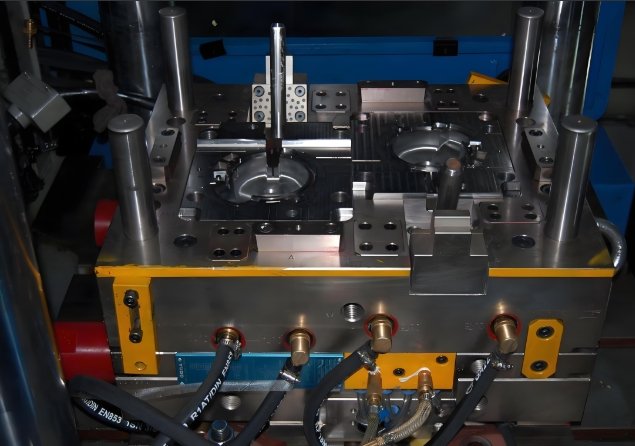
Cost management is vital in manufacturing. An injection mould company helps businesses meet their budget goals. This article explores cost breakdowns and savings in injection molding. Understanding expenses ensures better decisions.
Initial Costs: Mold Design
Creating injection molds starts with design. This step requires precision. A mold maker analyzes product requirements. They use advanced software to create detailed designs.
Design costs depend on complexity. A simple mold costs less. Complex shapes or multiple cavities increase the price. However, a well-designed mold reduces errors. This saves money during production.
Material Costs for Injection Molds
The materials used in injection molds affect costs. Steel molds are durable but expensive. Aluminum molds are cheaper but wear out faster.
Material choice depends on production volume. High-volume projects need durable molds. For low-volume runs, aluminum is more cost-effective. An experienced mold maker selects the right material to balance cost and durability.
Production Costs in Injection Molding
Production costs vary with the part size and material. Plastics like polypropylene and ABS are affordable. Specialized plastics like PEEK are costly.
Cycle time also impacts costs. Shorter cycles save energy. However, faster production may require advanced machinery. An injection mould company optimizes production speed to save money.
Maintenance and Repair Costs
Over time, injection molds need maintenance. Repairs prevent defects and downtime. Neglecting maintenance increases long-term costs.
A skilled mold maker inspects molds regularly. They address wear and tear promptly. Preventive care extends mold life and lowers repair expenses.
Labor Costs
Labor is another expense. Skilled workers operate machines and inspect parts. Automation can reduce labor costs. However, automated systems require upfront investment.
An injection mould company balances human expertise with automation. This ensures efficiency while managing costs.
Shipping and Logistics
Transporting materials and products adds to expenses. Lightweight plastics reduce shipping costs. However, bulky molds require careful handling.
An injection mould company works with reliable shipping partners. This ensures timely delivery and cost efficiency.
Savings Opportunities in Injection Molding
Now let’s explore how to save. An injection mould company offers several opportunities.
Standardization of Mold Design
Standard molds reduce costs. A mold maker uses modular designs to save on materials. These molds work across multiple projects. This eliminates the need for custom molds every time.
Efficient Material Use
Reducing waste lowers material costs. Injection molding machines optimize plastic usage. Advanced techniques like hot-runner systems further minimize waste.
Recycled plastics also offer savings. An injection mould company incorporates sustainable materials to reduce costs and environmental impact.
Batch Production Savings
Producing in large batches cuts costs. High-volume orders spread fixed costs over more units. This reduces the per-unit price.
An injection mould company plans production schedules carefully. They maximize machine efficiency and minimize downtime.
Energy Efficiency
Modern machines consume less energy. Energy-efficient injection molding reduces electricity bills. An injection mould company invests in advanced equipment to save energy.
Outsourcing to Injection Mould Companies
Outsourcing saves businesses money. An injection mould company handles design, production, and quality control. This eliminates the need for in-house teams and equipment.
Companies benefit from the expertise of skilled mold makers. They also avoid high setup costs. Outsourcing provides flexibility without long-term commitments.
Reducing Maintenance Costs
Preventive maintenance saves money. Regular inspections catch issues early. This avoids costly downtime.
A trusted injection mould company offers maintenance services. Their expertise keeps molds in top condition. This ensures smooth production and fewer repairs.
Streamlining Supply Chains
A reliable supply chain saves time and money. An injection mould company works with trusted material suppliers. This reduces delays and ensures consistent quality.
Simplifying logistics further cuts costs. Companies that streamline processes avoid unnecessary expenses.
Negotiating Long-Term Contracts
Long-term contracts with an injection mould company offer savings. Bulk discounts and fixed rates reduce costs.
This partnership ensures consistent production. It also fosters collaboration for innovative solutions.
Investing in Quality
Quality saves money in the long run. High-quality injection molds last longer. They produce flawless parts with minimal waste.
An experienced mold maker ensures top-notch quality. Investing in durable molds prevents frequent replacements.
Future Trends in Cost Management
The future of injection molding focuses on cost efficiency. Automation and AI reduce labor costs. Sustainable materials lower expenses and benefit the planet.
An injection mould company stays ahead with technology. Their expertise ensures continued savings for clients.
Managing costs is crucial in manufacturing. An injection mould company offers many savings opportunities. From efficient designs to advanced machinery, their services optimize budgets.
Skilled mold makers play a vital role in this process. Their expertise ensures precision and durability. By partnering with an injection mould company, businesses achieve cost-effective production.
Innovation, quality, and savings go hand in hand. Choose an experienced injection mould company for your next project. They’ll help you cut costs while delivering excellent results.