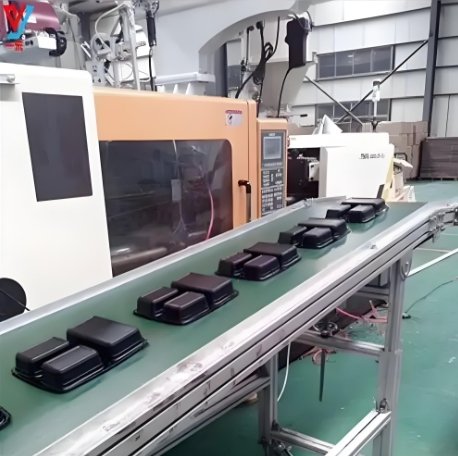
High-end electronics demand more than basic quality. They require precision, beauty, and reliability. Devices like smartphones, medical equipment, and luxury audio systems all use components built to the highest standards. In this world, traditional methods are not enough. That’s why specialty Electronic Injection Molding techniques have become so important.
Today, skilled Mold Makers use advanced methods to create parts that meet the growing demands of the electronics industry. These techniques allow for better finishes, tighter tolerances, stronger materials, and smarter production processes. In this article, we’ll dive deep into how specialty molding is changing high-end electronics and why choosing the right Mold Maker matters so much.
What is Specialty Electronic Injection Molding?
Specialty Electronic Injection Molding refers to using advanced molding methods to produce parts with very specific or high-end needs. These techniques go beyond simple plastic shaping. They often involve:
- High-precision molds
- Unique material blends
- Overmolding and insert molding
- Micro-molding
- Gas-assisted molding
- Liquid silicone rubber molding
- Metal-to-plastic transitions
A top Mold Maker knows which technique to choose based on the product’s needs. Using these methods ensures that even the most complex electronics parts are perfect right from the first production run.
Why High-End Electronics Need Specialty Molding
Luxury electronics set the standard for quality. Every small detail matters—from the way a device feels in your hand to how it performs after years of use. Ordinary manufacturing often cannot meet these high expectations.
Electronic Injection Molding with specialty methods provides:
- Ultra-fine surface finishes without secondary work
- Exact fits between parts, avoiding gaps or stress points
- Enhanced durability with tougher materials
- Weight savings with smarter designs
- Smaller sizes without losing strength
A good Mold Maker understands how to achieve all these goals, ensuring that premium devices live up to customer expectations.
Key Specialty Molding Techniques
Several advanced techniques help high-end electronics manufacturers succeed. Let’s look at the most important ones:
1. Overmolding
Overmolding means molding plastic over another material or part. For electronics, this can protect circuit boards, cover delicate parts, or create soft-touch surfaces. Mold Makers must be very precise because two different materials must bond perfectly without damaging sensitive electronics.
2. Insert Molding
Insert molding places metal pieces—like screws, contacts, or shielding—inside the mold before injecting plastic around them. This creates strong, integrated parts without extra assembly steps. Insert molding is common in connectors, buttons, and casings where metal adds strength or conductivity.
3. Micro-Molding
Some electronic parts are extremely small. Micro-molding focuses on making tiny, highly detailed parts for devices like hearing aids, medical sensors, and miniaturized cameras. Here, Electronic Injection Molding requires extreme care. A Mold Maker uses specialized machines and tools to control tiny amounts of material with great accuracy.
4. Gas-Assisted Molding
Gas-assisted molding injects gas into the molten plastic during molding. This creates hollow sections inside parts, saving weight and material. It also prevents sink marks and warping. Many high-end electronics use this method to build stronger yet lighter frames and housings.
5. Liquid Silicone Rubber (LSR) Molding
In some cases, soft, flexible parts are needed, like seals, keypads, or gaskets. LSR molding creates these parts with amazing precision. LSR parts resist heat, chemicals, and aging, making them perfect for rugged electronics.
The Role of the Mold Maker in Specialty Molding
Choosing the right Mold Maker is the most important step in specialty Electronic Injection Molding. Here’s why:
- Tool Design Expertise: Specialty parts need smart mold designs to avoid defects. A skilled Mold Maker predicts problems before they happen.
- Material Knowledge: Not all plastics behave the same. The Mold Maker knows how to handle advanced blends and additives.
- Precision Machining: Specialty molds must be built to very fine tolerances—often within microns.
- Quality Control: High-end electronics cannot afford defects. A great Mold Maker sets up strict checking systems.
By working closely with product designers and engineers, the Mold Maker helps turn creative ideas into real-world, manufacturable parts.
Specialty Materials in High-End Electronic Molding
Using the right material is just as important as using the right molding method. Specialty Electronic Injection Molding often uses:
- Carbon-filled plastics for conductivity
- Glass-filled nylons for strength
- Flame-retardant materials for safety
- ESD-safe plastics for static protection
- Optical-grade plastics for lenses and covers
Each application needs a unique balance of weight, strength, cost, and appearance. A good Mold Maker helps customers choose wisely.
Applications of Specialty Molding in Electronics
Specialty Electronic Injection Molding is already being used across many products, such as:
- High-end smartphones and tablets
- Medical devices like monitors and pumps
- Aerospace controls and sensors
- Automotive electronics like cameras and radars
- Home automation systems
- Luxury audio and video equipment
In all these products, specialty techniques improve both the look and the function, creating better user experiences.
Future Trends in Specialty Electronic Injection Molding
As electronics keep evolving, specialty Electronic Injection Molding will keep advancing too. We can expect:
- Smarter molds that monitor themselves during production
- More eco-friendly materials with recycled content
- Hybrid materials combining plastics, metals, and composites
- Even smaller parts for wearable and implantable devices
- Faster prototyping with digital twins and simulation
The future will demand even more from Mold Makers. Those who invest in new skills and technologies will lead the next wave of innovation.
High-end electronics require more than simple manufacturing. They need specialty Electronic Injection Molding handled by a skilled Mold Maker. Advanced techniques like overmolding, insert molding, micro-molding, and gas-assisted molding are essential to meet today’s exacting standards.
By combining smart design, expert tooling, and the right materials, Mold Makers help electronics companies deliver beautiful, reliable, and cutting-edge products. As devices continue to get smarter, smaller, and more complex, specialty molding will become even more important.
If you are developing a next-generation electronic product, choosing the right Mold Maker and specialty molding method could be the difference between success and failure. In the world of high-end electronics, every detail matters—and Electronic Injection Molding is where great products begin.