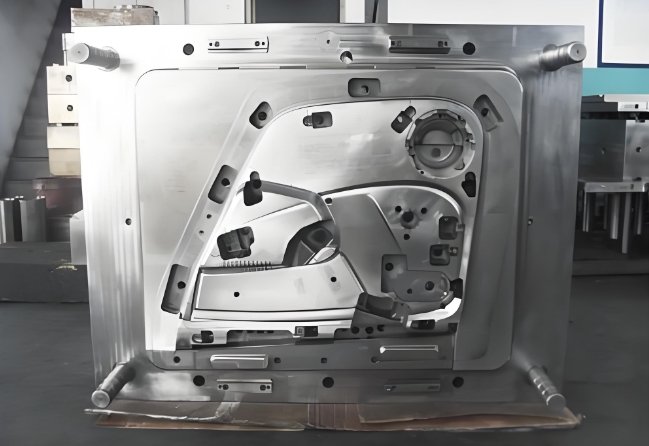
Vehicle exteriors define a car’s look and feel. Automotive injection molds help create smooth, stylish, and aerodynamic designs. A skilled mold maker ensures precision and durability in every part. These molds shape bumpers, grilles, panels, and other exterior components. With injection molding, manufacturers achieve high-quality finishes and lightweight structures.
Why Injection Molding for Automotive Exteriors?
1. High Precision Manufacturing
Every exterior component must fit perfectly. Automotive injection molds create detailed, accurate parts. A skilled mold maker ensures smooth finishes and perfect dimensions. This process reduces errors and enhances the vehicle’s appearance.
2. Strong and Lightweight Parts
Modern vehicles need strong yet lightweight materials. Injection molding allows the use of advanced plastics and composites. These materials reduce weight without compromising durability. A well-designed mold maker ensures parts meet strength requirements.
3. Consistent Quality and Efficiency
Mass production demands consistency. Automotive injection molds produce identical parts with minimal variation. This guarantees high quality across all vehicles. A reliable mold maker ensures efficiency and reduces production costs.
Key Exterior Components Made with Injection Molding
1. Bumpers
Bumpers protect the car and enhance aerodynamics. They must absorb impact while maintaining shape. Automotive injection molds create seamless, durable bumpers. A professional mold maker ensures perfect fitting and a smooth finish.
2. Grilles
Grilles improve airflow and add style. Injection molding ensures intricate designs with high accuracy. A mold maker crafts grilles that match the car’s overall look.
3. Side Panels
Side panels must be lightweight, strong, and aesthetically pleasing. Automotive injection molds create panels with high precision. A skilled mold maker ensures they align perfectly with the vehicle’s frame.
4. Door Handles
Door handles must be ergonomic, strong, and visually appealing. Injection molding ensures smooth and durable handles. A mold maker designs them for perfect grip and fit.
5. Mirror Housings
Mirror housings protect side mirrors from damage. Automotive injection molds create lightweight and durable housings. A mold maker ensures smooth edges and precise fitting.
6. Spoilers and Air Ducts
Spoilers improve aerodynamics and add style. Air ducts enhance airflow and cooling. Injection molding allows complex shapes with a smooth finish. A skilled mold maker ensures accurate and efficient production.
7. Roof Racks and Trim Pieces
Roof racks provide extra storage. Trim pieces add finishing touches to the exterior. Automotive injection molds produce sleek, well-fitted parts. A mold maker ensures strength and consistency.
Material Selection for Automotive Exteriors
1. High-Impact Plastics
Bumpers and panels require impact-resistant materials. Polypropylene and ABS plastics are common choices. These materials balance strength and flexibility.
2. Lightweight Composites
Carbon fiber-reinforced plastics (CFRP) offer strength with reduced weight. Automotive injection molds shape these composites into durable exterior parts.
3. UV-Resistant Materials
Exteriors face sunlight and harsh weather. UV-resistant plastics prevent fading and cracking. A mold maker selects materials that maintain long-term durability.
Advantages of Using Injection Molding for Auto Exteriors
1. Cost-Effective Production
Injection molding reduces material waste. Once the mold is set, large quantities can be produced efficiently. A skilled mold maker minimizes production costs while maintaining high quality.
2. Complex and Custom Designs
Modern cars require intricate designs. Injection molding allows complex shapes and custom textures. A mold maker ensures every detail is perfect.
3. Faster Production Times
Automotive manufacturers need speed. Automotive injection molds allow rapid production. A mold maker optimizes the process for efficiency.
4. Durability and Longevity
Molded exterior parts withstand extreme temperatures, moisture, and impacts. A reliable mold maker ensures parts meet high durability standards.
Challenges in Injection Molding for Automotive Exteriors
1. Maintaining Surface Quality
Scratches or imperfections affect the final look. A skilled mold maker ensures smooth, defect-free molds. This results in high-quality surfaces.
2. Material Shrinkage
Some plastics shrink after cooling. Automotive injection molds must compensate for this. A mold maker adjusts designs to maintain accuracy.
3. Design Complexity
Modern exteriors have intricate details. Injection molding must capture every feature precisely. A mold maker uses advanced techniques to achieve this.
Future Trends in Injection Molding for Auto Exteriors
1. Sustainable Materials
Recyclable and biodegradable plastics are gaining popularity. Mold makers are adapting to these eco-friendly materials.
2. Advanced Coatings
New coatings improve durability and aesthetics. Scratch-resistant and self-healing surfaces are becoming common. Automotive injection molds must accommodate these innovations.
3. Smart Exteriors
Future vehicles may have embedded sensors and lighting in exterior parts. Mold makers are working on solutions to integrate smart technology.
Automotive injection molds play a crucial role in shaping modern vehicle exteriors. Every bumper, grille, and panel depends on precise molds. A skilled mold maker ensures perfect fit, durability, and sleek design. With advancements in materials and techniques, injection molding continues to revolutionize the automotive industry. As vehicles evolve, mold makers will drive innovation in exterior design and production.