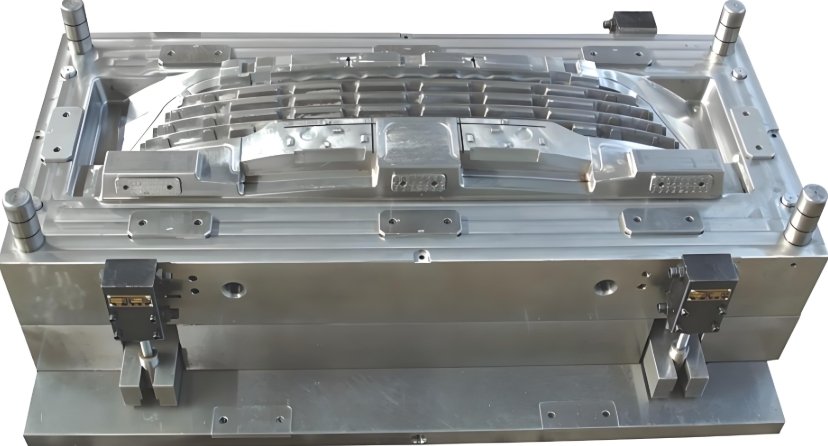
Bumpers and grilles are crucial parts of every vehicle. They need to be strong, durable, and visually appealing. Automotive Injection Molds are essential for producing these components. A skilled Mold Maker ensures each mold meets quality and efficiency standards. This article explores the process, benefits, and future of injection molding for bumpers and grilles.
Why Use Automotive Injection Molds?
1. Precision
Injection molding creates precise and consistent shapes. This ensures bumpers and grilles fit perfectly on vehicles.
2. Durability
The molds create parts that withstand impact, weather, and wear. This durability makes injection molding ideal for automotive needs.
3. Customization
Mold Makers design molds to match specific vehicle designs. This allows manufacturers to meet diverse style requirements.
The Role of a Mold Maker
1. Design Expertise
A Mold Maker creates detailed designs for molds. They ensure the mold produces high-quality parts.
2. Material Selection
Mold Makers choose materials that enhance the mold’s durability and performance. For bumpers and grilles, steel molds are common.
3. Efficiency
Skilled Mold Makers optimize the design to reduce production time. This saves costs and speeds up manufacturing.
Materials Used in Automotive Injection Molds
1. ABS Plastic
ABS plastic is lightweight and strong. It is often used for bumpers.
2. Polycarbonate
Polycarbonate is durable and impact-resistant. It’s ideal for grilles.
3. Polypropylene
Polypropylene is cost-effective and flexible. It works well for large, complex parts like bumpers.
Injection Molding Process for Bumpers
1. Designing the Mold
A Mold Maker starts with the design. They ensure it matches the bumper’s size and shape.
2. Material Selection
The right plastic material is chosen based on the bumper’s requirements.
3. Injection and Cooling
Molten plastic is injected into the mold. The mold cools and solidifies the plastic into the bumper shape.
4. Trimming and Finishing
Excess material is removed. The bumper is polished for a smooth finish.
Injection Molding Process for Grilles
1. Mold Design
Grilles require intricate designs. A Mold Maker ensures the mold captures every detail.
2. Material Selection
Polycarbonate or ABS plastic is often used for grilles.
3. Injection and Cooling
The plastic is injected into the mold and cooled. This forms the precise grille structure.
4. Post-Molding Steps
The grille undergoes additional finishing steps for quality assurance.
Benefits of Injection Molding for Bumpers and Grilles
1. Cost-Effectiveness
Once the mold is created, production costs drop. This is ideal for large volumes.
2. Consistency
Every part is identical, ensuring uniformity in production.
3. Durability
Injection-molded parts last longer and withstand harsh conditions.
4. Design Flexibility
The process allows for complex shapes and designs.
Challenges in Automotive Injection Molds
1. Initial Mold Costs
Creating the mold can be expensive. However, it pays off in the long run.
2. Material Selection
Choosing the wrong material can affect the part’s quality. A skilled Mold Maker avoids this issue.
3. Maintenance
Molds need regular maintenance to ensure consistent quality.
The Future of Automotive Injection Molds
1. Lightweight Materials
As vehicles become lighter, molds must adapt. Lightweight plastics are gaining popularity.
2. Sustainability
Eco-friendly materials and processes are the future of injection molding.
3. Advanced Technologies
3D printing and automation are making mold production faster and more precise.
Automotive Injection Molds play a vital role in creating bumpers and grilles. A skilled Mold Maker ensures the molds are durable, efficient, and cost-effective. With advancements in technology, the injection molding process continues to evolve. This ensures better quality, reduced costs, and more sustainable production. For manufacturers, injection molding remains the best choice for producing high-quality automotive components.