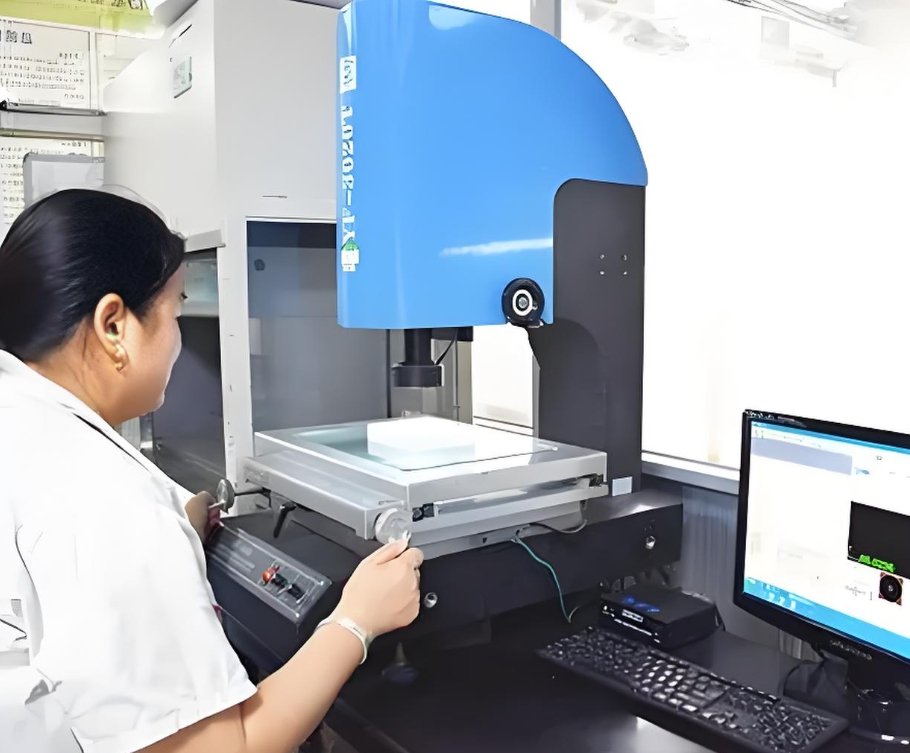
Controlling quality in an injection molding department is crucial. It helps keep production efficient and reduces waste. A Mold Maker plays a big role in ensuring this. Below are some ways to control quality effectively.
Start with High-Quality Materials
Quality begins with the materials used. The injection molding process requires specific types of plastic. These materials must meet the required standards. If the materials are of poor quality, the final product will be flawed. Always source materials from trusted suppliers. A Mold Maker knows how to select the right type of material.
Create a Solid Design
A strong design is the backbone of good production. Design errors lead to bad products. This is where the Mold Maker comes in. They help refine the design for the best results. Using computer-aided design (CAD) software is helpful. These tools catch potential issues early. Design reviews should be thorough.
Ensure Mold Quality
The mold itself plays a major role in the quality of the final product. A poorly made mold will produce bad parts. Molds should be designed and maintained by a skilled Mold Maker. Regular inspections of the mold are necessary. This helps identify wear and tear. Fixing small issues early prevents bigger problems later. Clean the molds regularly. Dirt or leftover materials can affect the quality of the parts.
Monitor the Injection Molding Process
Monitoring the injection molding process is vital. Even small changes in temperature or pressure can affect the outcome. Ensure machines are calibrated correctly. A skilled Mold Maker should oversee this. Machines should run at the correct settings for each material. Record these settings for future use. Automatic monitoring systems can help detect issues early.
Train Employees
The people running the machines play a huge role in quality control. Employees need proper training. They should understand the injection molding process well. Training should focus on machine settings, troubleshooting, and safety. The Mold Maker should guide less experienced staff. Regular training sessions keep everyone up-to-date.
Conduct Regular Inspections
Frequent inspections ensure quality is maintained. Inspect both the mold and the final product. Look for common issues like bubbles, cracks, or poor surface finish. Use precise measuring tools to check dimensions. A skilled Mold Maker knows how to spot these problems early. Inspections should happen at every step of the process.
Implement a Quality Management System (QMS)
A QMS helps organize quality control efforts. It provides a structured way to check for errors. The Mold Maker should follow the guidelines in the system. This system also includes record-keeping. Every part of the process should be documented. This helps trace any issues back to their source. Many companies use ISO 9001 for quality management. This certification ensures global standards are met.
Conduct Final Product Testing
Once the part is produced, it needs testing. This step ensures the part meets all requirements. The Mold Maker should be part of this process. Tests may include stress tests, temperature checks, and visual inspections. Different parts may require different tests. Testing catches any remaining flaws before the product ships to customers.
Use Advanced Technology
New technology can help control quality. Automation can reduce human error. Sensors and monitoring systems can track each stage of production. These systems alert the team if something goes wrong. Robotics can also help with precision tasks. The Mold Maker should embrace these technologies. They improve efficiency and quality.
Collaborate with Suppliers
Collaboration with suppliers ensures consistent material quality. A good relationship with material suppliers helps you get the best quality. Share your requirements with suppliers. They should know the exact materials needed for your injection molding process. A Mold Maker can also provide feedback on material quality.
Maintain Equipment
Proper machine maintenance is crucial. Machines need regular servicing to run smoothly. If a machine fails, it can ruin a production run. The Mold Maker should ensure all equipment is in top shape. A maintenance schedule should be followed strictly. Preventative maintenance is better than fixing a broken machine. Replace parts that show signs of wear.
Get Customer Feedback
Customer feedback is valuable. It helps identify any quality issues that might have been missed. Regularly ask for feedback after delivering products. A Mold Maker can use this information to make improvements. Customers appreciate companies that listen to their concerns.
Keep Improving
Quality control is an ongoing process. There’s always room for improvement. Regular audits of the quality control process should be done. The Mold Maker and team should be open to new ideas. Benchmarking against industry standards helps identify gaps. Continuous improvement ensures the department stays competitive.
Safety First
Safety should never be overlooked. Unsafe practices can harm employees and damage machines. Training on safety measures should be regular. A safe environment leads to fewer accidents. Fewer accidents mean less downtime and fewer quality issues. The Mold Maker plays a role in ensuring safety protocols are followed.
Communicate Clearly
Clear communication between team members is key. Issues must be reported quickly. The Mold Maker should ensure everyone is on the same page. A strong communication system reduces the chance of errors. Regular meetings and updates help keep the team informed.
Quality control in injection molding is critical for success. It starts with good materials, skilled employees, and well-maintained equipment. A Mold Maker is central to this process. By following strict quality standards, the department can produce high-quality parts consistently.