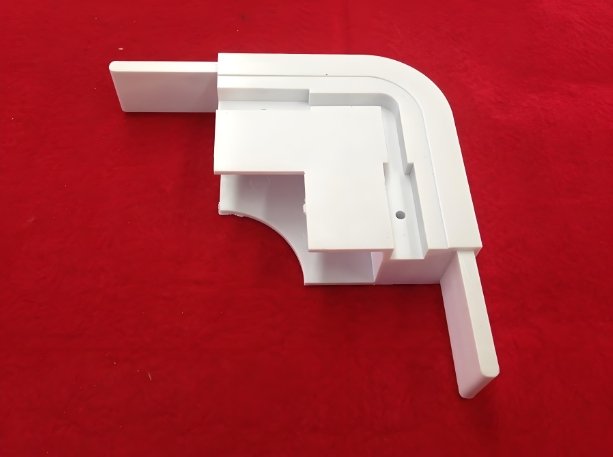
In today’s electronics world, products are getting smaller, thinner, and smarter. Devices like hearing aids, medical sensors, micro-connectors, and wearable tech all demand parts so small that even a tiny flaw can cause failure. To meet this challenge, manufacturers now depend on high-precision tooling in Electronic Injection Molding.
A skilled Mold Maker plays a key role in making this possible. They create ultra-accurate molds that produce tiny parts with perfect detail, strength, and consistency. In this article, we’ll explore why precision tooling matters, how it’s done, and why the future of electronics depends on it.
Why Precision Matters in Electronic Injection Molding
In Electronic Injection Molding, precision is everything. Small parts often have tiny features, thin walls, or complex shapes. If the mold is even slightly wrong, the parts may not fit, work, or last. In critical industries like healthcare or aerospace, failure is not an option.
High-precision tooling ensures:
- Exact dimensions for tight fits and seals
- Smooth surfaces for better performance and looks
- High strength even in tiny parts
- Reliable repeatability across millions of cycles
A skilled Mold Maker understands that making these ultra-small parts isn’t just about shrinking regular molds—it requires a whole new level of care and technology.
What Makes a Mold “High-Precision”?
High-precision molds must meet incredibly tight tolerances. In some cases, dimensions must be accurate within a few microns (one micron is 1/1000th of a millimeter).
Key features of precision molds include:
- Ultra-smooth cavity surfaces
- Very fine edges and small details
- Accurate parting lines
- Perfect venting to avoid air traps
- Consistent temperature control for even molding
Creating such molds requires not just high-end machines but also deep knowledge. That’s why finding the right Mold Maker is critical for success in Electronic Injection Molding.
Tools and Technologies Used in Precision Molding
Advanced technology supports high-precision Electronic Injection Molding. Here are some of the tools and methods top Mold Makers use:
1. CNC Micromachining
High-end CNC machines can carve molds with incredible accuracy. These machines use fine-tipped cutters that can create tiny shapes and features without damaging the material.
2. EDM (Electrical Discharge Machining)
EDM uses electrical sparks to cut metals. It’s perfect for making very small, detailed parts that normal cutting tools can’t handle.
3. Laser Texturing
Laser beams create patterns or textures on the mold surface. This is useful for tiny logos, anti-slip textures, or specific functional surfaces in electronics.
4. High-Resolution 3D Scanning
After creating a mold, Mold Makers use 3D scanners to check every detail. This ensures the mold matches the design exactly before mass production begins.
5. Cleanroom Molding
For sensitive electronic parts, production often happens in cleanrooms. These are dust-free environments where precision molding can happen without contamination.
Materials Used for Ultra-Small Electronic Parts
Choosing the right material is just as important as choosing the right process. In Electronic Injection Molding, small parts often need special plastics that offer:
- High strength
- Dimensional stability
- Heat resistance
- Electrical insulation
- Chemical resistance
Popular materials include:
- LCP (Liquid Crystal Polymer): Excellent for micro-connectors and sensors.
- PEEK (Polyether Ether Ketone): High strength and chemical resistance.
- Polycarbonate: Clear and tough for lenses and casings.
- Nylon 6/6: Strong and easy to mold for many types of parts.
A skilled Mold Maker can recommend the best material based on part function, molding difficulty, and long-term reliability.
Challenges in Precision Electronic Injection Molding
Making ultra-small parts isn’t easy. Several problems can arise if the Mold Maker isn’t careful:
- Short shots: When the mold doesn’t fill completely.
- Flash: Thin excess material where mold halves meet.
- Warping: Uneven cooling can distort small parts.
- Burn marks: Caused by trapped air or overheating.
Precision tooling, proper mold design, and exact machine settings help avoid these problems. Top Mold Makers plan for these challenges from the very beginning.
Applications of Ultra-Small Parts in Electronics
Ultra-small components made with high-precision Electronic Injection Molding are found in many industries:
- Medical Devices: Sensors, drug delivery systems, implantable devices.
- Consumer Electronics: Smartphones, earbuds, wearable tech.
- Automotive: Micro-switches, cameras, advanced driver assistance systems.
- Industrial: IoT sensors, connectors, miniature controls.
Each of these industries demands absolute quality and reliability, making high-precision molds even more important.
The Role of the Mold Maker
The Mold Maker is the heart of precision Electronic Injection Molding. Their work includes:
- Designing the mold with high-end software
- Selecting the right steel and materials
- Machining parts to micron-level tolerances
- Assembling and polishing the mold with extreme care
- Testing and adjusting until the mold runs perfectly
Without a talented Mold Maker, even the best machines can’t produce perfect parts. Their craftsmanship and experience ensure every mold is built to last and to perform under tough production demands.
Future of High-Precision Molding in Electronics
As electronics continue shrinking, the demand for precision Electronic Injection Molding will only grow. In the future, we expect:
- Even smaller parts for medical implants and nanotechnology.
- Smarter molds with built-in sensors to monitor quality in real time.
- Faster prototyping with 3D printing and hybrid techniques.
- Greener materials that reduce environmental impact.
Mold Makers who invest in new skills, software, and machines will lead the future of the industry. Their role will become even more important as technology evolves.
High-precision tooling is the foundation of success for ultra-small parts in Electronic Injection Molding. Today’s electronics would not be possible without the skill, experience, and technology provided by expert Mold Makers.
From choosing the right material to building perfect molds, every step matters. As devices get smaller and smarter, the need for precise, reliable, and scalable solutions will only grow.
Working with a trusted Mold Maker ensures that even the tiniest parts will meet the highest standards—giving electronics companies the edge they need in a fast-moving world. In Electronic Injection Molding, precision isn’t just a feature—it’s the key to innovation.