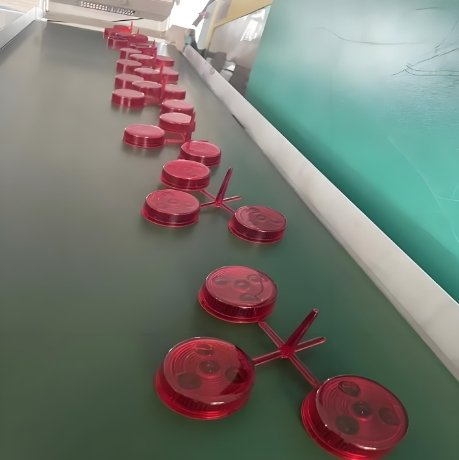
In Electronic Injection Molding, mass production is key.
It requires molds that can create many parts quickly and efficiently.
High-cavitation molds are built for this purpose.
They allow the production of multiple parts in one cycle.
This speeds up the manufacturing process and lowers costs.
Let’s dive into why high-cavitation molds are so important for mass production.
What Is a High-Cavitation Mold?
A high-cavitation mold is a mold that can produce multiple parts at once.
It has several cavities, each capable of producing a part.
The more cavities the mold has, the more parts it can make in a single cycle.
For example, a high-cavitation mold might have 8, 16, or even more cavities.
This is compared to traditional molds, which may only have 1 or 2 cavities.
High-cavitation molds are designed for efficiency.
They allow manufacturers to make large quantities of parts quickly.
This is crucial in industries like electronics, where demand can be high.
The Role of a Mold Maker in High-Cavitation Molds
A skilled Mold Maker plays an important role in designing and building high-cavitation molds.
The Mold Maker must consider many factors.
They focus on mold layout, material flow, and cooling.
The goal is to ensure that every cavity works efficiently and consistently.
1. Designing the Mold Layout
The Mold Maker must design the mold to fit multiple cavities.
Each cavity needs to be placed carefully to ensure even material flow.
If one cavity fills faster than others, it can lead to defects.
The Mold Maker uses advanced software to create a balanced layout.
2. Managing Material Flow
In high-cavitation molds, material flow is critical.
The Mold Maker ensures that plastic flows evenly into each cavity.
This helps avoid issues like air pockets or incomplete filling.
By managing the flow properly, the Mold Maker ensures that each part is made correctly.
3. Cooling the Mold
Cooling is one of the biggest challenges in high-cavitation molds.
With many cavities, the mold needs to cool quickly and evenly.
The Mold Maker designs cooling channels to ensure fast and uniform cooling.
This helps reduce cycle time and improve part quality.
Advantages of High-Cavitation Molds in Electronic Injection Molding
1. Increased Production Speed
The main benefit of high-cavitation molds is speed.
By producing multiple parts in one cycle, manufacturers can increase output.
This is especially important for mass production.
The faster parts are made, the more cost-effective the production process becomes.
2. Reduced Cycle Time
High-cavitation molds reduce the cycle time per part.
This is because more parts are produced at once.
With less time spent per cycle, production rates increase.
3. Lower Production Costs
Since high-cavitation molds produce more parts in less time, production costs go down.
Less time in the mold means reduced energy consumption.
Additionally, fewer molds are needed to produce the same number of parts.
This makes high-cavitation molds an efficient and cost-effective solution.
4. Better Consistency and Quality
High-cavitation molds help maintain consistency.
With multiple cavities, each part is produced under the same conditions.
This ensures uniformity in size, shape, and finish.
Consistent parts are crucial in Electronic Injection Molding, where precision is key.
Challenges in High-Cavitation Molds
1. Design Complexity
High-cavitation molds are more complex to design.
The Mold Maker must ensure that each cavity receives the same amount of material.
Any imbalance can lead to defects like short shots or uneven cooling.
This requires careful planning and expertise.
2. Increased Tooling Costs
The initial cost of high-cavitation molds is higher.
More cavities mean more material, precision, and effort in the mold-making process.
However, this cost is offset by the increased production speed and lower per-part costs in the long run.
3. Maintenance and Repair
With more cavities comes more potential for problems.
If one cavity wears out or becomes damaged, it can affect the entire mold.
Maintaining high-cavitation molds requires regular inspections and repairs.
A skilled Mold Maker is needed to ensure that the mold stays in top condition.
Types of High-Cavitation Molds
There are different types of high-cavitation molds used in Electronic Injection Molding.
Each type has specific advantages based on the application.
1. Single Injection Molds
These molds use one injection point to fill multiple cavities.
The plastic is injected into the mold, filling all cavities simultaneously.
This is the most common type of high-cavitation mold.
2. Multi-Point Injection Molds
In some high-cavitation molds, multiple injection points are used.
This can help improve material flow, especially for complex parts.
Multi-point injection molds are useful when the part requires a precise filling pattern.
3. Family Molds
Family molds are used when several parts need to be produced in one cycle.
Each cavity in the mold may create a different part, but all parts come from the same mold.
Family molds help reduce cycle time and improve efficiency.
How High-Cavitation Molds Improve Efficiency
Efficiency is critical in Electronic Injection Molding.
High-cavitation molds improve efficiency in several ways:
- Faster production cycles: More parts are produced in one cycle, reducing overall cycle time.
- Less downtime: High-cavitation molds produce parts faster, reducing time spent in maintenance.
- Increased throughput: With multiple cavities, manufacturers can produce larger quantities of parts in less time.
This results in a more streamlined production process and higher profitability.
When to Use High-Cavitation Molds
High-cavitation molds are ideal for mass production.
They are best used when large quantities of the same part are needed.
For example, electronic connectors, housings, and other components can be efficiently produced with high-cavitation molds.
They are also ideal for parts that require high precision and consistency.
However, for smaller production runs or complex parts, low-cavitation molds may be more suitable.
The Mold Maker will help determine the best approach based on the product and production needs.
High-cavitation molds are crucial in Electronic Injection Molding for mass production.
They allow manufacturers to produce many parts in one cycle, increasing speed and reducing costs.
A skilled Mold Maker designs these molds with precision to ensure that parts are produced efficiently and consistently.
While there are challenges involved, the benefits of high-cavitation molds far outweigh the drawbacks.
With faster production times and better quality control, high-cavitation molds are a valuable tool for any manufacturer looking to produce electronic components in high volumes.
If you’re ready to explore how high-cavitation molds can boost your production, reach out to an experienced Mold Maker to discuss your needs.