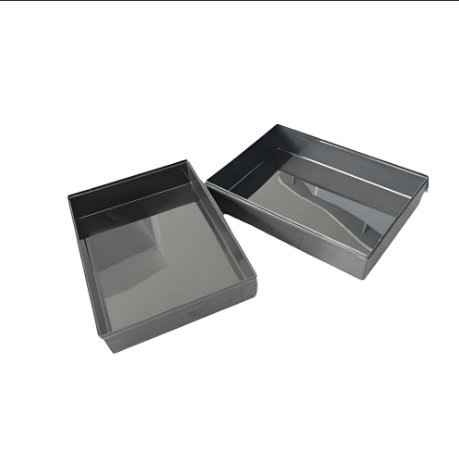
Plastic housings are essential in modern products—from home electronics to industrial tools. These outer shells do more than protect—they add shape, structure, and aesthetic value. One of the most effective ways to produce them is through Housing Injection Molding. This method offers speed, accuracy, and flexibility, making it the go-to choice for industries worldwide.
In this article, we’ll explore the full process of Housing Injection Molding, examine common materials, and explain how an expert Mold Maker plays a vital role in creating top-quality plastic enclosures.
What Is Housing Injection Molding?
Housing Injection Molding is the process of creating plastic housings by injecting molten plastic into a metal mold. These housings can serve as protective shells, covers, or structural parts. They are widely used in electronics, medical devices, appliances, and automotive parts.
The method is fast and reliable. It allows the production of thousands—or even millions—of identical parts. With the help of a skilled Mold Maker, manufacturers can ensure each part is precise and durable.
The Importance of a Good Mold Maker
The Mold Maker builds the tool used in the molding machine. This tool shapes the final housing. The quality of this mold affects the final product’s strength, look, and performance.
A skilled Mold Maker:
- Designs molds with proper cooling and venting
- Uses the right steel grade for durability
- Ensures the mold allows smooth part release
- Matches tight tolerances to product specs
Without a precise mold, even the best design can fail. That’s why the Mold Maker is a key part of any Housing Injection Molding project.
The Housing Injection Molding Process
Let’s go step by step through the full Housing Injection Molding process.
1. Part Design
Every project starts with a 3D model. This design includes all housing features: mounting holes, clips, ports, and more. The designer must ensure the part is moldable. That means:
- Adding draft angles
- Keeping wall thickness even
- Avoiding deep undercuts
- Planning for cooling and ejection
At this stage, the Mold Maker often advises on improvements to avoid defects later.
2. Mold Design
The Mold Maker now creates the mold based on the part design. The mold usually has two main halves: the core and the cavity. It also includes:
- Cooling lines
- Ejector pins
- Gates and runners
- Venting channels
The goal is a mold that creates clean, accurate housings every time.
3. Mold Fabrication
Next, the mold is machined, often using CNC and EDM. The Mold Maker works with great precision to match the part specs. They polish the surface and test for proper fit and alignment.
Once finished, the mold is installed in the injection molding machine.
4. Material Selection
Material choice affects the part’s strength, look, and feel. Common plastics for Housing Injection Molding include:
- ABS (Acrylonitrile Butadiene Styrene)
Tough, easy to mold, and cost-effective. Common in electronics. - Polycarbonate (PC)
Strong and clear. Often used in safety equipment or high-end electronics. - Polypropylene (PP)
Flexible and chemical-resistant. Good for medical housings. - Nylon (PA)
High mechanical strength. Useful for industrial or automotive use. - PC+ABS blend
Combines the strength of PC and the easy molding of ABS. Great for housings that require durability and finish.
The Mold Maker may recommend materials based on part size, wall thickness, or surface needs.
5. Injection Molding
Once the mold and material are ready, the machine heats plastic pellets into a liquid. Then:
- The machine injects molten plastic into the mold
- The plastic fills the cavity and cools
- The mold opens
- Ejector pins push the housing out
- The cycle repeats
This cycle can be very fast—often under a minute. A well-built mold by an expert Mold Maker reduces scrap and speeds up production.
Surface Finishes and Features
Housing Injection Molding allows many finishes and textures. These are applied to the mold itself.
- Glossy finish: Polished mold surfaces
- Matte or textured finish: Etched or blasted molds
- Soft-touch coating: Overmolding or post-treatment
These options are important for customer-facing products. The Mold Maker ensures the mold surface delivers the desired finish every time.
Common Design Features in Plastic Housings
Modern housings are not just shells. They often include:
- Snap fits or clips for tool-free assembly
- Bosses and ribs for added strength
- Mounting points for PCBs or batteries
- Vent holes or speaker grills
- Screw posts for secure fastening
These features must be designed carefully and built precisely. A good Mold Maker ensures the mold produces all these fine details correctly.
Benefits of Housing Injection Molding
There are many reasons why manufacturers choose this process:
1. Precision and Repeatability
Once the mold is built, each housing is identical. This is critical for parts that must fit other components.
2. Low Cost in High Volume
After the mold cost, the cost per part is very low—especially in high-volume production.
3. Speed
Thousands of housings can be made every day. This helps companies meet tight timelines.
4. Strength and Light Weight
Plastic housings are strong yet light, making them perfect for handheld and portable devices.
5. Design Flexibility
Complex shapes, logos, and fine details can all be molded in one step. The Mold Maker ensures the mold supports all design goals.
Challenges in the Process
Even great designs can face issues. Common problems include:
- Warping: Caused by uneven cooling
- Sink marks: From thick sections
- Short shots: When plastic doesn’t fill the mold completely
- Flash: When plastic leaks between mold halves
- Ejection marks: From poorly placed ejector pins
A skilled Mold Maker solves these problems by adjusting the mold design, adding cooling, or refining gate placement.
Housing Injection Molding is essential to modern manufacturing. It delivers durable, accurate, and attractive enclosures for many products. The process depends on good design, the right materials, and—most importantly—a professional Mold Maker.
The Mold Maker is more than just a tool builder. They are partners in quality, helping ensure that every housing is strong, functional, and beautiful. With the right support and experience, Housing Injection Molding can bring your product ideas to life—efficiently and reliably.