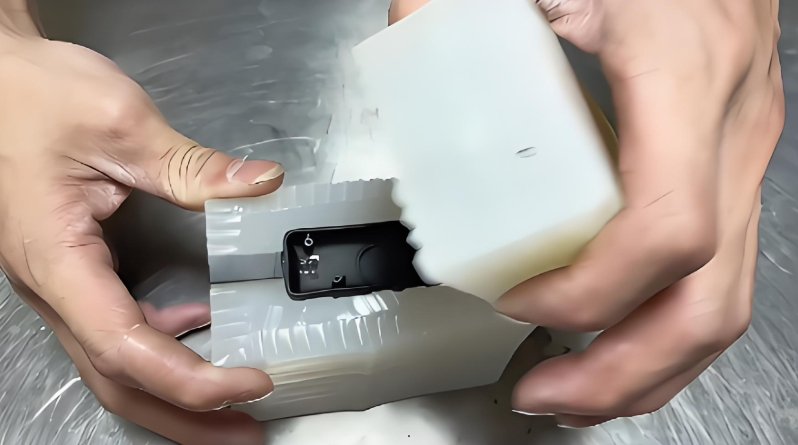
Innovation requires multiple attempts. Each version refines ideas further. This process is called iterative design.
Rapid Prototyping plays a central role in this. It allows quick creation of physical models. Partnering with an injection mould company enhances the process.
This guide explores how Rapid Prototyping supports iterative design.
What Is Iterative Design?
Iterative design means repeated cycles of design, testing, and improvement.
It helps teams find flaws early. Feedback after each cycle improves the next version.
This approach saves time and ensures better results.
Why Use Rapid Prototyping?
Rapid Prototyping accelerates iterative design. It turns concepts into physical models fast.
Teams can test ideas without waiting. Early errors get fixed quickly.
An injection mould company ensures the prototypes are precise.
Benefits of Rapid Prototyping in Iterative Design
Faster Testing
Prototypes are ready quickly. This shortens testing cycles.
Improved Feedback
Physical models make feedback more accurate. People understand designs better when they see them.
Cost Savings
Early detection of errors prevents expensive mistakes.
Better Collaboration
Teams share ideas easily using tangible models.
Steps in Rapid Prototyping for Iterative Design
1. Idea Generation
Start with a concept. Sketch or model it digitally.
2. Prototype Creation
Use Rapid Prototyping to build a model.
3. Testing
Test the prototype in real conditions. Collect feedback.
4. Refinement
Improve the design based on the feedback.
5. Repeat
Create the next version and test again.
Role of an Injection Mould Company
Material Expertise
They suggest suitable materials for each cycle.
Precision Manufacturing
Their tools ensure accurate prototypes.
Scalability
They handle small and large production runs.
Cost Efficiency
They optimize resources, saving money.
Examples of Rapid Prototyping in Iterative Design
Consumer Products
Companies refine gadgets through multiple versions.
Automotive
Car parts undergo iterative design for performance and safety.
Medical Devices
Prototypes ensure safety and compliance with regulations.
Challenges in Iterative Design
Tight Deadlines
Fast iterations can cause stress.
High Costs
Frequent prototyping increases expenses.
Complexity
Managing multiple versions requires good organization.
Overcoming Challenges with Rapid Prototyping
Efficient Processes
An injection mould company streamlines production.
Cost Control
They provide affordable materials and methods.
Advanced Technology
Modern machines make iterations faster and more accurate.
Materials in Rapid Prototyping
Plastics
Affordable and versatile. Ideal for early versions.
Metals
Strong and durable. Used for functional prototypes.
Composites
Combine properties of different materials.
Specialized Materials
Required for medical or aerospace applications.
Comparing Prototyping Methods
3D Printing
- Fast and affordable for initial designs.
- Limited material options.
CNC Machining
- High precision but slower.
- Best for functional testing.
Injection Molding
- Suitable for larger runs.
- Partner with an injection mould company for better results.
Future Trends in Rapid Prototyping
Smarter Machines
AI will speed up design and manufacturing.
Sustainable Materials
Eco-friendly options will reduce waste.
Greater Collaboration
Digital tools will make teamwork seamless.
Rapid Prototyping is essential for iterative design. It allows teams to test and refine ideas quickly.
Working with an injection mould company improves efficiency. They ensure precision, scalability, and cost savings.
By embracing this approach, you can create better products faster.