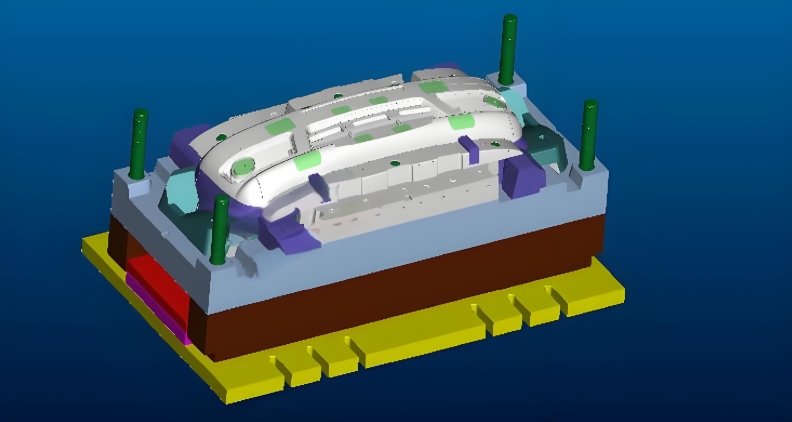
Modern vehicles require precise components. Automotive injection molds create these parts with high accuracy. A skilled mold maker ensures perfect fit, strength, and durability. High-tech mold-making processes improve efficiency and reduce costs. Advanced techniques allow complex shapes and lightweight designs.
Why High-Tech Molding Matters?
1. Precision in Automotive Parts
Every vehicle part must meet strict standards. Automotive injection molds ensure accuracy. A professional mold maker guarantees tight tolerances.
2. Faster Production Cycles
Advanced molding processes speed up production. High-tech machines reduce cycle times. Mold makers optimize efficiency.
3. Lightweight and Strong Materials
Modern cars need strong yet lightweight parts. High-tech molding uses advanced polymers. A mold maker selects the best materials.
4. Cost Reduction and Waste Minimization
Technology reduces material waste. Automotive injection molds maximize efficiency. A skilled mold maker minimizes production costs.
Key High-Tech Mold Making Processes
1. Computer-Aided Design (CAD) and Simulation
CAD software designs precise mold structures. Simulation tests mold performance before production. A mold maker ensures accuracy using digital models.
2. High-Speed CNC Machining
CNC machines carve molds with extreme precision. These machines create smooth and detailed surfaces. Automotive injection molds require this high-tech process.
3. Electric Discharge Machining (EDM)
EDM shapes hard metals with electrical sparks. It allows fine details and sharp edges. A skilled mold maker uses EDM for complex designs.
4. Laser Cutting and Engraving
Lasers cut intricate patterns into molds. Engraving improves part identification. Automotive injection molds benefit from this precision process.
5. 3D Printing for Rapid Prototyping
3D printing creates mold prototypes quickly. It reduces development time. A mold maker tests designs before final production.
6. Multi-Cavity Molding
Multi-cavity molds produce multiple parts at once. This increases efficiency. Automotive injection molds often use this high-tech process.
7. Gas-Assisted Injection Molding
Gas injection reduces material usage. It creates lightweight yet strong parts. A mold maker ensures proper gas distribution.
8. Hot Runner Systems
Hot runners keep plastic melted inside the mold. This prevents waste and speeds up production. Automotive injection molds with hot runners improve efficiency.
Materials Used in High-Tech Mold Making
1. High-Performance Plastics
Modern molds use strong, lightweight plastics. These materials improve fuel efficiency. A mold maker selects heat-resistant polymers.
2. Metal Inserts for Strength
Some molds combine plastic with metal inserts. This increases durability. Automotive injection molds use this for structural parts.
3. Composite Materials
Composites reduce weight without losing strength. Advanced mold makers work with carbon fiber and reinforced plastics.
Applications of High-Tech Automotive Molds
1. Interior Components
Dashboards, panels, and trim require precise molds. Automotive injection molds create durable, stylish interiors. A mold maker ensures perfect fit and finish.
2. Exterior Parts
Bumpers, grilles, and side panels need tough molds. High-tech processes ensure strong, impact-resistant parts. Mold makers use precision techniques for smooth finishes.
3. Engine and Fuel System Components
Modern fuel systems require exact tolerances. High-tech automotive injection molds create reliable fuel tanks, pumps, and connectors. A mold maker ensures leak-proof designs.
4. Lighting Systems
Headlights and taillights need clear, precise molds. Advanced molding techniques ensure optical clarity. A mold maker polishes molds for flawless lenses.
5. Safety Components
Airbags, seatbelt housings, and crash-resistant parts use high-tech molds. Automotive injection molds must meet strict safety standards. A skilled mold maker guarantees durability.
Challenges in High-Tech Mold Making
1. Achieving Tight Tolerances
Automotive parts require extreme precision. Even minor defects cause issues. A skilled mold maker ensures high accuracy.
2. Managing Complex Designs
Modern vehicles have intricate components. Automotive injection molds must capture every detail. High-tech software helps mold makers create perfect designs.
3. Reducing Cycle Times
Faster production means lower costs. High-tech molding techniques improve efficiency. Mold makers constantly refine processes.
4. Adapting to New Materials
The auto industry uses new materials often. must adapt to different plastics. A mold maker stays updated on the latest innovations.
Future Trends in High-Tech Mold Making
1. Smart Molds with Sensors
Future molds will have built-in sensors. These will track pressure, temperature, and performance. Mold makers will use real-time data to improve quality.
2. AI-Driven Design Optimization
Artificial intelligence will optimize mold designs. AI can predict issues before production. Automotive injection molds will become more efficient.
3. Sustainable Mold Making
Eco-friendly materials will reduce waste. Mold makers will use recyclable plastics and biodegradable composites.
4. Fully Automated Molding Lines
Automation will speed up production. Robots will assist mold makers in creating perfect molds.
High-tech processes transform automotive injection molds. Precision, speed, and efficiency define modern mold making. A skilled mold maker ensures strong, reliable parts. As technology advances, molding techniques will continue to improve.