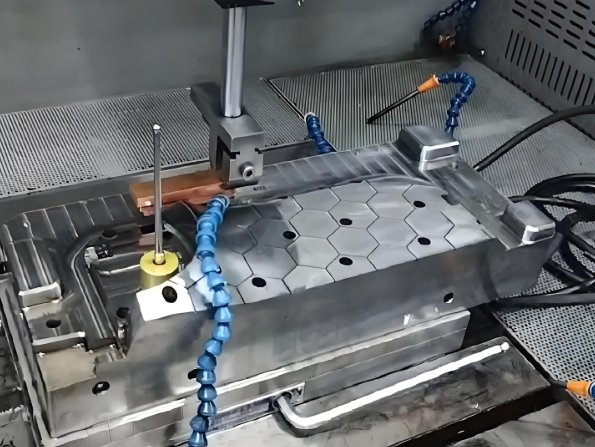
Car parts need strength and precision. Automotive injection molds create durable components. A skilled mold maker ensures accuracy and quality.
Why Durability Matters in Automotive Parts
1. Safety and Performance
Strong parts improve vehicle safety. Automotive injection molds help maintain structural integrity. A mold maker ensures proper design.
2. Longevity and Reliability
Durable components last longer. Automotive injection molds reduce wear and tear. A mold maker selects tough materials.
3. Cost-Effectiveness
Long-lasting parts lower maintenance costs. Automotive injection molds enhance durability. A mold maker optimizes production.
Key Automotive Components Made with Injection Molding
1. Engine Covers
Heat-resistant plastics protect engines. Automotive injection molds shape these covers. A mold maker ensures precise dimensions.
2. Bumpers and Grilles
Strong plastics absorb impact. Automotive injection molds produce flexible bumpers. A mold maker improves crash resistance.
3. Dashboard Panels
Dashboards must be durable. Automotive injection molds create sleek, sturdy designs. A mold maker ensures smooth finishes.
4. Air Intake Manifolds
Manifolds manage airflow efficiently. Automotive injection molds create lightweight, durable manifolds. A mold maker ensures proper airflow.
5. Fuel System Components
Fuel tanks require strength. Automotive injection molds produce leak-proof tanks. A mold maker ensures chemical resistance.
Materials for Durable Automotive Injection Molds
1. Polypropylene (PP)
PP is lightweight and strong. Automotive injection molds use PP for interior and exterior parts. A mold maker ensures flexibility.
2. Polycarbonate (PC)
PC resists heat and impact. Automotive injection molds shape durable lighting covers. A mold maker ensures high optical clarity.
3. Nylon (PA)
Nylon is wear-resistant. Automotive injection molds use PA for gears and engine components. A mold maker ensures high strength.
4. ABS (Acrylonitrile Butadiene Styrene)
ABS is tough and flexible. Automotive injection molds use ABS for dashboard trims. A mold maker ensures smooth designs.
Advanced Injection Molding Techniques for Durability
1. Multi-Shot Molding
Different materials improve strength. Automotive injection molds now combine multiple plastics. A mold maker ensures proper bonding.
2. Gas-Assisted Molding
Hollow structures reduce weight. Automotive injection molds use gas-assisted methods. A mold maker optimizes part strength.
3. Overmolding
Extra layers add protection. Automotive injection molds enhance part durability. A mold maker combines materials for better performance.
4. High-Precision Tooling
Accurate molds improve quality. Automotive injection molds need tight tolerances. A mold maker ensures exact specifications.
Challenges in Automotive Injection Molding
1. High Heat Resistance
Car engines generate heat. Automotive injection molds require heat-resistant plastics. A mold maker selects high-performance materials.
2. Complex Designs
Car parts have intricate shapes. Automotive injection molds must be highly detailed. A mold maker uses precision techniques.
3. Material Shrinkage
Plastics shrink after cooling. Automotive injection molds must account for this. A mold maker adjusts designs for accuracy.
4. Sustainability Requirements
Eco-friendly materials are essential. Automotive injection molds now use recyclable plastics. A mold maker focuses on green solutions.
Innovations in Automotive Injection Molding
1. Smart Sensors in Molds
Sensors detect defects early. Automotive injection molds now include real-time monitoring. A mold maker ensures consistent quality.
2. 3D Printing for Mold Prototyping
Prototypes speed up production. Automotive injection molds benefit from 3D-printed samples. A mold maker tests designs quickly.
3. AI in Mold Design
AI optimizes mold efficiency. Automotive injection molds now use data-driven designs. A mold maker improves precision with AI insights.
4. Automated Injection Molding
Automation reduces errors. Automotive injection molds now integrate robotic systems. A mold maker ensures high-speed production.
Future of Durable Automotive Injection Molds
1. Lighter, Stronger Plastics
New materials enhance durability. Automotive injection molds will use advanced composites. A mold maker selects stronger alternatives.
2. Faster Mold Cycles
Technology improves production speed. Automotive injection molds will feature quicker cycles. A mold maker refines cooling and injection methods.
3. Sustainability in Injection Molding
Green solutions reduce waste. Automotive injection molds will use biodegradable plastics. A mold maker focuses on eco-friendly innovations.
4. Improved Customization
Car designs are evolving. Automotive injection molds will allow more customization. A mold maker adapts to new design trends.
Durability is key in automotive manufacturing. Automotive injection molds produce high-quality, long-lasting components. A skilled mold maker ensures strength, efficiency, and sustainability. The future of injection molding promises even more advanced techniques and materials.