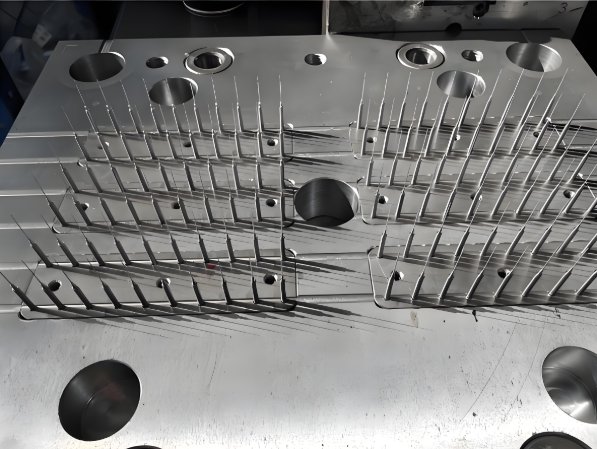
Modern healthcare depends on reliable medical devices. Medical injection molding plays a key role in producing high-quality parts. A skilled mold maker ensures accuracy, sterility, and durability.
1. What is Medical Injection Molding?
The Basics
Medical injection molding is a manufacturing process. It produces plastic medical parts with precision. A mold maker creates the molds used in production.
Why It Matters
- Ensures consistent quality
- Meets strict medical standards
- Reduces human error in manufacturing
2. The Importance of Medical Injection Molding
High Precision
Medical devices require extreme accuracy. Medical injection molding produces parts with tight tolerances. A mold maker ensures exact dimensions.
Sterility and Safety
Medical parts must be free from contamination. Medical injection molding takes place in clean environments. A mold maker ensures materials meet medical standards.
Cost-Effective Mass Production
Healthcare needs large volumes of medical parts. Medical injection molding allows fast and cost-effective production. A mold maker optimizes efficiency.
Lightweight and Durable Materials
Plastics are lighter than metal. Medical injection molding produces strong yet lightweight parts. A mold maker selects durable materials.
Custom Designs for Specific Needs
Each medical device has unique requirements. Medical injection molding allows custom shapes and sizes. A mold maker tailors molds for specific applications.
3. Common Applications of Medical Injection Molding
Surgical Instruments
Surgical tools require precision and sterility. Medical injection molding produces reliable instruments. A mold maker ensures accurate molding.
Examples:
- Forceps
- Clamps
- Scalpel handles
Implantable Medical Devices
Implants must be biocompatible. Medical injection molding creates safe and durable implants. A mold maker selects medical-grade plastics.
Examples:
- Pacemaker housings
- Artificial joints
- Dental implants
Drug Delivery Systems
Accurate drug delivery saves lives. Medical injection molding ensures precise dosing mechanisms. A mold maker creates high-precision molds.
Examples:
- Insulin pens
- Inhalers
- Syringe plungers
Diagnostic and Laboratory Equipment
Testing requires accurate tools. Medical injection molding produces high-quality diagnostic parts. A mold maker ensures consistency.
Examples:
- Test tubes
- Lab trays
- Sample containers
Prosthetics and Orthopedic Devices
Prosthetics must be strong and comfortable. Medical injection molding creates lightweight and durable prosthetics. A mold maker ensures proper fit.
Examples:
- Artificial limbs
- Braces
- Joint supports
4. Key Materials Used in Medical Injection Molding
Medical-Grade Plastics
A mold maker selects materials based on safety and performance.
- Polycarbonate (PC) – Strong and transparent
- PEEK (Polyetheretherketone) – Heat-resistant and biocompatible
- Polypropylene (PP) – Flexible and chemical-resistant
- Silicone – Soft and biocompatible
Why Material Choice is Important
- Ensures patient safety
- Meets regulatory standards
- Increases product durability
5. Cleanroom Manufacturing for Medical Molding
What is a Cleanroom?
A cleanroom is a controlled environment. Medical injection molding requires strict cleanliness. A mold maker follows precise production protocols.
Benefits of Cleanroom Molding
- Prevents contamination
- Meets FDA and ISO standards
- Ensures high-quality products
6. Micro-Molding for Tiny Medical Components
What is Micro-Molding?
Micro-molding produces extremely small parts. Medical injection molding ensures high accuracy. A mold maker creates precision micro-molds.
Applications of Micro-Molding
- Miniature surgical tools
- Catheter tips
- Hearing aid components
7. Single-Use vs. Reusable Medical Components
Why Single-Use Medical Parts?
Hospitals need disposable, sterile tools. Medical injection molding produces them in large volumes. A mold maker ensures precision.
Reusable Medical Components
Some medical tools require sterilization and reuse. Medical injection molding ensures durability. A mold maker selects high-quality materials.
Examples:
- Surgical handles
- Blood pressure cuffs
- Monitoring device casings
8. Multi-Shot Molding for Complex Medical Parts
What is Multi-Shot Molding?
This process combines different materials into one part. Medical injection molding uses this technique for better functionality. A mold maker ensures proper bonding.
Applications
- Dual-layer syringe plungers
- Soft-touch medical grips
- Ergonomic device handles
9. Regulatory Compliance in Medical Injection Molding
Why Compliance Matters
Medical products must meet strict safety standards. Medical injection molding follows global regulations. A mold maker ensures compliance.
Key Standards
- FDA (U.S. Food and Drug Administration)
- ISO 13485 (Medical Device Quality)
- USP Class VI (Biocompatibility)
10. Rapid Prototyping for Faster Product Development
Why Prototyping is Essential
New medical devices require extensive testing. Medical injection molding enables rapid prototyping. A mold maker refines designs before full production.
Prototyping Techniques
- 3D printing
- Soft tooling
- Small-batch molding
11. The Role of Automation in Medical Injection Molding
How Automation Improves Manufacturing
Modern production uses automation. Medical injection molding benefits from robotic systems. A mold maker programs precise machine operations.
Advantages of Automation
- Reduces human error
- Increases production speed
- Ensures consistent quality
12. Sustainable Medical Injection Molding
Why Sustainability Matters
Hospitals generate plastic waste. Medical injection molding now includes eco-friendly solutions. A mold maker selects sustainable materials.
Green Medical Plastics
- Biodegradable polymers
- Recycled medical-grade plastics
- Plant-based resins
13. Advanced Cooling Systems for Faster Production
Why Cooling is Important
Faster cooling increases efficiency. Medical injection molding uses advanced cooling techniques. A mold maker ensures even heat distribution.
Cooling Methods
- Conformal cooling channels
- Water-assisted cooling
- Copper inserts for faster heat dissipation
14. The Future of Medical Injection Molding
What’s Next?
Technology is evolving. Medical injection molding will use AI and smart materials. A mold maker will integrate automated quality control.
Upcoming Trends
- AI-driven defect detection
- Fully automated molding lines
- Smart medical materials with enhanced properties
Medical injection molding is essential for modern healthcare. It provides precision, sterility, and efficiency. Skilled mold makers ensure the highest standards, improving patient care and medical innovation.