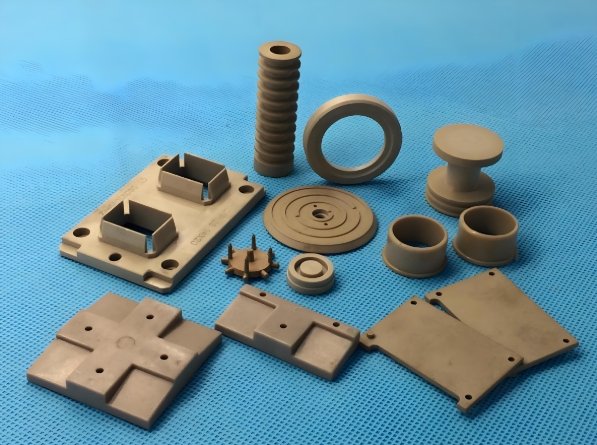
Cost efficiency is crucial in medical injection molding. Manufacturers must balance quality, compliance, and production costs. Mold makers use smart strategies to lower expenses while maintaining precision and safety. This article explores cost-saving techniques in medical molding.
Why Cost Reduction Matters in Medical Injection Molding
1. High Material Costs
Medical-grade plastics are expensive. Reducing waste helps lower costs.
2. Strict Regulatory Compliance
Meeting FDA and ISO standards increases expenses. Efficient processes minimize costs.
3. Energy-Intensive Production
Injection molding machines consume significant power. Energy-efficient solutions save money.
4. Labor and Maintenance Expenses
Automating processes reduces labor costs and machine downtime.
Key Strategies to Reduce Costs in Medical Injection Molding
1. Optimize Material Usage
- Use thin-wall molding to reduce material consumption.
- Select high-performance polymers that require less resin.
- Recycle scrap material whenever possible.
2. Choose Cost-Effective Medical-Grade Plastics
- Compare different FDA-approved plastics.
- Use recyclable thermoplastics to reduce waste.
- Source materials from reliable, cost-efficient suppliers.
3. Implement Advanced Mold Design
- Mold makers design multi-cavity molds to produce more parts per cycle.
- Use hot runner systems to reduce material waste.
- Optimize mold cooling to prevent defects and rework.
4. Automate the Production Process
- Robotic systems handle part removal and inspection.
- Automated conveyors reduce manual labor needs.
- AI-powered quality control minimizes defective parts.
5. Improve Energy Efficiency
- Use servo-driven electric injection molding machines.
- Optimize cooling systems to lower power usage.
- Implement smart scheduling to reduce machine idle time.
Reducing Material Costs in Medical Injection Molding
1. Use Recycled Medical-Grade Plastics
- FDA-approved recycled resins lower costs.
- Reduces environmental impact while maintaining compliance.
2. Minimize Waste Through Process Optimization
- Scientific molding techniques prevent material loss.
- AI monitors material flow to avoid overuse.
3. Leverage Hybrid and Alternative Materials
- Use glass-filled or fiber-reinforced plastics to improve strength.
- Reduce part thickness without compromising durability.
How Mold Makers Reduce Costs
1. Design Molds for Longevity
- Use hardened steel molds to increase lifespan.
- Apply coatings to reduce wear and tear.
2. Implement Predictive Mold Maintenance
- IoT sensors detect mold wear in real time.
- Prevents breakdowns and expensive repairs.
3. Utilize Modular Mold Systems
- Interchangeable mold inserts reduce tooling costs.
- Allows for quick modifications without creating new molds.
4. Optimize Mold Cooling and Ejection
- Conformal cooling channels improve heat dissipation.
- Faster cooling reduces cycle times and increases output.
Reducing Labor Costs in Medical Injection Molding
1. Increase Automation
- Cobots (collaborative robots) assist human operators.
- Fully automated systems reduce manual labor.
2. Train Employees for Efficiency
- Skilled workers prevent errors and rework.
- Proper training improves productivity and machine handling.
3. Implement Real-Time Production Monitoring
- IoT-connected machines provide instant performance updates.
- AI detects inefficiencies and suggests optimizations.
Improving Energy Efficiency to Lower Costs
1. Use Energy-Efficient Machines
- Electric injection molding machines consume 30% less energy.
- Hybrid systems balance speed and energy use.
2. Optimize Cycle Times
- AI reduces unnecessary machine operations.
- Faster cooling and ejection reduce power consumption.
3. Implement Smart Factory Solutions
- Automated lighting and climate control reduce utility costs.
- IoT-enabled systems track and optimize energy use.
Reducing Downtime and Maintenance Costs
1. Schedule Preventive Maintenance
- Regular mold inspections prevent unexpected failures.
- AI predicts when maintenance is needed.
2. Use High-Quality Mold Components
- Precision-engineered molds last longer.
- Reduces frequent replacements and downtime.
3. Implement Remote Machine Monitoring
- IoT alerts operators to potential failures.
- Real-time diagnostics reduce costly shutdowns.
Latest Innovations in Cost Reduction for Medical Injection Molding
1. AI-Powered Process Optimization
- AI adjusts machine settings to reduce material waste.
- Predicts ideal molding conditions for energy efficiency.
2. 3D Printing for Mold Prototyping
- Cuts mold development costs by up to 50%.
- Speeds up design testing and reduces errors.
3. Blockchain for Supply Chain Efficiency
- Tracks raw materials for cost-effective sourcing.
- Improves transparency in procurement and pricing.
4. Advanced Robotics for Material Handling
- AI-powered robots handle material feeding and mixing.
- Reduces manual errors and improves consistency.
5. Digital Twin Technology for Process Simulation
- Virtual modeling prevents defects before production.
- Reduces trial-and-error costs in mold testing.
Future Trends in Cost Reduction for Medical Injection Molding
1. Fully Automated Smart Factories
- AI-driven facilities will operate with minimal human intervention.
- Reduces long-term labor and error-related costs.
2. Sustainable Manufacturing Solutions
- Biodegradable plastics will lower disposal costs.
- Renewable energy will power more medical molding plants.
3. On-Demand Manufacturing with 3D-Printed Molds
- Faster mold production at a lower cost.
- Reduces reliance on expensive traditional tooling.
4. Cloud-Based Manufacturing Analytics
- AI will analyze data to find cost-saving opportunities.
- Machine learning will optimize energy and material use.
5. Customizable Mold Designs for Multi-Use Applications
- Modular molds will allow quick production changes.
- Reduces the need for new mold investments.
Cost reduction in medical injection molding requires smart strategies. Mold makers optimize materials, automation, and energy use to cut expenses. AI, IoT, and predictive maintenance further enhance efficiency. By adopting these methods, manufacturers can produce high-quality medical devices at a lower cost.