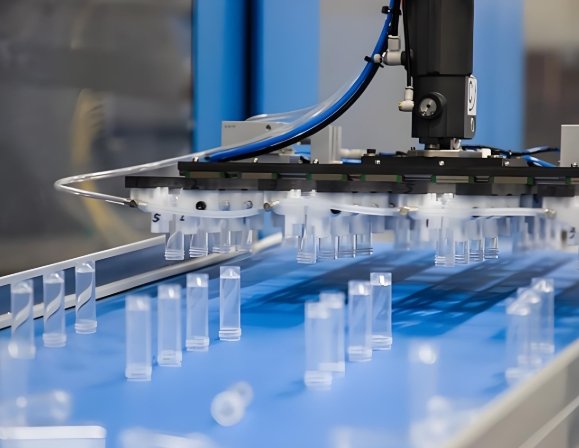
Drug delivery systems are vital in healthcare. They allow for precise and controlled release of medications. Medical injection molding plays an essential role in making these systems. It ensures the production of high-quality components with exact specifications. Mold makers design molds to meet stringent standards.
Why Injection Molding is Important for Drug Delivery Systems
1. High Precision and Consistency
Drug delivery systems need exact dimensions. Medical injection molding ensures that every part is uniform. This helps maintain the effectiveness and safety of the system.
2. Speed and Efficiency
Injection molding can produce large quantities of parts in a short time. This allows drug delivery systems to be manufactured quickly and cost-effectively.
3. Material Flexibility
A wide range of materials can be used for medical injection molding. This ensures that drug delivery systems have the required durability and biocompatibility.
4. Safety and Sterility
Components used in drug delivery must be sterile and safe. Mold makers choose materials that meet regulatory requirements to ensure the final product is safe for patients.
Types of Drug Delivery Systems Made Using Injection Molding
1. Syringe Systems
Syringes are one of the most common drug delivery devices. They must be designed for precision and leak-proof operation. Medical injection molding allows for high accuracy in syringe manufacturing.
2. Inhalers
Inhalers deliver medication directly to the lungs. Injection molding ensures the parts are precisely shaped and free from contamination.
3. Transdermal Patches
These patches deliver drugs through the skin. Injection molding helps create flexible, effective patches that are easy to use.
4. Infusion Pumps
Infusion pumps provide controlled, continuous delivery of medication. Injection molding is used to create durable, precise parts for these devices.
5. Implantable Drug Devices
Implants deliver medication over a longer period. These devices require high precision, which medical injection molding ensures.
6. Oral Dosage Forms
Certain drug delivery systems, like tablets or capsules, are made using injection molding. This helps ensure consistency in dosage and ease of production.
The Role of Mold Makers in Drug Delivery System Production
1. Designing the Mold
A mold maker designs the molds used to create drug delivery components. The design must meet stringent requirements for size, shape, and function.
2. Material Selection
Mold makers choose the best materials for each application. The materials must be biocompatible and able to withstand exposure to medication.
3. Ensuring Precision
Injection molding requires precise measurements. Mold makers ensure that the molds are perfectly crafted to create accurate parts.
4. Testing and Prototyping
Before full production, prototypes are tested. This ensures that the parts meet quality and safety standards.
5. Maintenance of Molds
To ensure longevity and consistent quality, molds need regular maintenance. Mold makers handle repairs and improvements to keep molds in top condition.
Challenges in Drug Delivery System Production
1. Regulatory Compliance
Drug delivery systems are subject to strict regulations. Mold makers ensure that all components meet FDA and ISO standards for safety and quality.
2. Biocompatibility
Drug delivery systems must be made from materials that are safe for patients. Mold makers select materials that won’t cause allergic reactions or toxicity.
3. Durability
Drug delivery systems must work consistently over time. Injection molding helps produce durable, long-lasting components.
4. Contamination Prevention
Medical devices must be sterile. Mold makers ensure that the manufacturing process avoids contamination, maintaining the cleanliness of each part.
Advanced Injection Molding Techniques for Drug Delivery Systems
1. Micro Molding
Micro molding is used to create small, intricate parts. This is especially important for drug delivery systems that require precise, miniature components.
2. Multi-Shot Molding
Multi-shot molding combines different materials in one piece. This is useful for creating complex drug delivery components that require multiple material properties.
3. Overmolding
Overmolding allows for the creation of complex parts with multiple layers. This technique is used in drug delivery devices to create seals, grips, and other critical features.
4. Biodegradable Materials
Some drug delivery systems need to degrade over time. Biodegradable plastics are used in the manufacturing of these devices to ensure safety and effectiveness.
The Future of Injection Molding in Drug Delivery Systems
1. Automation
Automation is transforming the manufacturing process. Robots and automated systems help improve efficiency and reduce human error.
2. Smart Drug Delivery Systems
Smart systems that monitor and adjust medication delivery are on the rise. Injection molding will play a role in creating the precise components needed for these advanced devices.
3. 3D Printing and Injection Molding Integration
Combining 3D printing and injection molding opens up new possibilities. This will allow for faster prototyping and production of drug delivery systems.
4. Sustainability
Sustainable materials are becoming more common in medical manufacturing. Mold makers are working to incorporate eco-friendly options into drug delivery system production.
Medical injection molding is vital for the production of drug delivery systems. It ensures high precision, efficiency, and safety. Mold makers play a critical role in creating molds that meet regulatory standards. As technology advances, the integration of new techniques and materials will continue to improve drug delivery systems, making healthcare more effective and accessible.