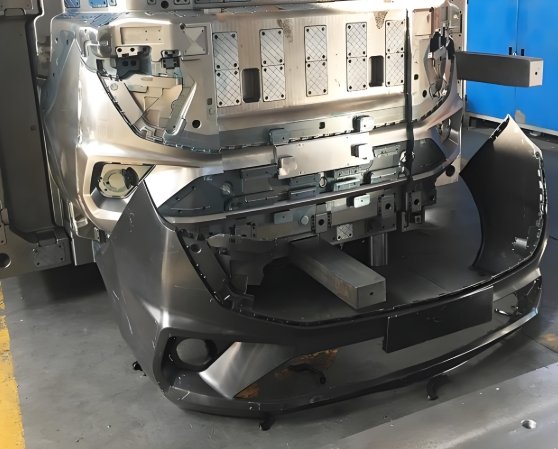
Automotive Injection Molds are essential for producing high-quality automotive components at a lower cost. The process is efficient and can produce large quantities of parts quickly. Mold Makers help optimize designs, ensuring that manufacturing remains affordable while maintaining precision and durability.
What Are Automotive Injection Molds?
Automotive Injection Molds are used to create various automotive components. These molds are made of metal and shaped to form parts by injecting molten material into them. The mold cools and hardens, forming the desired part. Common components include bumpers, dashboards, and door panels.
How Automotive Injection Molds Help Reduce Costs
1. Mass Production
One of the main advantages of Automotive Injection Molds is their ability to mass-produce parts quickly. Once the mold is created, manufacturers can produce thousands of identical parts in a short time. This reduces per-unit costs and makes large-scale production cost-effective.
2. Minimal Waste
The injection molding process is efficient with minimal material waste. Unlike other manufacturing methods, excess material is often reused, reducing the cost of raw materials. This makes the process more cost-efficient for manufacturers.
3. Faster Production
Injection molding allows for high-speed production of automotive parts. Once the mold is ready, the actual molding process takes seconds to minutes, depending on the part. This speed reduces labor costs and increases output, leading to lower overall production costs.
The Role of Mold Makers in Cost-Effective Manufacturing
1. Design Optimization
A skilled Mold Maker can optimize the design of the mold to improve efficiency. By creating molds that are easy to manufacture and maintain, Mold Makers help reduce production time and costs. They also consider the materials used in the mold to minimize costs while maintaining quality.
2. Material Selection
Choosing the right materials is essential for cost-effective molding. Mold Makers use durable materials that ensure the mold lasts for many cycles without needing to be replaced. This reduces downtime and the need for frequent replacements, which cuts costs in the long run.
3. Reducing Scrap and Defects
A well-designed mold minimizes defects and scrap. Mold Makers ensure that the mold produces parts to precise specifications, reducing the need for rework or discarded parts. This ensures that manufacturers only pay for the parts that meet quality standards.
Benefits of Automotive Injection Molds for Cost-Effective Manufacturing
1. High Precision
Automotive Injection Molds are known for their precision. Parts are created with exact measurements and details, reducing the chances of errors. This means fewer defective parts, less rework, and lower costs.
2. Long-Term Durability
Injection molds are designed to last for a long time. Mold Makers create molds that can produce hundreds of thousands of parts without significant wear. This durability ensures that manufacturers can keep production costs down over time.
3. Complex Parts at Low Costs
The injection molding process can create complex parts with ease. The ability to produce intricate shapes reduces the need for additional processing or assembly steps. This lowers labor and manufacturing costs.
Materials Used in Automotive Injection Molds
1. Steel
Steel is a common material used in Automotive Injection Molds. It’s strong, durable, and can withstand the high temperatures used in injection molding. Steel molds are ideal for mass production and can last for millions of cycles.
2. Aluminum
Aluminum is lighter and less expensive than steel. It’s often used for smaller production runs or when lower upfront costs are essential. Aluminum molds are faster to make and can be used for producing parts in a short time.
3. Alloy Materials
Alloy materials combine the benefits of steel and aluminum. They are strong yet cost-effective. Mold Makers often use alloys to balance cost and performance, creating molds that are both durable and affordable.
Challenges in Cost-Effective Automotive Injection Mold Manufacturing
1. Initial Mold Cost
One challenge is the high initial cost of creating an injection mold. Designing and building the mold requires skilled labor and expensive materials. However, this cost is offset over time through high-volume production, making it cost-effective in the long run.
2. Complexity of Parts
Some automotive parts are complex and require intricate molds. Designing these molds can be costly, and the production process may require more time and resources. However, the cost of complexity is balanced by the reduction in post-production work.
3. Material Costs
The cost of raw materials for molding can fluctuate. Mold Makers need to choose materials that offer the best balance between cost, performance, and durability to keep production costs low.
How Automotive Injection Molds Ensure Quality and Cost-Effectiveness
1. Precision and Consistency
Automotive Injection Molds ensure that each part produced is identical in shape and size. This precision leads to fewer defects and less waste, making the manufacturing process more cost-effective.
2. Shorter Cycle Times
Shorter cycle times allow manufacturers to produce more parts in less time. This reduces labor costs and increases overall production efficiency.
3. Reduced Need for Post-Processing
Injection molding produces parts with smooth surfaces and precise dimensions. This reduces the need for additional finishing work, which lowers labor and material costs.
Future Trends in Cost-Effective Automotive Injection Molds
1. 3D Printing for Molds
3D printing technology is increasingly used to create prototype molds quickly and affordably. This technology allows for faster mold development, which reduces time-to-market and costs.
2. Eco-Friendly Materials
As sustainability becomes more important, manufacturers are exploring eco-friendly materials for Automotive Injection Molds. These materials are both cost-effective and environmentally friendly, which appeals to both consumers and manufacturers.
3. Smart Manufacturing
The use of AI and automation in mold production is expected to increase. These technologies will improve efficiency, reduce errors, and further lower the cost of Automotive Injection Molds.
Automotive Injection Molds are a cost-effective solution for manufacturing high-quality automotive components. By optimizing designs, selecting the right materials, and reducing waste, manufacturers can produce large volumes of parts quickly and affordably. Skilled Mold Makers play a key role in ensuring that molds are both durable and cost-effective. As technologies continue to advance, the future of Automotive Injection Molds looks even more promising, offering new ways to further reduce costs and improve production efficiency.