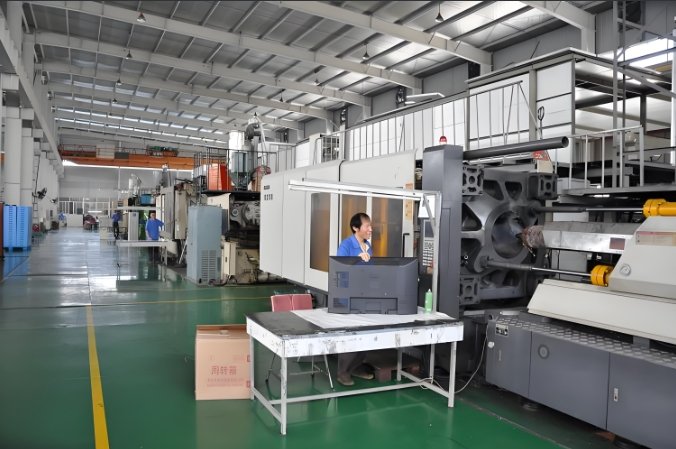
In Electronic Injection Molding, dimensional stability is key. Electronic parts must fit precisely. Even small changes in size can cause failures. Dimensional stability ensures that the parts stay within the correct size range. It is crucial for the function and durability of the electronic device. A skilled Mold Maker can help maintain this stability.
1. What Is Dimensional Stability?
Dimensional stability means that the part will not shrink, expand, or warp after molding. For Electronic Injection Molding, this is especially important. Small changes in part size can affect the performance of electronic devices. Precision is essential.
2. Factors That Affect Dimensional Stability
Several factors affect dimensional stability. They include:
- Mold design
- Material choice
- Injection pressure
- Cooling time
- Mold temperature
Each of these must be controlled. The Mold Maker plays a vital role in ensuring all factors are balanced correctly.
3. Proper Mold Design
Mold design is the first step in ensuring dimensional stability. A well-designed mold will ensure the plastic flows evenly. It will also prevent uneven cooling.
The Mold Maker ensures that the mold is designed with proper venting, gating, and flow paths. This reduces the chance of defects.
4. Material Selection for Dimensional Stability
The material chosen for Electronic Injection Molding affects dimensional stability. Different plastics shrink at different rates. For example, thermoplastics shrink more than thermosets.
A Mold Maker chooses the right material for the job. They understand the material’s shrinkage rate. This helps prevent changes in size and shape.
5. Controlling Injection Pressure
Injection pressure controls how plastic enters the mold. If the pressure is too high, it can cause the part to distort. If it is too low, the mold may not fill correctly.
A skilled Mold Maker adjusts the injection pressure carefully. They ensure the right pressure for each material and mold design. This is essential for maintaining dimensional stability.
6. Cooling Time and Temperature
Cooling is one of the most important factors in Electronic Injection Molding. If the part cools too quickly or too slowly, it may warp or shrink unevenly.
The Mold Maker ensures that the mold has an effective cooling system. This system helps the part cool uniformly. The right cooling time and temperature reduce dimensional changes.
7. Balancing Mold Temperature
Mold temperature is another crucial factor. If the mold is too hot or too cold, the part may not form correctly. Uneven temperatures lead to warping and other issues.
A skilled Mold Maker maintains a consistent mold temperature. This keeps the part dimensions stable.
8. Using Temperature-Controlled Molds
For parts with high precision needs, temperature-controlled molds are used. These molds have built-in temperature control systems. They can keep the mold at a constant temperature throughout the cycle.
This helps ensure that Electronic Injection Molding remains stable and accurate. It prevents size changes due to temperature fluctuations.
9. Mold Material Selection
Just like the plastic material, the mold material matters. Steel molds are strong and can last longer, but they are slower to heat and cool. Aluminum molds cool faster but wear out faster.
The Mold Maker picks the best material for the job. They ensure that the mold material complements the plastic material. This choice affects the final part’s dimensional stability.
10. Monitoring the Process
Continuous monitoring of the Electronic Injection Molding process is essential. By using sensors and data analysis, any shifts in pressure, temperature, or material flow can be detected.
The Mold Maker works with the machine operators to monitor these conditions. Regular checks ensure that everything stays on track. If something goes wrong, they can correct it immediately.
11. Part Orientation
Part orientation affects how the material cools. If the part is not positioned correctly in the mold, it may not cool evenly. Uneven cooling leads to warping and dimensional shifts.
A Mold Maker considers part orientation during design. Proper part placement in the mold reduces the chance of instability.
12. Using Gas-Assisted Molding
Gas-assisted molding uses gas to help form the part. It can reduce material usage and also control shrinkage. By injecting gas into the mold, the plastic solidifies more evenly.
For Electronic Injection Molding, gas-assisted molding can help control dimensional stability. A skilled Mold Maker will decide when this method is appropriate.
13. Mold Venting and Air Traps
Mold venting is critical for dimensional stability. If air gets trapped in the mold, it can cause uneven filling or warping. The Mold Maker designs vents to allow air to escape. This ensures even filling and reduces air pockets.
14. Quality Control and Inspection
After molding, each part must be inspected for dimensional accuracy. The Mold Maker works with the quality control team to ensure all parts meet specifications.
They may use tools like laser scanners or CMMs (coordinate measuring machines) to check the dimensions of the parts. This helps catch any dimensional issues before they become a problem.
15. Post-Molding Operations
Even after the parts are molded, post-molding operations can affect dimensional stability. These operations include trimming, assembly, or coating.
The Mold Maker ensures that these processes do not affect the part’s dimensions. They carefully consider how these steps interact with the molded part.
16. Understanding Shrinkage and Compensation
All plastics shrink during cooling. This shrinkage can cause the part to become smaller than expected. To prevent this, the Mold Maker compensates for shrinkage during the mold design phase.
They take the material’s shrinkage rate into account and adjust the mold dimensions accordingly. This compensation ensures that the final part remains the correct size.
17. Reducing Warping in Electronic Parts
Warping is another challenge in Electronic Injection Molding. It happens when the part cools unevenly. Warping can affect the fit and function of electronic parts.
The Mold Maker designs the mold to prevent warping. They use techniques like uniform cooling and mold material selection to control this issue.
18. Overcoming Mold Wear and Tear
Molds wear out over time. This wear can lead to changes in part dimensions. Regular maintenance and inspection are key.
The Mold Maker regularly checks the mold for signs of wear. They replace worn parts before they affect the final product.
19. Testing and Validation
Once the mold is set up, extensive testing is done to ensure dimensional stability. The Mold Maker runs several test cycles to check if the parts meet the required specifications.
Any deviations are corrected before full production begins. This testing phase ensures that the parts will remain stable throughout production.
Dimensional stability is crucial in Electronic Injection Molding. A skilled Mold Maker plays a key role in ensuring that electronic parts remain precise and functional. From mold design to material choice and cooling, every step counts.
By carefully controlling the process and continuously monitoring the conditions, dimensional stability can be maintained. This leads to high-quality, reliable electronic parts that meet the stringent requirements of the industry.