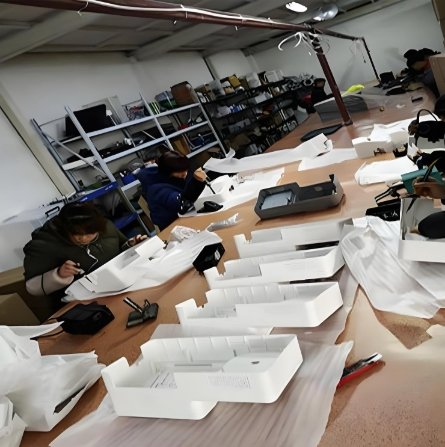
In Electronic Injection Molding, the quality of the final product is largely determined by the design of the mold. A skilled Mold Maker ensures that every part fits precisely and performs as required. Even small design flaws can lead to large problems. These include defects like warping, shrinkage, or poor material flow. Understanding how mold design affects the final product is key to producing high-quality electronic components.
Importance of Mold Design in Electronic Injection Molding
Mold design impacts the entire injection molding process. A well-designed mold helps ensure that the molded part meets specific standards. For electronic components, that means durability, precision, and functionality. The right design reduces defects and increases production efficiency. It also minimizes costly errors in production.
Role of the Mold Maker in Design
A Mold Maker is a key player in ensuring quality. They take the product’s specifications and turn them into a mold that shapes the final part. They choose the right materials, configure cooling systems, and ensure that the mold has precise dimensions. Their goal is to make a mold that reduces waste and maximizes the quality of each electronic component produced.
Material Choice and Its Impact on Quality
One of the first steps in mold design is choosing the right material for the mold itself. Some materials are better suited for high precision, while others are more suited for speed or lower-volume production. A Mold Maker must choose the right material that balances durability, ease of use, and cost. The right mold material ensures that the parts come out with tight tolerances and the appropriate surface finish.
Precision and Tolerances in Design
Precision is crucial in Electronic Injection Molding. Components like connectors, microchips, and housings must meet strict tolerances. Even small variations in part size can cause malfunction or failure. The Mold Maker ensures that the mold’s design is accurate down to the micron level. They use advanced tools and technology to create molds with tight tolerances. This results in high-quality electronic components that fit and perform as expected.
Gate Design and Its Effect on Part Quality
The gate is where the molten plastic enters the mold. The design of the gate can affect how well the plastic fills the cavity, impacting the final product. If the gate is too large or too small, it can lead to defects such as voids, poor flow, or uneven cooling. A Mold Maker carefully chooses gate placement and size to ensure optimal filling and to prevent defects.
Runner Design for Consistent Flow
The runner system in a mold channels the plastic into the cavities. Proper runner design is essential for consistent material flow. If the runner system is poorly designed, it can cause uneven filling or increased pressure on certain areas of the mold. This can lead to warping or misaligned parts. A well-designed runner system ensures that the plastic flows evenly, helping to reduce defects and maintain consistent part quality.
Cooling System Design
Cooling is a critical aspect of Electronic Injection Molding. Uneven cooling can cause warping or shrinkage, leading to parts that don’t meet specifications. The Mold Maker designs a cooling system that ensures the plastic cools evenly throughout the mold. This is done by strategically placing cooling channels and using temperature control systems to regulate the cooling rate. Efficient cooling ensures that parts maintain their shape and dimensional accuracy.
Parting Line and Flash Control
The parting line is where the two halves of the mold meet. If this line is not carefully designed, it can result in excess plastic, known as flash, around the edges of the molded part. Flash is an unwanted defect that requires additional cleaning or trimming. A skilled Mold Maker ensures that the parting line is as precise as possible. This minimizes flash and ensures clean, defect-free parts every time.
Venting for Proper Airflow
Venting is an important factor in mold design. During the injection molding process, air must be able to escape from the mold as the plastic flows in. If air is trapped inside, it can cause defects like bubbles or uneven surfaces. The Mold Maker designs small vents in the mold to allow air to escape without letting the molten plastic leak out. Proper venting ensures that parts are free of air pockets and that they maintain their integrity.
Mold Maintenance and Durability
The design of the mold also affects its durability and ease of maintenance. Molds used for Electronic Injection Molding are subjected to high pressures and temperatures, which can wear them down over time. A well-designed mold is easier to maintain, reducing downtime and ensuring consistent part quality. The Mold Maker ensures that parts of the mold can be easily replaced or repaired as needed. This helps extend the life of the mold and maintain the quality of production.
Dimensional Stability and Quality Control
Electronic Injection Molding requires tight control over the dimensional stability of parts. Even minor changes in mold temperature or pressure can affect part size. The Mold Maker uses advanced technology to monitor and control these factors. They ensure that every part remains within the desired tolerance range. This is especially important in the production of electronic components, where small variations can cause performance issues.
Troubleshooting Design Issues
If issues arise during production, the Mold Maker can identify design flaws that may be causing defects. This can include issues with cooling, venting, or parting lines. The Mold Maker analyzes the problem and adjusts the mold design to resolve it. This proactive approach helps to prevent further defects and ensures that part quality is maintained.
Prototyping and Testing the Mold Design
Before the mold is used in full-scale production, prototypes are made and tested. These prototypes help the Mold Maker check for issues in the design. They can test for fit, functionality, and overall quality. If any issues are identified, the mold is adjusted before production begins. This testing process ensures that the final mold produces high-quality parts without defects.
The design of the mold plays a critical role in the quality of Electronic Injection Molding parts. From choosing materials to controlling cooling and ensuring dimensional accuracy, every step in the mold design process affects the final product. A skilled Mold Maker ensures that the mold is designed for precision, durability, and efficiency. Their expertise ensures that the molded electronic components meet strict quality standards and perform as required.
By focusing on every detail in the mold design, manufacturers can produce high-quality electronic components that meet the demanding standards of the industry. Whether it’s reducing defects, improving part fit, or increasing production efficiency, the mold design is essential to the success of Electronic Injection Molding.