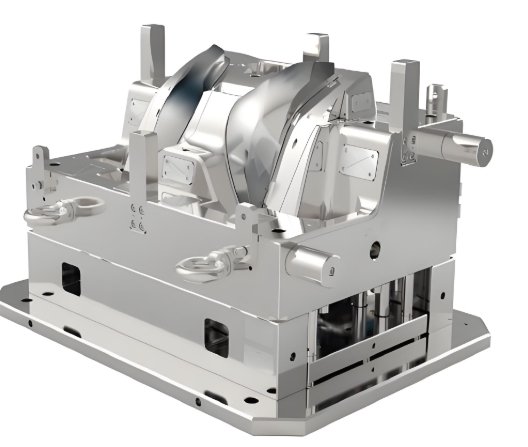
Automotive parts require precision and speed. Automotive injection molds make high-volume production possible. A skilled mold maker ensures quality and efficiency.
Why High-Volume Production Matters
1. Faster Manufacturing
Speed is critical in the auto industry. Automotive injection molds produce thousands of parts quickly. A mold maker ensures rapid cycles.
2. Cost Reduction
Mass production lowers costs. Automotive injection molds reduce material waste. A mold maker optimizes designs for efficiency.
3. Consistent Quality
Every part must be identical. Automotive injection molds maintain precision. A mold maker ensures accurate molds.
4. Meeting Industry Demand
The auto industry requires millions of parts. Automotive injection molds support high demand. A mold maker helps manufacturers scale up.
Materials for High-Volume Injection Molding
1. ABS (Acrylonitrile Butadiene Styrene)
ABS is strong and lightweight. Automotive injection molds use ABS for dashboards and trims. A mold maker ensures perfect finishes.
2. Polypropylene (PP)
PP is flexible and impact-resistant. Automotive injection molds use PP for interior panels. A mold maker selects PP for durability.
3. Polycarbonate (PC)
PC withstands heat and pressure. Automotive injection molds use PC for headlights. A mold maker ensures high clarity and strength.
4. Nylon (PA)
Nylon is wear-resistant. Automotive injection molds use nylon for gears and under-hood parts. A mold maker ensures precision in complex shapes.
Key Processes in High-Volume Injection Molding
1. Mold Design and Engineering
A good mold ensures quality. Automotive injection molds need exact specifications. A mold maker uses CAD software for precise designs.
2. Material Selection
Choosing the right plastic is crucial. Automotive injection molds must handle high stress. A mold maker selects materials for strength and flexibility.
3. Injection Molding Process
Molten plastic is injected into the mold. Automotive injection molds shape parts under high pressure. A mold maker ensures even distribution.
4. Cooling and Ejection
Cooling prevents defects. Automotive injection molds must have efficient cooling channels. A mold maker optimizes cooling for fast cycles.
5. Finishing and Quality Control
Parts need a smooth surface. Automotive injection molds create precise shapes. A mold maker inspects for defects before shipping.
Advantages of High-Volume Injection Molding
1. Fast Production Cycles
Molding is quicker than other methods. Automotive injection molds allow high-speed manufacturing. A mold maker fine-tunes the process for efficiency.
2. Lower Cost Per Part
Bulk production saves money. Automotive injection molds reduce labor costs. A mold maker designs molds for high output.
3. Minimal Material Waste
Optimized designs use less plastic. Automotive injection molds minimize scrap. A mold maker refines gates and runners to reduce excess.
4. Enhanced Precision
Tight tolerances matter. Automotive injection molds ensure exact dimensions. A mold maker maintains high accuracy in every part.
Challenges in High-Volume Production
1. Mold Wear and Tear
Frequent use damages molds. Automotive injection molds must be durable. A mold maker uses hardened steel for longevity.
2. Heat Management
High-speed production generates heat. Automotive injection molds need proper cooling. A mold maker optimizes cooling channels for efficiency.
3. Defects and Inconsistencies
Air bubbles and warping can occur. Automotive injection molds must be flawless. A mold maker tests molds for accuracy.
4. Cost of High-Quality Molds
Precision molds are expensive. Automotive injection molds require advanced tooling. A mold maker balances cost and performance.
Innovations in High-Volume Injection Molding
1. Multi-Cavity Molds
More cavities mean more parts per cycle. Automotive injection molds now use multi-cavity designs. A mold maker creates complex layouts for efficiency.
2. Automated Production
Robots improve speed and accuracy. Automotive injection molds now integrate automation. A mold maker programs machines for precision.
3. 3D Printing for Prototyping
Prototyping speeds up design. Automotive injection molds benefit from 3D-printed samples. A mold maker tests new designs before full production.
4. Smart Sensors in Molds
Sensors detect defects early. Automotive injection molds now have built-in monitoring. A mold maker uses data to optimize performance.
Future of High-Volume Injection Molding
1. Faster Cycle Times
Machines are getting faster. Automotive injection molds will soon have even quicker cycles. A mold maker improves efficiency with new designs.
2. Sustainable Materials
Recyclable plastics are the future. Automotive injection molds will use eco-friendly materials. A mold maker explores biodegradable options.
3. AI-Optimized Molding
Artificial intelligence improves production. Automotive injection molds will use AI for defect detection. A mold maker will rely on data for better results.
4. Lightweight Components
Automakers want lighter parts. Automotive injection molds will focus on weight reduction. A mold maker selects advanced composites for strength.
High-volume production keeps the auto industry moving. Automotive injection molds make mass manufacturing efficient. A skilled mold maker ensures precision, durability, and cost savings. Future innovations will push injection molding even further.