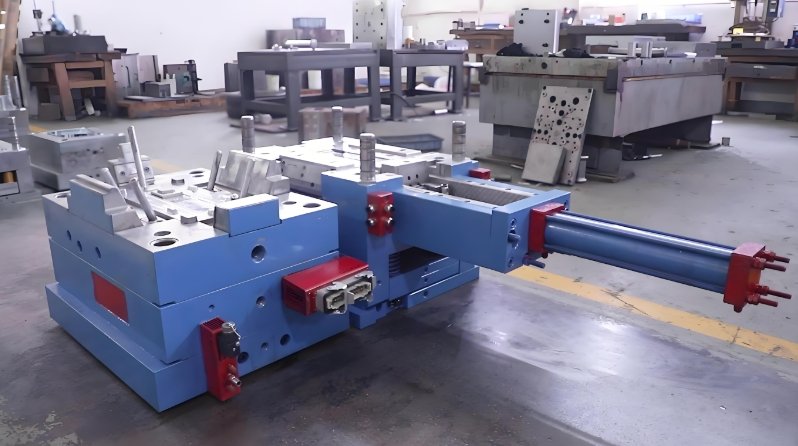
Modern electronics require extreme precision. Electronic injection molding ensures high-quality, accurate, and reliable parts. Even small errors can cause device failures. Mold makers play a key role in maintaining tight tolerances. This article explores why precision matters and how advanced molding techniques help.
1. The Importance of Precision in Electronic Components
1.1 Why Precision Matters
Electronic devices use tiny, complex parts. These parts must fit perfectly to ensure proper function. Even a small misalignment can disrupt the entire system.
1.2 Consistency in Mass Production
Millions of electronic parts are produced daily. Electronic injection molding ensures uniformity across all units. Without precision, variations in parts could lead to assembly failures.
1.3 Preventing Electrical Failures
Electronic components must connect perfectly. A poorly molded connector can cause circuit breaks, short circuits, or overheating.
2. The Role of Mold Makers in Precision Manufacturing
2.1 Designing High-Precision Molds
Mold makers create molds with exact specifications. These molds determine the final product’s accuracy.
2.2 Choosing the Right Materials
Different electronic parts need different materials. Mold makers select heat-resistant, durable, and non-conductive materials for safety and longevity.
2.3 Quality Control in Mold Making
A slight defect in a mold can ruin thousands of parts. Mold makers use precision tools and inspection techniques to ensure accuracy.
3. Key Applications of High-Precision Injection Molding in Electronics
3.1 Circuit Board Housings
Circuit boards require protective casings. These must be strong, heat-resistant, and precisely molded to fit delicate components.
3.2 Micro Connectors and Sockets
Micro-sized connectors need ultra-precise molding. These small parts must ensure perfect electrical connections.
3.3 LED Components
LED housings must allow light transmission while protecting internal parts. High-precision molding ensures proper light diffusion and heat resistance.
3.4 Switches and Buttons
Injection-molded buttons must be durable, responsive, and accurately placed within electronic devices.
4. Advanced Injection Molding Techniques for High Precision
4.1 Micro Injection Molding
This method creates ultra-small parts with extreme precision. It is essential for miniaturized electronics.
4.2 Overmolding
Overmolding combines different materials in a single part. It is used for grip-enhanced connectors and insulated components.
4.3 Insert Molding
Insert molding integrates metal or electronic elements into plastic casings. It ensures strong and secure part integration.
4.4 Liquid Silicone Rubber (LSR) Molding
LSR molding produces flexible, heat-resistant components. It is used in wearables and medical electronics.
5. Benefits of High-Precision Electronic Injection Molding
5.1 Increased Product Reliability
Precision molding ensures long-lasting, high-performance electronic components.
5.2 Lower Defect Rates
Accurate molds reduce defects, saving costs and preventing product recalls.
5.3 Improved Miniaturization
Modern electronics require smaller, more complex parts. High-precision molding supports miniaturization.
5.4 Enhanced Manufacturing Efficiency
Tighter tolerances mean fewer production errors and faster assembly.
6. Challenges in High-Precision Electronic Injection Molding
6.1 Tight Tolerances
Meeting extreme precision standards is challenging. Mold makers must maintain tolerances within microns.
6.2 Material Selection
Choosing the right plastic or composite affects part durability and performance.
6.3 Tooling Costs
High-precision molds require advanced machinery and expertise, increasing initial costs.
7. Innovations in High-Precision Injection Molding
7.1 AI-Driven Quality Control
AI detects defects in real time, improving accuracy and reducing waste.
7.2 Smart Molds
Smart molds monitor production conditions and adjust for maximum precision.
7.3 Sustainable Manufacturing
New eco-friendly materials reduce environmental impact without sacrificing precision.
8. The Future of High-Precision Electronic Injection Molding
8.1 Miniaturization Trends
Devices are getting smaller. Injection molding will continue to support ultra-compact designs.
8.2 Automation in Mold Making
Robots and AI will enhance speed and accuracy in mold maker operations.
8.3 Integration with 3D Printing
3D printing will speed up prototyping and mold testing.
High-precision electronic injection molding is essential for modern electronics. Mold makers ensure accuracy, durability, and efficiency. As technology advances, precision molding will continue shaping the future of electronics.