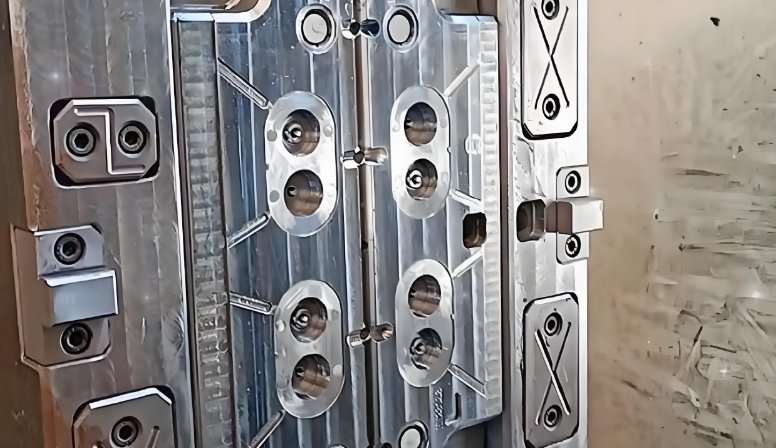
The Internet of Things (IoT) is revolutionizing medical injection molding. Smart sensors, automation, and real-time data improve precision and efficiency. Mold makers are using IoT to enhance monitoring, predictive maintenance, and compliance. This technology ensures better medical device manufacturing with minimal errors.
What is IoT in Medical Injection Molding?
1. Definition
IoT connects machines, sensors, and software to monitor and control production processes remotely.
2. Why It’s Important
- Reduces defects and waste.
- Improves efficiency and machine uptime.
- Ensures compliance with FDA and ISO standards.
- Provides real-time tracking of every molded component.
Key IoT Applications in Medical Injection Molding
1. Smart Sensors for Real-Time Monitoring
- Tracks temperature, pressure, and cycle times.
- Alerts operators to potential process deviations.
- Ensures consistent product quality.
2. AI-Driven Predictive Maintenance
- Detects early signs of mold wear and machine failures.
- Reduces unplanned downtime.
- Extends the lifespan of molds and equipment.
3. Cloud-Based Data Analytics
- Stores production data for instant access.
- Helps manufacturers analyze trends and optimize performance.
- Enables remote monitoring of multiple production sites.
4. Automated Quality Control
- Uses AI-powered vision systems to detect defects.
- Reduces manual inspections.
- Ensures compliance with medical manufacturing regulations.
5. Smart Inventory and Material Tracking
- IoT-connected RFID tags monitor raw materials.
- Prevents shortages and overstocking.
- Improves supply chain efficiency.
How IoT Improves Efficiency in Medical Injection Molding
1. Faster Production Cycles
- AI adjusts molding parameters in real time.
- Reduces cycle times without affecting quality.
2. Enhanced Mold Performance
- Sensors detect fluctuations in mold conditions.
- Prevents defects by optimizing cooling and material flow.
3. Better Energy Management
- IoT-powered machines adjust power usage.
- Reduces energy consumption and operational costs.
4. Remote Process Control
- Operators can monitor and adjust machines from anywhere.
- Increases flexibility and reduces response time to issues.
5. Improved Compliance and Traceability
- IoT logs every production detail.
- Ensures full traceability for audits and recalls.
The Role of Mold Makers in IoT Adoption
1. Designing Smart Molds
- Mold makers integrate sensors into mold designs.
- Enables real-time data collection for optimization.
2. Implementing IoT-Compatible Materials
- Works with manufacturers to select smart materials.
- Ensures compatibility with automated monitoring systems.
3. Enhancing Mold Maintenance Strategies
- Uses IoT data to predict and schedule maintenance.
- Reduces costly mold replacements.
4. Supporting Digital Twin Technology
- Mold makers create virtual models for testing before production.
- Improves accuracy and reduces material waste.
Challenges of IoT Integration in Medical Injection Molding
1. High Implementation Costs
- IoT-enabled machines and software require investment.
- Long-term efficiency gains offset initial costs.
2. Cybersecurity Risks
- IoT systems store sensitive production data.
- Strong cybersecurity measures are needed to prevent breaches.
3. Integration with Legacy Systems
- Older machines may not support IoT connectivity.
- Upgrading production lines takes time and resources.
4. Data Overload and Management
- IoT generates large amounts of data.
- Manufacturers need AI-powered analytics to interpret and use data effectively.
Latest Innovations in IoT for Medical Injection Molding
1. AI-Powered Process Optimization
- Machine learning fine-tunes molding parameters.
- Improves precision and reduces material waste.
2. Blockchain for Secure Production Data
- Ensures tamper-proof tracking of medical device manufacturing.
- Improves transparency and regulatory compliance.
3. Smart Robotic Automation
- IoT-connected robots handle molding, inspection, and packaging.
- Reduces labor costs and enhances efficiency.
4. Digital Twin Integration
- Creates virtual simulations of molding processes.
- Identifies and corrects defects before production starts.
5. Edge Computing for Faster Decision-Making
- Processes IoT data locally instead of relying on cloud servers.
- Reduces lag time and improves real-time monitoring.
Future Trends in IoT for Medical Injection Molding
1. Fully Automated Smart Factories
- AI-powered IoT will manage the entire production process.
- Requires minimal human intervention.
2. 5G-Enabled IoT Networks
- Ultra-fast data transmission will enhance real-time monitoring.
- Improves machine-to-machine communication.
3. Sustainable IoT Solutions
- Smart energy management will lower carbon footprints.
- IoT will optimize resource usage for greener manufacturing.
4. Patient-Specific Medical Device Production
- IoT will enable customized manufacturing based on patient data.
- Smart molds will adjust in real-time for personalized implants.
5. AI-Driven Supply Chain Optimization
- IoT will improve material sourcing and logistics.
- Reduces delays and ensures consistent production.
IoT is transforming medical injection molding. Smart sensors, AI, and automation improve efficiency, reduce defects, and ensure compliance. Mold makers are integrating IoT into smart molds, predictive maintenance, and digital twin technology. As IoT advances, the future of medical molding will become faster, smarter, and more reliable.