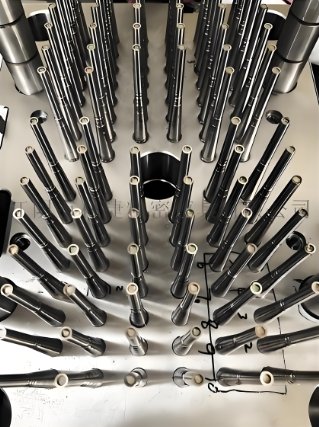
Medical equipment must meet strict quality and safety standards. Medical injection molding is a key process in manufacturing these devices. It ensures accuracy, sterility, and cost efficiency. Mold makers design molds that produce reliable and high-quality parts.
Why Medical Injection Molding is Important
1. Precision and Accuracy
Medical equipment requires exact dimensions. Medical injection molding creates parts with tight tolerances. This ensures they fit and function properly.
2. High Production Speed
Injection molding allows for mass production. This speeds up the manufacturing process and reduces costs.
3. Biocompatible Materials
Medical devices need safe materials. Injection molding uses biocompatible plastics that are non-toxic and durable.
4. Sterility and Clean Production
Medical components must be free from contamination. Injection molding takes place in controlled environments to ensure sterility.
Applications of Medical Injection Molding
1. Surgical Instruments
Scalpels, forceps, and clamps are made using medical injection molding. These instruments require high precision and durability.
2. Diagnostic Equipment
Medical devices like test kits and lab tools rely on injection molding. Accuracy in these parts ensures correct test results.
3. Implantable Devices
Pacemaker casings and orthopedic implants use injection-molded components. They must meet strict safety and biocompatibility standards.
4. Drug Delivery Devices
Inhalers, insulin pens, and syringes are essential for patient care. Injection molding ensures they work properly and safely.
5. Medical Packaging
Sterile containers, pill dispensers, and IV bags are made using injection molding. These products must be safe and durable.
6. Prosthetics and Orthotics
Custom prosthetics and orthopedic braces require precise molding. Injection molding creates lightweight, durable, and comfortable medical aids.
7. Catheters and Tubing
Flexible plastic tubing is essential in many medical procedures. Injection molding ensures the tubes are smooth, sterile, and safe.
Benefits of Medical Injection Molding
1. Cost-Effective Production
Injection molding reduces material waste. It also lowers labor costs since machines handle most of the work.
2. Consistent Quality
Each part comes out the same. This ensures all medical devices meet strict industry standards.
3. Design Flexibility
Complex shapes and detailed designs are possible. This helps create innovative medical equipment.
4. Strong and Lightweight Parts
Injection molding produces durable yet lightweight components. This improves the usability of medical equipment.
5. High Volume Production
Large quantities of parts can be made quickly. This keeps up with high medical demands.
6. Minimal Material Waste
Excess plastic can be reused. This makes injection molding an efficient process.
The Role of Mold Makers in Medical Equipment Production
1. Designing the Mold
Mold makers create molds based on the product’s specifications. The mold must be perfect to ensure high precision.
2. Choosing the Right Material
Material selection is crucial. Mold makers select materials that are biocompatible, durable, and suitable for sterilization.
3. Prototyping and Testing
Before mass production, prototypes are made. This helps in testing and making improvements.
4. Maintaining Mold Quality
Regular mold maintenance ensures continuous high-quality production. Mold makers check and repair molds as needed.
Challenges in Medical Injection Molding
1. Strict Regulatory Requirements
Medical devices must meet FDA and ISO standards. Manufacturers must ensure compliance.
2. Material Compatibility
Not all plastics are suitable for medical use. The right materials must be chosen to avoid health risks.
3. Avoiding Contamination
Production takes place in clean rooms to maintain sterility. Strict hygiene protocols are followed.
4. High Initial Costs
Mold creation requires an initial investment. However, long-term production saves costs.
Advanced Technologies in Medical Injection Molding
1. Micro Molding
This process makes very small parts. It is used for components in hearing aids and surgical tools.
2. Overmolding
Overmolding combines two materials in one part. It is useful for grips on medical devices.
3. Liquid Silicone Rubber (LSR) Molding
LSR molding creates flexible, heat-resistant parts. It is ideal for catheters and seals.
4. Automation in Injection Molding
Robots and automated systems improve precision and speed. This reduces human error and increases efficiency.
The Future of Medical Injection Molding
1. Smart Medical Devices
Advanced technology will lead to smart implants and drug delivery systems. Injection molding will help in their production.
2. Sustainable Medical Plastics
Eco-friendly materials will reduce environmental impact. Recyclable medical plastics will become more common.
3. Improved Biocompatible Materials
New materials will enhance the safety and durability of medical devices.
4. 3D Printing and Injection Molding Integration
Combining these technologies will allow for rapid prototyping and faster production.
Medical injection molding plays a key role in healthcare. It ensures the production of high-quality, safe, and precise medical equipment. Mold makers design molds that meet strict standards. As technology advances, injection molding will continue to improve medical manufacturing, making healthcare more efficient and accessible.