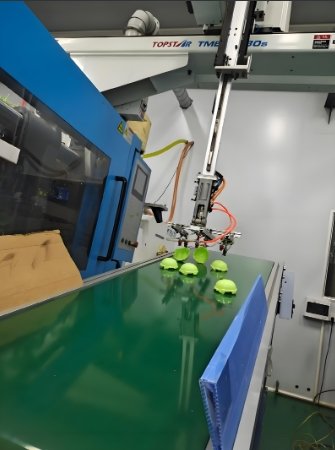
Electronic Injection Molding is key to making strong and precise electronic parts. But flash is a big problem. Flash is the extra plastic that leaks out of the mold. It forms thin fins on the part’s edges. Flash looks bad. It also affects part size and function.
Let’s learn how to stop it. A smart Mold Maker knows how.
1. What Is Flash?
Flash is a molding defect. It happens when plastic leaks out of the mold cavity. It cools and sticks to the part’s edge. Flash often forms near the parting line. It also appears around ejector pins or vents.
2. Why Is Flash Bad?
Flash causes many issues. It makes parts look bad. It makes them hard to fit or use. Flash also needs trimming. That adds time and cost.
In Electronic Injection Molding, flash can block connectors or damage circuits. So, it must be avoided.
3. Poor Mold Fit Causes Flash
Flash often means the mold halves don’t fit well. Even a small gap lets plastic leak out.
A skilled Mold Maker checks and fixes mold fit. They make sure both sides align tightly.
4. Worn Parting Lines
The parting line is where the mold opens and closes. Over time, it can wear down. That makes a gap.
If the parting line is worn, flash will appear. A smart Mold Maker inspects and repairs these lines often.
5. Wrong Clamp Pressure
Too little clamp pressure can cause flash. The mold may not stay fully closed.
During Electronic Injection Molding, the machine must use the right force. A trained team checks and adjusts it as needed.
6. Excess Injection Pressure
Too much injection pressure is risky. It forces plastic into tiny gaps.
If the pressure is too high, flash will form. The Mold Maker adjusts the pressure to match the mold design.
7. Mold Damage Can Cause Flash
Small dents or scratches on mold surfaces lead to flash.
The Mold Maker checks for damage before every run. They polish and repair the mold when needed.
8. Wrong Venting
Vents let air escape from the mold. But if vents are too big, plastic leaks out. If too small, air gets trapped.
Both problems can cause flash. A good Mold Maker makes vents the right size and shape.
9. Poor Mold Design
Some molds are just not built right. Weak designs lead to gaps and leaks.
A skilled Mold Maker designs for high precision. They make sure the mold can hold pressure without leaking.
10. Low-Quality Steel or Materials
Cheap mold materials wear out fast. They don’t hold tight tolerances.
In Electronic Injection Molding, only high-grade steel should be used. A pro Mold Maker picks the best material for long life.
11. Machine Misalignment
If the molding machine is out of line, the mold may not close flat. That causes flash.
The Mold Maker and operator align the machine properly. Regular checks keep things in line.
12. Ejector Pin Flash
Flash can also appear around ejector pins. This happens if the pins are worn or not sealed right.
A smart Mold Maker maintains pins often. They use tight-tolerance fittings to avoid leaks.
13. Resin Type Affects Flash
Some resins flow too easily. They leak into tiny gaps.
The Mold Maker chooses the right resin for the part. They also adjust the mold to match the resin flow.
14. Mold Temperature Is Important
If the mold is too hot, the resin may flow too freely. If it’s too cold, it won’t seal gaps.
In Electronic Injection Molding, a balanced mold temperature helps stop flash.
15. Gate Location Affects Flow
Where the resin enters the mold matters. Poor gate placement can cause uneven flow.
Uneven flow leads to pressure spikes and flash. A skilled Mold Maker places gates wisely.
16. Mold Deflection Under Pressure
If the mold is not strong enough, it may bend slightly under high pressure.
Even tiny bending causes gaps. A strong Mold Maker designs the mold to resist this.
17. Injection Speed Matters
Too fast, and the plastic forces its way into gaps. Too slow, and it may not fill the mold right.
Speed must be set just right. The Mold Maker works with the machine team to find the perfect speed.
18. Cleaning the Mold Often
Dirt or leftover plastic can stop the mold from closing fully. This leads to flash.
Cleaning the mold before every run helps. It’s a job the Mold Maker takes seriously.
19. Checking for Flash During Production
Sometimes flash starts partway through the run. So, checking parts during the job is key.
In Electronic Injection Molding, regular checks help catch flash early.
20. Trim Tools for Removing Flash
Even with care, some flash may appear. Trimming tools cut off flash quickly.
A skilled Mold Maker also designs trim tools to match the part perfectly.
21. Replacing Worn Mold Parts
Mold parts wear out over time. Core pins, bushings, and plates can all change shape.
The Mold Maker tracks part life. They replace worn parts before they cause flash.
22. Digital Monitoring Systems
Modern machines use sensors to track pressure, speed, and temperature. These help detect flash causes in real time.
Smart Electronic Injection Molding shops use this data to prevent flash early.
23. Training the Team
A trained team spots problems early. They know what flash looks like and what causes it.
The Mold Maker often trains machine operators and QC staff to catch issues fast.
Flash is a common problem in Electronic Injection Molding. But it can be fixed. With the right steps, flash can be stopped before it starts.
A skilled Mold Maker is the key. They design strong molds, use the best materials, and keep machines in top shape. They know how to balance pressure, speed, and temperature.
If you want clean, perfect parts with no flash, work with an expert Mold Maker. It saves time, cuts waste, and keeps your electronics working great.