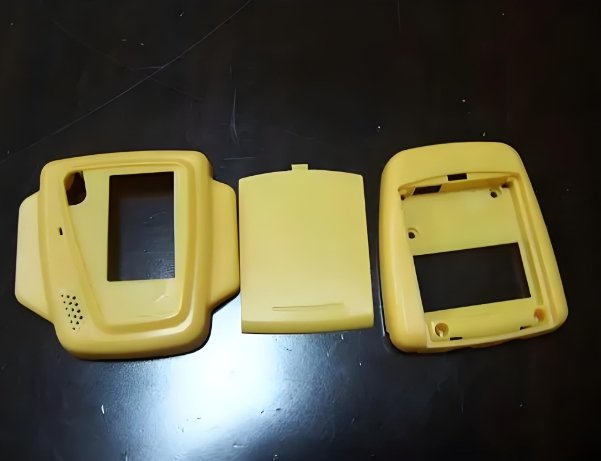
Housing injection molding plays a vital role in the creation of plastic enclosures for electronic devices, appliances, tools, and more. These housings protect inner components and give products their final shape. As industries evolve, new demands are placed on plastic parts. In response, mold makers and manufacturers are pushing boundaries to meet these needs.
This article explores the most important trends shaping housing injection molding today. Whether you’re a product designer or a mold maker, staying updated with the latest technology, materials, and methods can make all the difference in performance, cost, and speed.
1. High-Performance Materials
The demand for stronger, lighter, and more durable housings continues to grow. Modern housing injection molding no longer relies solely on basic ABS or polycarbonate. Now, many mold makers are working with advanced polymers like:
- Glass-filled nylon
- Flame-retardant PC/ABS blends
- UV-resistant polypropylene
- Conductive plastics for EMI shielding
These materials extend the life of housings and help meet global safety standards. A knowledgeable mold maker will recommend the best plastic based on temperature, impact resistance, or environmental exposure.
2. Miniaturization of Components
Products are getting smaller and more complex. Think of smartphones, IoT devices, or smart home sensors. All of these require tight-tolerance housings with precise snap fits and fine details.
This shift has forced housing injection molding to evolve. Tools must now support:
- Micro features
- Thin walls
- Compact geometries
A skilled mold maker must use advanced machining to build such high-precision molds. Even slight errors in the tooling can cause short shots or warping. That’s why expertise in miniature mold components is a growing requirement.
3. Overmolding and Insert Molding
Modern plastic housings often need multiple materials or embedded hardware. This is where overmolding and insert molding are booming.
- Overmolding allows a soft rubber grip to be molded over a hard plastic base.
- Insert molding places metal parts, such as threads or connectors, inside the housing during the molding process.
These techniques improve function and reduce assembly. However, they demand more from the mold maker, who must design the tool to manage multiple steps, complex cooling, and precision part placement.
4. Sustainability in Mold Design and Production
Today’s brands care more about environmental responsibility. That impacts both the materials used and the way parts are made.
Housing injection molding is adapting by:
- Using recycled or bio-based resins
- Reducing material waste with runnerless (hot runner) molds
- Creating lightweight housings with smart design
- Optimizing cooling to save energy
A green approach isn’t just better for the environment. It also saves money and improves brand image. A proactive mold maker will offer options that meet both environmental goals and production needs.
5. Rapid Tooling and Bridge Tooling
Speed is everything in competitive markets. To launch products faster, many companies now ask for rapid or bridge tooling.
- Rapid tooling uses aluminum or softer steels to create low-volume molds quickly.
- Bridge tooling fills the gap between prototype and full production.
This trend in housing injection molding is ideal for testing a design before investing in expensive steel molds. A forward-thinking mold maker will offer these options to help clients move faster with less risk.
6. Advanced Simulation and DFM Software
Before a mold is even cut, new software allows full digital testing of flow, cooling, warpage, and more. This software is changing the game for housing injection molding.
Design for Manufacturing (DFM) tools let mold makers predict:
- Where defects will form
- How plastic will fill complex shapes
- Whether the part will shrink or bend after ejection
The result? Fewer errors, lower costs, and faster mold validation. A modern mold maker uses simulation tools as part of the planning process to ensure first-time-right tooling.
7. Smart Molds and Automation
Smart molds are equipped with sensors that track temperature, pressure, and cycle time in real time. These molds improve consistency and help spot issues before they cause scrap.
Automation is also expanding in housing injection molding, with:
- Robotic part removal
- Automated mold cleaning
- In-line inspection systems
The goal is zero-defect production with fewer labor costs. A progressive mold maker will design molds with automation in mind from the start.
8. Custom Finishes and Textures
Today, housings are not just functional—they also represent brand identity. Textures, gloss levels, and surface finishes matter more than ever.
Trends include:
- Laser-engraved logos in the mold
- Micro-texturing for grip or style
- Soft-touch finishes from TPE overmolding
An expert mold maker works with surface finishing teams to deliver not just a part—but a complete, ready-to-market housing that stands out.
9. Supply Chain Localization and Dual Sourcing
Global supply chains are shifting. Many companies are rethinking where their housing injection molding gets done. Some now prefer local or regional mold makers to avoid shipping delays, tariffs, and communication issues.
Others use dual sourcing—having one mold maker in Asia and one closer to home. This balances cost with speed and lowers risk in case of disruptions.
10. Integration with 3D Printing
3D printing is not replacing injection molding—but it is working alongside it. For mold makers, it provides faster prototypes, sample inserts, and even conformal cooling channels inside tools.
For product teams, 3D-printed housings can be tested quickly before moving to full housing injection molding. This speeds up the whole cycle.
The world of housing injection molding is changing fast. From smart molds and sustainable plastics to new tooling methods and design tools, innovation is everywhere.
To stay ahead, choose a mold maker who:
- Understands new materials
- Uses advanced software and automation
- Can deliver fast tooling without cutting quality
- Offers real solutions—not just parts
The best mold makers don’t just build tools. They solve problems, reduce time to market, and help bring better products to life.
Want to explore how these trends apply to your next housing project? Let us know—we’re happy to help.