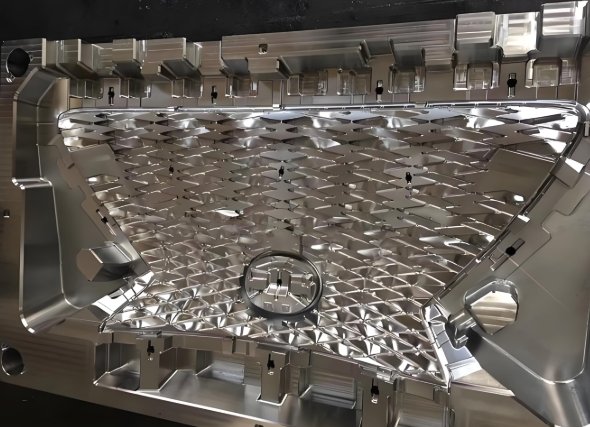
Lighting plays a critical role in vehicle safety and design. Automotive Injection Molds are essential in manufacturing high-quality lighting components for vehicles. These molds allow for precise, durable, and cost-effective production of various automotive lighting parts. A skilled Mold Maker creates these parts to meet strict automotive standards.
The Importance of Lighting in Automotive Design
1. Safety and Visibility
Automotive lighting is essential for safe driving. Headlights, taillights, and indicators ensure that a vehicle is visible to others. Well-designed lighting also improves driver visibility, especially at night or in poor weather conditions.
2. Aesthetic Appeal
Beyond functionality, automotive lighting enhances the vehicle’s look. Modern car designs use intricate light shapes and dynamic lighting patterns to give vehicles a unique style.
The Role of Automotive Injection Molds in Lighting Production
1. Precision and Efficiency
Automotive Injection Molds ensure precise shapes for each lighting component. Mold Makers use advanced techniques to produce complex geometries that would be difficult to achieve with traditional methods. Injection molding is fast and cost-efficient, making it ideal for large-scale production.
2. Durable Materials
Lighting components must be durable and resistant to harsh conditions. Automotive Injection Molds can be created with high-strength materials that withstand UV radiation, temperature changes, and physical stress.
Components of Automotive Lighting Made with Injection Molds
1. Headlights
Headlights are one of the most critical lighting components in vehicles. Automotive Injection Molds are used to create the intricate shapes of headlight lenses and housings. Mold Makers ensure that the lenses are clear, durable, and able to direct light efficiently.
2. Taillights
Taillights, including brake lights and turn signals, are another key component of automotive lighting. Injection molding is used to create these parts in large volumes. The ability to form complex shapes allows for creative designs, improving both visibility and style.
3. Indicators and Markers
Small but essential, indicators and marker lights help with signaling to other drivers. Automotive Injection Molds ensure these components are precisely molded for a perfect fit and clear light output.
Materials Used in Automotive Injection Molds for Lighting
1. Polycarbonate
Polycarbonate is a popular material for automotive lighting. It’s strong, impact-resistant, and has excellent light transmission properties. It’s often used in headlight lenses and covers.
2. Acrylic
Acrylic is another material used for lighting parts. It’s clear, has high impact resistance, and is cost-effective. Acrylic is commonly used in taillights and turn signals.
3. Custom Plastics
Specialized plastics are used to enhance performance. These materials offer additional properties like UV resistance, which is crucial for outdoor components like headlights and taillights that are exposed to sunlight and weather conditions.
The Advantages of Automotive Injection Molds in Lighting
1. Customization
One of the biggest benefits of Automotive Injection Molds is the ability to customize lighting components. Complex shapes, different finishes, and colors can be achieved through molding, giving manufacturers more freedom in design.
2. Consistency and Quality
Injection molding ensures consistent, high-quality parts. Each lighting component produced will have the same shape, size, and finish. This is important for meeting industry standards and consumer expectations.
3. Cost-Effectiveness
Injection molding is highly cost-effective for large-scale production. Once a mold is created, manufacturers can produce thousands of identical parts quickly and at a low cost, reducing the overall cost of automotive lighting components.
The Role of the Mold Maker in Automotive Lighting
1. Design and Prototyping
A skilled Mold Maker works closely with automotive designers to create molds that meet the specific requirements of lighting components. They help refine designs, ensuring that the parts fit correctly and function as intended.
2. Material Selection
Choosing the right material is crucial for automotive lighting. A Mold Maker selects materials that offer the necessary strength, durability, and transparency for the parts.
3. Tooling and Production
Once the design is finalized, the Mold Maker builds the injection mold tool. This tool is used to produce high-quality lighting parts with precise detail. The mold must be durable and capable of handling high temperatures and pressures during the molding process.
Innovations in Automotive Injection Molds for Lighting
1. LED Lighting Integration
As LED lighting becomes more common in modern vehicles, Automotive Injection Molds are adapting to integrate LED technology. These lights require precise housings and lenses, which are efficiently made with injection molds.
2. Smart Lighting Systems
With the rise of smart vehicles, lighting systems are becoming more sophisticated. Injection molding is used to create components for adaptive headlights, dynamic turn signals, and other intelligent lighting systems.
3. Eco-Friendly Materials
In response to environmental concerns, manufacturers are increasingly turning to eco-friendly materials. Automotive Injection Molds can be made using recycled plastics and biodegradable materials, helping reduce the carbon footprint of the automotive industry.
Challenges in Automotive Lighting Production
1. High-Performance Requirements
Automotive lighting components must meet strict performance standards. These parts must be able to handle extreme temperatures, UV radiation, and physical impact. Achieving this level of durability requires precision in both mold design and material selection.
2. Complex Shapes
Modern automotive lighting features complex shapes that require advanced molding techniques. For example, headlight lenses often have curved, multi-faceted designs. These shapes require molds with precise details and accuracy.
Future Trends in Automotive Lighting Molds
1. Customization and Personalization
The future of automotive lighting will likely see increased customization. Drivers may be able to personalize their vehicle’s lighting system, from the color of the headlights to the design of the taillights. Injection molding will play a key role in making these customized parts affordable and easy to produce.
2. Sustainability in Production
As sustainability becomes more important, the use of eco-friendly materials in automotive lighting production will increase. Molds designed for these materials will be essential for reducing the environmental impact of automotive manufacturing.
3. Integration with Vehicle Design
In the future, lighting components will likely be more integrated into the overall design of the vehicle. Mold Makers will work closely with automotive designers to ensure that lighting components enhance the aesthetic appeal of vehicles while maintaining functionality.
Automotive Injection Molds are integral to the production of high-quality lighting components. They offer precision, cost-effectiveness, and durability, making them ideal for mass-producing essential automotive parts like headlights, taillights, and turn signals. Mold Makers play a vital role in designing and creating molds that meet the strict standards required for automotive lighting. As lighting technology continues to evolve, the role of Automotive Injection Molds will continue to grow, ensuring that vehicles are safer, more stylish, and more energy-efficient.