your product’s size, complexity, and volume.
By the end, you’ll know how to make the right decision for your plastic housing—and how to work with a skilled mold maker to achieve excellent results.
Why Injection Molding Is Ideal for Housings
Before diving into the types of injection molding, let’s answer a bigger question: why use injection molding at all?
Housing injection molding is the leading choice because it creates strong, high-precision plastic parts. It allows manufacturers to achieve tight tolerances, detailed designs, and complex features. Whether you’re making 500 or 500,000 parts, this method ensures consistency, speed, and surface quality.
More importantly, when paired with an experienced mold maker, this process delivers superior results every time.
Different Injection Molding Methods Explained
1. Traditional Injection Molding
This is the most widely used housing injection molding method. Plastic pellets are melted and injected into a mold cavity, which cools and solidifies into the desired shape.
Best For:
- Medium to high production volumes
- Detailed, high-strength parts
- Tight dimensional tolerances
Pros:
- Excellent repeatability
- Strong mechanical properties
- Broad material selection
- Compatible with automation
Cons:
- High upfront tooling costs
- Mold lead times can be long
- Requires a skilled mold maker
2. Overmolding
Overmolding combines two or more materials into one part. A soft plastic or rubber is molded over a hard plastic substrate.
Best For:
- Ergonomic housings
- Seals, grips, and bumpers
- Multi-color or multi-texture designs
Pros:
- Improved aesthetics
- Better function (like grip or water sealing)
- Simplifies assembly
Cons:
- Higher part cost
- More complex mold design
- Demands an advanced mold maker
3. Insert Molding
In insert molding, metal or pre-formed components (like threaded inserts) are placed into the mold before the plastic is injected.
Best For:
- Structural housings needing metal parts
- Electrical components
- Durable threaded holes
Pros:
- Integrates components
- Reduces assembly time
- Enhances part strength
Cons:
- Requires manual or robotic insert placement
- Complex mold design
- Needs expert mold maker support
4. Gas-Assisted Injection Molding
This method uses gas (usually nitrogen) to push molten plastic against the mold wall, forming hollow sections inside the part.
Best For:
- Large, thick-walled housings
- Automotive or furniture parts
- Reducing weight and warping
Pros:
- Lighter parts
- Lower material cost
- Fewer sink marks
Cons:
- Limited material options
- Requires special equipment
- Demands a highly experienced mold maker
5. Micro Injection Molding
This is used to produce tiny, detailed plastic parts, often under 1 gram.
Best For:
- Small electronic or medical housings
- Precision optical components
Pros:
- High accuracy at micro scale
- Minimal material waste
Cons:
- Expensive equipment
- Highly sensitive to errors
- Needs a specialized mold maker
How a Mold Maker Shapes the Process
No matter the method, the mold is the heart of housing injection molding. And the mold maker is the person who creates that heart.
A skilled mold maker works closely with engineers to:
- Optimize mold flow and cooling
- Select the right steel for mold life
- Add draft angles and ejector systems
- Reduce flash, warping, and sink marks
- Shorten cycle times without affecting quality
The better your mold maker, the more efficient your production process—and the fewer issues you’ll face in mass production.
Factors That Help You Choose the Right Molding Method
Choosing the best housing injection molding method depends on your specific needs. Consider these key questions:
What is the production volume?
- Low to medium volumes might justify micro or insert molding.
- High volumes favor traditional or gas-assisted molding for long-term savings.
What are the part requirements?
- Strength and rigidity? Go for gas-assisted or insert molding.
- Comfort and texture? Overmolding provides the best feel.
- Tiny details or small size? Use micro molding.
What’s your budget?
- Complex methods cost more upfront.
- However, they can reduce post-processing and assembly costs.
How important is part appearance?
- If surface finish and uniformity are critical, standard housing injection molding or overmolding is ideal.
Case Example: Choosing the Right Method for a Consumer Product
Let’s say you’re making a handheld remote control with soft grips and embedded metal threads for screws.
Here’s what you’ll likely use:
- Insert molding for the threaded screw bosses
- Overmolding for the rubberized grip
- All done using high-precision housing injection molding
This process would require a multi-stage mold designed by an expert mold maker. With the right strategy, you’ll reduce assembly time, lower part count, and improve product feel.
Common Mistakes to Avoid
- Skipping mold flow analysis: Without it, the plastic may not fill properly.
- Choosing a cheap mold maker: You’ll spend more fixing problems later.
- Overcomplicating the part: Keep the design simple for fast production.
- Ignoring material shrinkage: Your mold maker should adjust the cavity size accordingly.
Avoid these traps by involving your mold maker early in the project.
Conclusion: Choose What Works Best for Your Needs
Every method of housing injection molding offers unique benefits. The right choice depends on part complexity, material, cost, and function.
- Traditional molding is versatile and fast.
- Overmolding and insert molding add function and beauty.
- Micro and gas-assisted molding solve extreme needs.
But none of these will work well without a reliable mold maker. They turn your ideas into tools that produce strong, accurate, and repeatable parts.
Before you start your next project, consult with a trusted mold maker. Their insights will help you choose the right process—and make your plastic housing a success.