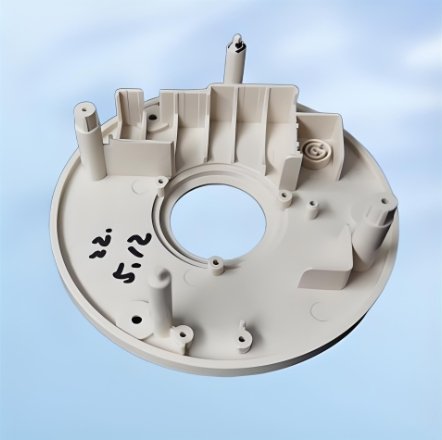
When it comes to producing high-quality plastic housings, no method compares to housing injection molding. From smartphones to automotive control units, plastic housings are all around us. Their performance depends on how well they are molded—and most importantly, how well the mold is made.
In this article, we’ll explain why housing injection molding stands out as the top choice for making durable, functional, and visually appealing plastic housings. You’ll also understand the crucial role a professional mold maker plays in the success of each project.
What Is Housing Injection Molding?
Housing injection molding is a manufacturing process where molten plastic is injected under high pressure into a precision-made mold. The plastic cools and solidifies into a defined shape, forming the outer enclosure or “housing” for various devices.
Whether the part needs to protect electronics, fit with other parts, or hold screws or clips, housing injection molding delivers unmatched precision.
The molds used in this process are built by a mold maker, who ensures that every cavity, gate, and surface matches the product’s functional and cosmetic needs.
Benefits of Housing Injection Molding
Let’s look at the many advantages housing injection molding offers over other plastic forming methods:
1. High Dimensional Accuracy
Plastic housings often need to align with other parts—such as circuit boards, connectors, or covers. That means the size must be exact. Housing injection molding provides tight tolerances, often within ±0.05 mm.
Thanks to the skills of a capable mold maker, each housing comes out nearly identical to the next, making it perfect for high-precision applications.
2. Superior Surface Finish
Today’s market demands more than just function. Products must also look good. With housing injection molding, you can achieve smooth, matte, glossy, or textured finishes directly from the mold.
There’s no need for extra sanding or painting. A seasoned mold maker can even include surface textures, logos, or fine details in the mold itself.
3. Fast Production for Large Volumes
Need thousands—or even millions—of housings? Housing injection molding is built for that. Once the mold is ready, each cycle takes just seconds to complete. The process supports mass production while maintaining consistent quality.
And when a mold maker designs the tooling for fast cooling and efficient part ejection, production speed increases without losing accuracy.
4. Material Variety for Different Requirements
Different housings need different properties. Some must be heat resistant. Others need impact strength, transparency, or UV stability. Housing injection molding supports a wide range of thermoplastics like:
- ABS
- Polycarbonate
- Nylon
- Glass-filled polymers
- TPE and TPU (for flexible parts)
A good mold maker ensures the mold matches the flow behavior and cooling needs of the selected plastic.
5. Strong and Durable Parts
Housings must protect internal components. That means they need strength. Housing injection molding creates dense, solid parts that resist cracking, deformation, or wear.
Because the material fills the mold completely, the result is a uniform structure with excellent mechanical strength. That strength begins with a properly built mold—another reason why choosing the right mold maker matters.
6. Freedom of Design
With housing injection molding, designers can include complex shapes, undercuts, screw bosses, clips, slots, and even living hinges. These features allow parts to snap together, mount securely, or open and close.
The mold maker uses their expertise to translate these features into moldable forms, using actions like side cores, lifters, or collapsible cores.
7. Minimal Waste
Compared to processes like machining or even blow molding, housing injection molding creates very little waste. Every shot is accurately metered. Any excess can often be reground and reused, reducing environmental impact.
A professional mold maker can also optimize the mold layout to minimize runner waste and increase the number of parts per cycle.
Comparing to Other Methods
You might ask: What about 3D printing, blow molding, or vacuum forming? While each has its uses, they fall short for housing production:
- 3D Printing: Great for prototyping but too slow and costly for mass production. Surface finish and strength are also limited.
- Blow Molding: Ideal for hollow parts like bottles, but cannot produce detailed housings with tight fits or inner supports.
- Vacuum Forming: Works for simple covers but lacks precision, strength, and part complexity.
Only housing injection molding combines speed, accuracy, surface finish, and part strength—especially when driven by a skilled mold maker.
The Mold Maker’s Role
The heart of any housing injection molding project is the mold. This tool defines the part’s shape, texture, dimensions, and performance. A qualified mold maker builds molds from durable steels, carefully machines each feature, and polishes the surface to perfection.
But that’s not all.
A mold maker also considers:
- Plastic flow and cooling behavior
- Ejection and demolding strategies
- Mold longevity and maintenance
- Gate and runner design for efficient filling
Without an expert mold maker, the project may suffer from defects like warping, short shots, sink marks, or flash. The best mold makers not only build molds—but also improve part design and cycle time through thoughtful tooling strategies.
Real-World Applications
Housing injection molding is used across industries:
- Electronics: Phone cases, routers, remote controls
- Automotive: Dashboard panels, control unit housings
- Medical: Monitor casings, diagnostic device housings
- Appliances: Blender bases, washing machine panels
- Industrial: Enclosures for sensors, switches, or motors
Each of these relies on consistent shape, good appearance, and strong mechanical support—all achievable through housing injection molding.
Cost vs. Quality
While mold tooling has a higher up-front cost, the long-term payoff is massive. Once the mold is built, parts can be produced for pennies. And the quality remains consistent, cycle after cycle.
Working with a trusted mold maker ensures the initial investment results in fewer defects, faster cycles, and longer mold life.
Conclusion
Housing injection molding is unmatched when it comes to making plastic housings that are strong, attractive, and consistent. With the right plastic, a high-quality mold, and a skilled mold maker, your parts will meet even the toughest standards.
This method provides the speed, flexibility, and quality needed in today’s competitive markets. While other methods may fit for short runs or non-structural parts, only housing injection molding delivers the complete package for serious housing applications.
So, if you’re looking to produce high-performance plastic housings at scale, trust the process—and partner with the right mold maker from the start.