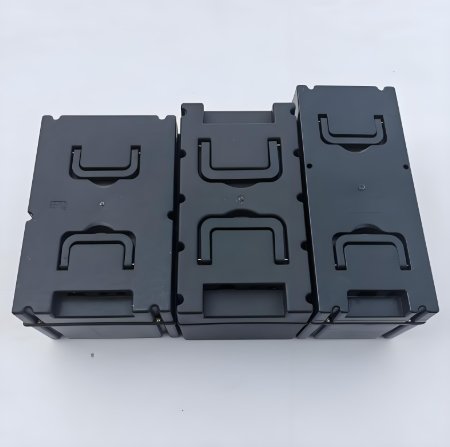
In Electronic Injection Molding, the choice of runner system is critical. Runners guide the molten plastic into the mold cavity. The right system impacts part quality, cycle time, and cost. Two common types of runner systems are hot runners and cold runners.
Understanding the differences helps choose the best option. A skilled Mold Maker knows which system to use based on production needs. Let’s dive deeper into these systems.
What Are Runner Systems?
Runner systems guide the plastic from the injection nozzle to the mold cavity. The system must be efficient. If it’s not, production slows, costs increase, and part quality decreases.
There are two main types of runner systems: hot runners and cold runners. Both have strengths and weaknesses.
How Hot Runner Systems Work
In a hot runner system, the runners are heated. This keeps the plastic in liquid form as it flows through the mold. The heat prevents the plastic from solidifying before entering the cavities.
Mold Makers use these systems for parts that require fast cycles or high-volume production. Hot runners are also ideal for complex molds with many cavities.
How Cold Runner Systems Work
In a cold runner system, the runners are not heated. They cool down as the plastic flows through. This causes the plastic to solidify in the runner. The solidified plastic is then removed from the mold. Cold runners are used in low- to medium-volume production.
Key Differences Between Hot and Cold Runner Systems
1. Material Waste
- Hot Runner: Less material waste. The plastic stays molten, so there’s no scrap.
- Cold Runner: More waste. The plastic cools and solidifies in the runner. This results in extra material that must be discarded.
For Electronic Injection Molding, reducing waste is essential for efficiency. The Mold Maker may recommend hot runners for this reason.
2. Cycle Time
- Hot Runner: Faster cycle times. The plastic is always ready to flow, which speeds up the process.
- Cold Runner: Slower cycle times. The runners need to cool, adding time to the cycle.
A faster cycle is important in Electronic Injection Molding, especially for high-volume parts. Mold Makers choose hot runners when time is critical.
3. Cost
- Hot Runner: Higher upfront costs. The system needs heating elements and controllers. It’s more expensive to install.
- Cold Runner: Lower upfront costs. No heating elements are needed.
While hot runner systems cost more initially, they can save money over time by reducing material waste and speeding up production. Mold Makers weigh these factors when deciding.
4. Complexity of Mold Design
- Hot Runner: More complex mold design. It requires precise control of temperature and pressure.
- Cold Runner: Simpler mold design. There’s less complexity to manage.
For high-precision parts in Electronic Injection Molding, a complex system may be necessary. However, it’s not always needed, and a Mold Maker must determine the best choice.
5. Maintenance
- Hot Runner: Requires more maintenance. The heating elements and controllers can wear out over time.
- Cold Runner: Easier to maintain. Without heating components, there’s less chance of failure.
In Electronic Injection Molding, molds are often used for many cycles. A Mold Maker will take maintenance needs into account when choosing the system.
6. Quality of Parts
- Hot Runner: Consistent part quality. The runners are always at the right temperature, leading to uniform flow and fewer defects.
- Cold Runner: Variations in part quality. The cooling and solidifying of plastic in the runner can lead to inconsistencies.
For high-quality electronic components, the Mold Maker may prefer hot runners to ensure consistent results.
When to Choose Hot Runner Systems
Hot runner systems are ideal in specific situations. Here’s when Mold Makers typically recommend them for Electronic Injection Molding:
- High-Volume Production: Hot runners are more efficient for large batches.
- Complex Molds: Multiple cavities or intricate designs benefit from hot runners.
- Reducing Waste: Hot runners eliminate scrap material, saving money in the long run.
- Faster Cycle Times: Hot runners reduce the overall cycle time, speeding up production.
When to Choose Cold Runner Systems
Cold runner systems are better for smaller-scale or less complex production. Here are some scenarios where cold runners make sense:
- Low-Volume Production: If you don’t need to produce high numbers of parts, cold runners are cost-effective.
- Simple Designs: For molds with fewer cavities and simpler shapes, cold runners work well.
- Lower Upfront Investment: If budget is a concern, cold runners can be a more affordable choice.
- Low-Waste Tolerance: If scrap material isn’t a major issue, cold runners can be used without significant downsides.
Factors to Consider in Electronic Injection Molding
The choice between hot and cold runners depends on various factors. Mold Makers consider:
- Part Complexity: High-precision or intricate parts need hot runners.
- Production Volume: For high volumes, hot runners are typically the better choice.
- Material Type: Some plastics perform better in hot runner systems.
- Budget: Cold runner systems are cheaper to set up initially.
- Part Quality: Consistent, high-quality parts often require hot runners.
In Electronic Injection Molding, precision is critical. The Mold Maker needs to consider all these factors to deliver the best results.
Pros and Cons Summary
Feature | Hot Runner System | Cold Runner System |
---|---|---|
Upfront Cost | High | Low |
Material Waste | Low | High |
Cycle Time | Short | Long |
Complexity | High | Low |
Maintenance | High | Low |
Part Quality | Consistent, high quality | Potential quality variations |
Both hot and cold runner systems have their places in Electronic Injection Molding. A skilled Mold Maker carefully selects the system based on the part’s needs, production volume, material, and budget. Hot runner systems offer faster cycles, less waste, and consistent quality, making them a go-to for high-volume and complex molds. Cold runner systems, on the other hand, are perfect for smaller, less complex runs where cost is a major concern.
Ultimately, the choice of runner system can make or break the success of your molding project. By working with an experienced Mold Maker, you can ensure the best system is selected for your needs, leading to efficient production and high-quality electronic parts.