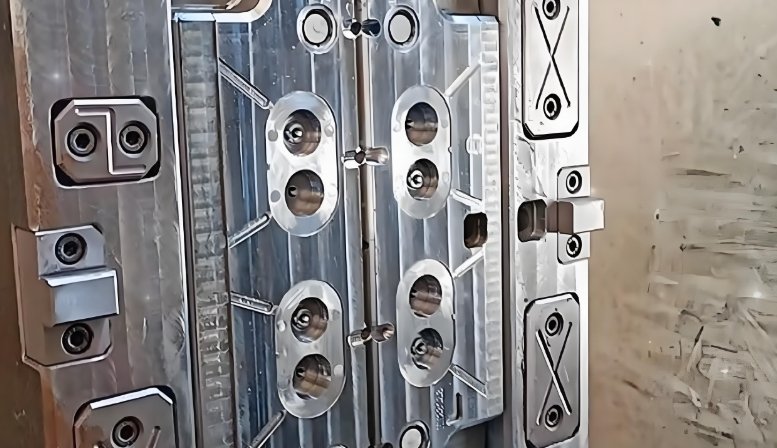
Medical devices require strong and safe materials. Medical injection molding relies on high-quality plastics. A skilled mold maker selects the right material. The right plastic ensures durability, sterility, and biocompatibility.
1. Why Material Selection Matters in Medical Injection Molding
Ensuring Biocompatibility
Medical devices touch the human body. Poor materials can cause infections or reactions. Biocompatible plastics prevent harm.
Maintaining Strength and Durability
Medical devices face pressure and impact. Weak materials break easily. The right plastic ensures long-lasting performance.
Sterilization Compatibility
Hospitals sterilize medical devices. Heat, chemicals, and radiation are used. Plastics must resist these treatments.
Regulatory Compliance
Medical plastics must meet FDA and ISO standards. A mold maker selects materials that pass strict tests.
2. Common Plastics Used in Medical Injection Molding
1. Polycarbonate (PC)
- Strong and impact-resistant.
- Used in surgical instruments and IV connectors.
- Transparent for easy monitoring.
2. Polypropylene (PP)
- Lightweight and chemical-resistant.
- Common in syringes and lab containers.
- Withstands heat sterilization.
3. Polyethylene (PE)
- Flexible and durable.
- Used in tubing and prosthetics.
- Resistant to moisture and bacteria.
4. Acrylonitrile Butadiene Styrene (ABS)
- Tough and lightweight.
- Ideal for medical device housings.
- Maintains shape under pressure.
5. Polyether Ether Ketone (PEEK)
- High heat and chemical resistance.
- Used in implants and surgical tools.
- Offers superior mechanical properties.
6. Polyvinyl Chloride (PVC)
- Flexible and cost-effective.
- Common in IV bags and tubing.
- Resists chemicals and sterilization.
7. Silicone
- Soft and biocompatible.
- Used in catheters and seals.
- Withstands extreme temperatures.
3. How a Mold Maker Ensures the Right Material Choice
Evaluating Application Needs
A mold maker considers the function of the part. Strength, flexibility, and sterilization methods are assessed.
Testing Material Properties
Materials undergo stress and durability tests. These tests confirm resistance to chemicals and impact.
Ensuring Regulatory Compliance
A skilled mold maker follows FDA and ISO guidelines. Compliance ensures safety and approval for medical use.
Optimizing for Cost and Efficiency
Some materials are expensive. A mold maker balances cost with performance. The best option meets safety standards at a reasonable price.
4. Key Considerations When Choosing Medical Plastics
1. Biocompatibility
The plastic should not harm patients. It must be tested for allergies and reactions.
2. Strength and Durability
Medical devices need to be strong. The material should resist breaking or bending.
3. Sterilization Resistance
Many medical tools are sterilized with heat, chemicals, or radiation. The plastic must withstand these processes.
4. Flexibility and Rigidity
Some parts require stiffness, while others need flexibility. A mold maker selects the right balance.
5. Cost Efficiency
High-quality plastics can be costly. The best material provides durability at a reasonable price.
5. Applications of Medical Plastics in Injection Molding
Surgical Instruments
Polycarbonate and PEEK create strong surgical tools. These materials improve precision and durability.
Implants and Prosthetics
PEEK and silicone are used in implants. They are safe for long-term use inside the body.
IV and Drug Delivery Systems
Polypropylene and PVC are common in IV bags and syringes. They prevent contamination and ensure safe drug delivery.
Diagnostic Equipment
ABS and polycarbonate are used in diagnostic devices. These materials provide durability and clarity.
Medical Packaging
Sterile plastic packaging protects medical tools. It prevents contamination and extends shelf life.
6. The Role of Medical Injection Molding in Material Selection
Step 1: Material Testing
Each plastic undergoes rigorous testing. This ensures it meets medical standards.
Step 2: Mold Design
A mold maker designs precise molds. This ensures consistent product quality.
Step 3: Injection Molding Process
The plastic is melted and injected into the mold. It cools and forms the final shape.
Step 4: Quality Control
Every part is checked for strength, accuracy, and biocompatibility. Only approved parts reach the market.
7. Challenges in Medical Injection Molding Material Selection
Regulatory Approval
Meeting medical standards takes time. Every plastic must pass strict safety tests.
Cost of High-Quality Materials
Some biocompatible plastics are expensive. A mold maker must balance performance with cost.
Manufacturing Precision
Medical parts require tight tolerances. Even small errors can affect performance.
8. Future Trends in Medical Injection Molding Materials
Biodegradable Medical Plastics
Sustainable materials reduce medical waste. They offer eco-friendly alternatives to traditional plastics.
Smart Polymers
New plastics react to temperature and pressure changes. They improve medical device performance.
3D Printing with Medical-Grade Plastics
Advanced 3D printing allows faster, customized medical parts. It reduces production time.
Material selection is critical in medical injection molding. A skilled mold maker ensures safety, strength, and biocompatibility. The right plastic makes medical devices durable, sterile, and cost-effective. As technology advances, new materials will enhance medical innovation.