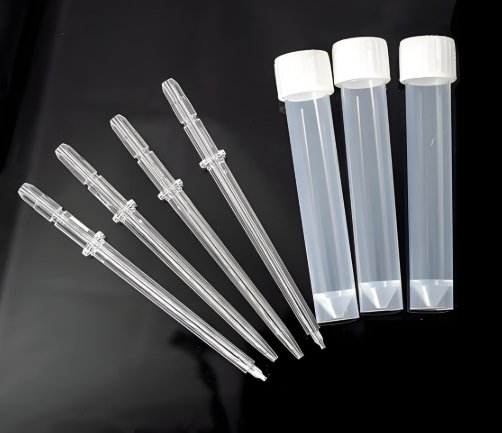
Cost control is crucial in medical injection molding. Many factors influence production expenses, from material selection to tooling and automation. Mold makers play a key role in optimizing efficiency and reducing costs while ensuring high-quality medical components. Understanding these factors helps manufacturers make cost-effective decisions.
1. Material Selection and Cost Impact
1.1 Type of Medical-Grade Plastics
- High-performance plastics (e.g., PEEK, PPSU) are expensive but durable.
- Standard thermoplastics (e.g., PP, PE) are cheaper but may lack durability.
1.2 Biocompatibility and Compliance
- FDA and ISO-approved materials cost more due to strict safety standards.
- Some materials require additional testing, adding to expenses.
1.3 Recycled vs. Virgin Materials
- Recycled plastics lower costs but may not meet medical standards.
- Virgin medical-grade resins ensure purity but are more expensive.
1.4 Specialty Additives
- Antimicrobial, radiopaque, or conductive additives increase costs.
- Enhances product functionality but requires extra processing.
2. Mold Design and Tooling Costs
2.1 Complexity of the Mold
- Simple molds with fewer cavities are cheaper to produce.
- Multi-cavity molds increase output but have higher initial costs.
2.2 Mold Material Selection
- Aluminum molds are affordable but wear out faster.
- Steel molds last longer but have higher upfront costs.
2.3 Hot vs. Cold Runner Systems
- Hot runner molds reduce material waste but cost more initially.
- Cold runner molds are cheaper but create more scrap.
2.4 Mold Longevity and Maintenance
- Well-maintained molds last longer, reducing long-term costs.
- Poorly designed molds require frequent repairs, increasing downtime.
3. Production Volume and Cycle Time
3.1 High vs. Low Volume Production
- High-volume runs lower per-part costs.
- Low-volume production requires frequent mold changes, increasing costs.
3.2 Cycle Time Optimization
- Faster cycle times reduce labor and energy costs.
- Poorly optimized cycles increase waste and downtime.
3.3 Automation in Production
- Robotic systems lower labor costs but require investment.
- Manual labor increases operational expenses over time.
4. Labor and Workforce Expenses
4.1 Skilled vs. Unskilled Labor
- Skilled operators reduce defects but demand higher wages.
- Training costs add to production expenses.
4.2 Operator-to-Machine Ratio
- Higher automation reduces labor costs.
- Fewer workers managing multiple machines increases efficiency.
4.3 Shift Schedules and Overtime
- Round-the-clock production lowers per-part cost.
- Overtime pay increases overall manufacturing costs.
5. Energy Consumption and Facility Costs
5.1 Machine Energy Efficiency
- Electric injection molding machines use less energy than hydraulic models.
- Hybrid systems offer a balance of power and efficiency.
5.2 Cooling and Heating Costs
- Efficient cooling systems reduce energy consumption.
- Poorly maintained cooling leads to longer cycle times and higher costs.
5.3 Factory Overhead Expenses
- Rent, utilities, and facility maintenance affect overall production costs.
- Lean manufacturing reduces space requirements and overhead.
6. Regulatory Compliance and Quality Standards
6.1 FDA and ISO Certification Costs
- Compliance requires extensive documentation and testing.
- Regular audits and inspections add to long-term costs.
6.2 Cleanroom Manufacturing
- ISO 14644 cleanrooms are costly to maintain.
- Required for sterile medical components but increases production expenses.
6.3 Quality Control and Testing
- AI-powered inspection reduces labor but adds software costs.
- Manual inspections increase labor costs but ensure compliance.
7. Supply Chain and Logistics Expenses
7.1 Raw Material Sourcing
- Local suppliers reduce shipping costs.
- Importing medical-grade plastics increases expenses due to tariffs and duties.
7.2 Just-in-Time (JIT) Inventory
- Lowers storage costs but requires reliable suppliers.
- Delayed shipments can halt production, increasing downtime.
7.3 Shipping and Packaging
- Sterile packaging for medical devices is costly.
- Bulk shipments lower per-unit shipping costs.
8. Waste Management and Sustainability Costs
8.1 Scrap Reduction Strategies
- AI-driven systems optimize material use.
- Poorly calibrated machines increase material waste.
8.2 Recycling and Reuse of Materials
- Some medical plastics are recyclable, reducing raw material costs.
- Certain applications require only virgin materials, increasing expenses.
8.3 Sustainable Manufacturing Initiatives
- Green energy solutions reduce long-term costs.
- Biodegradable materials often cost more but meet environmental regulations.
9. Technological Advancements and Automation
9.1 AI and IoT-Enabled Systems
- AI optimizes molding parameters to reduce waste.
- IoT-connected machines prevent costly defects before they occur.
9.2 Robotics in Production
- Reduces labor costs over time.
- Initial investment in automation is expensive.
9.3 3D Printing for Mold Prototyping
- Lowers development costs for new molds.
- Reduces trial-and-error in mold design.
10. Future Trends in Cost Reduction for Medical Injection Molding
10.1 Fully Automated Smart Factories
- AI-driven production will reduce manual labor costs.
- Smart scheduling will optimize machine usage.
10.2 Sustainable Medical Plastics
- New bioplastics will lower material costs.
- Improved recycling programs will reduce waste.
10.3 Blockchain for Supply Chain Transparency
- Reduces fraud and improves procurement efficiency.
- Ensures raw materials meet medical-grade standards.
10.4 Predictive Maintenance for Cost Control
- IoT-enabled machines will detect wear before failure.
- Reduces unplanned downtime and repair costs.
10.5 Digital Twins for Process Optimization
- Virtual simulations prevent production errors.
- Lowers scrap rates and boosts efficiency.
Many factors affect medical injection molding costs. Mold makers help manufacturers optimize mold design, material selection, and automation to control expenses. By adopting AI, IoT, and energy-efficient solutions, companies can maintain high-quality production while reducing costs.