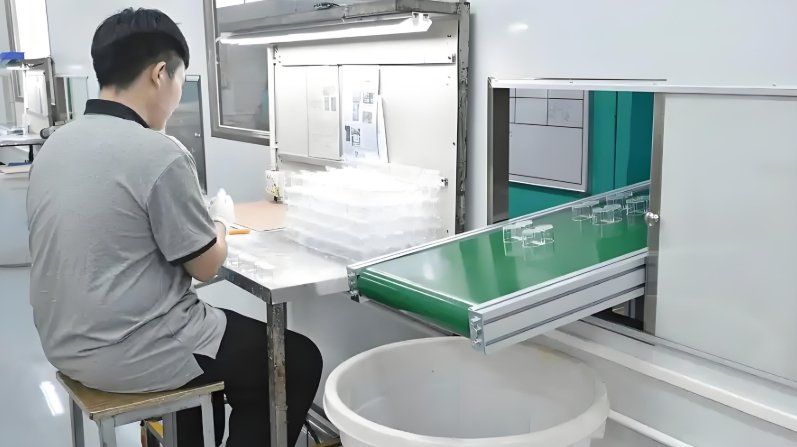
Quality control is vital in injection molding. It ensures that every product meets high standards. An injection mould company focuses on delivering precise, reliable, and durable products. This requires a combination of advanced technology, skilled mold makers, and strict testing processes. Quality is key to satisfying customers and building trust.
In this guide, we explore how an injection mould company ensures quality. From material selection to final inspection, every step matters. Let’s examine these processes.
The Role of Materials in Quality
Material selection is the foundation of quality in injection molding. Using the wrong material can lead to defects. High-quality raw materials ensure durable and reliable products. An injection mould company evaluates materials carefully.
Thermoplastics like ABS, polycarbonate, and nylon are popular choices. These materials have excellent strength and flexibility. For sensitive applications, biocompatible or food-grade plastics may be required.
The mold maker ensures that the chosen material works with the mold design. This avoids problems like warping, cracks, or uneven surfaces. Material consistency is checked regularly during production.
Precision in Mold Design
Mold design is another critical factor. An experienced mold maker creates molds that meet exact specifications. Precise molds reduce errors and waste.
Designing molds involves computer-aided design (CAD) software. This technology allows for accurate measurements and 3D visualization. Before production begins, the design is thoroughly tested.
The mold must also allow for proper cooling and ejection. Poor cooling can cause defects in the final product. The injection mould company ensures that molds are optimized for efficiency and quality.
Advanced Machinery for Quality
Modern machinery plays a significant role in quality control. An injection mould company uses high-tech equipment to maintain precision. Machines with accurate temperature and pressure controls ensure consistent results.
Automation is widely used in injection molding. Robots handle repetitive tasks with accuracy. This reduces human error and speeds up production. Automated systems also monitor processes in real-time. Any deviation from the standard is quickly corrected.
Skilled technicians oversee the machinery. They ensure that every product meets the required standards. Regular maintenance keeps machines running smoothly.
Inspection During Production
Inspection is continuous during injection molding. Quality checks happen at multiple stages. This ensures defects are caught early. An injection mould company uses various inspection methods.
One method is visual inspection. Workers examine products for surface defects like scratches or bubbles. For more precision, companies use advanced tools.
Dimensional inspection is another important step. This measures the product’s size and shape. It ensures the product matches the mold design. Digital calipers, micrometers, and coordinate measuring machines (CMM) are used for this purpose.
Material properties are also tested. Tensile strength, hardness, and flexibility are evaluated. These tests confirm that the product can withstand its intended use.
The Role of Mold Makers
The mold maker plays a crucial role in quality control. They ensure that the molds meet strict standards. A poorly made mold can ruin an entire production run. Skilled mold makers focus on precision and durability.
Molds undergo rigorous testing before use. Trial runs ensure the mold produces flawless parts. Any flaws are corrected immediately. The mold maker also considers factors like cooling time and material flow.
High-quality molds are essential for consistent results. They also reduce downtime and maintenance costs. The injection mould company invests in training and tools for its mold makers.
Final Inspection and Packaging
Once production is complete, products go through final inspection. This is the last chance to catch defects before shipping. An injection mould company uses strict criteria for approval.
Surface finish, dimensions, and material properties are rechecked. Products that fail to meet standards are rejected. Approved products are cleaned and prepared for packaging.
Eco-friendly packaging is often used. This reduces environmental impact. The products are securely packed to prevent damage during transportation.
Continuous Improvement
Quality control is an ongoing process. An injection mould company constantly seeks to improve. Feedback from customers helps identify areas for improvement.
The company invests in new technology and training. Regular audits ensure that processes meet industry standards. Certifications like ISO 9001 demonstrate a commitment to quality.
Benefits of Quality Control
Quality control offers many benefits. First, it ensures customer satisfaction. High-quality products meet or exceed expectations.
Second, it reduces waste. Defective products are costly and harmful to the environment. By catching defects early, an injection mould company saves time and resources.
Third, quality control builds trust. Customers rely on the company for consistent results. This strengthens business relationships and reputation.
Finally, it ensures compliance with regulations. Many industries have strict quality requirements. Meeting these standards avoids legal issues and penalties.
Challenges in Quality Control
Despite its importance, quality control is challenging. Variations in raw materials can affect product quality. An injection mould company must work closely with suppliers.
Machine malfunctions are another challenge. Regular maintenance and skilled technicians help minimize downtime.
Keeping up with customer demands is also difficult. Customers expect faster delivery without compromising quality. Balancing speed and accuracy requires careful planning.
Quality control is the backbone of injection molding. It ensures that products meet high standards and customer expectations. An injection mould company achieves this through careful material selection, precise mold design, and advanced machinery. The mold maker plays a vital role in ensuring that every product is flawless.
Continuous inspection and improvement further enhance quality. By investing in quality control, the company builds trust and reduces waste. This benefits both the business and its customers.