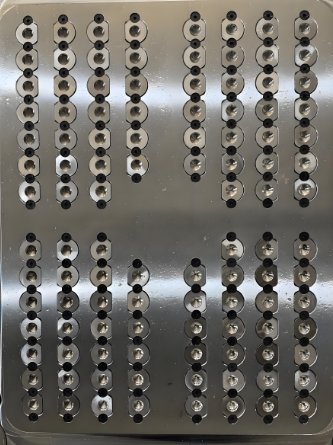
Medical injection molding is crucial in producing high-quality medical devices. To meet strict standards, manufacturers must follow Good Manufacturing Practices (GMP). These guidelines ensure safety, precision, and compliance with regulations. This article explores the best practices in medical injection molding and how mold makers apply GMP to maintain high standards.
What Is GMP in Medical Injection Molding?
1. Definition of GMP
Good Manufacturing Practices (GMP) refer to a set of regulations ensuring that medical devices are consistently produced and controlled. These practices cover every aspect of production, from material selection to final inspection.
2. Why GMP Matters
GMP ensures that medical devices are safe, effective, and reliable. Failure to comply with GMP standards can lead to defects, recalls, and legal issues.
3. Regulatory Bodies
The FDA and ISO 13485 are the primary regulatory authorities for GMP. Manufacturers must adhere to these guidelines to sell medical devices in most markets.
Key GMP Guidelines for Medical Injection Molding
1. Facility Requirements
- Cleanrooms are essential in medical injection molding. They prevent contamination of parts.
- The facility must maintain specific temperature, humidity, and cleanliness levels.
- Separate areas should be used for molding, testing, and assembly.
2. Personnel Training
- Employees must undergo regular training on GMP standards.
- Training includes hygiene, handling materials, and using molding equipment.
- Continuous education ensures that workers understand the latest regulations.
3. Equipment Maintenance
- All equipment must be properly maintained and calibrated.
- Regular checks prevent equipment malfunctions that could compromise quality.
- A mold maker must ensure that molds are regularly serviced to avoid defects.
4. Material Control
- Materials used in medical injection molding must meet biocompatibility standards.
- A strict system for tracking materials ensures that only approved materials are used.
- Materials should be stored in controlled conditions to avoid contamination.
5. Process Control
- Medical injection molding processes must be carefully monitored.
- Parameters such as temperature, pressure, and cycle time should be controlled.
- Any variations from the standard must be documented and addressed immediately.
Best Practices for Medical Injection Molding in Compliance with GMP
1. Detailed Documentation
- All processes, from mold design to final product testing, should be documented.
- Documentation includes material certifications, batch records, and testing results.
- Accurate records ensure traceability and help with audits.
2. Regular Audits
- Internal and external audits ensure that GMP standards are being followed.
- Audits identify areas for improvement and ensure compliance with regulations.
- Mold makers should conduct regular checks on mold designs, processes, and final products.
3. Continuous Improvement
- Continuous improvement is a core principle of GMP.
- Manufacturers must implement systems for regular process reviews.
- Feedback from inspections and audits helps improve production.
4. Product Testing and Validation
- All parts produced by medical injection molding must undergo thorough testing.
- Tests include dimensional checks, strength tests, and biocompatibility assessments.
- The testing results must be documented and reviewed for compliance.
5. Batch Control and Traceability
- Each batch of parts must be traceable from production to final use.
- Batch control ensures that defective products can be recalled if necessary.
- A detailed system for batch identification and traceability is required.
6. Cleanroom Standards
- Medical injection molding must be conducted in a controlled environment.
- Cleanrooms prevent contamination and maintain high standards of hygiene.
- Strict protocols must be followed to ensure the cleanroom remains free from particles.
The Role of the Mold Maker in GMP Compliance
1. Mold Design
- Mold makers must design molds that meet the required standards for medical injection molding.
- Molds must be precise and capable of producing parts within the required tolerances.
- Any mold defects can lead to product defects, affecting safety and quality.
2. Mold Maintenance
- Regular maintenance of molds is essential to ensure proper functioning.
- Proper cleaning and lubrication of molds prevent contamination and wear.
- Mold makers must ensure that molds are inspected and serviced according to GMP guidelines.
3. Quality Control in Molding
- The mold maker plays a key role in maintaining quality throughout the molding process.
- Monitoring and adjusting molding parameters, such as temperature and pressure, is crucial.
- Any deviation from the established process must be immediately corrected.
Challenges in Medical Injection Molding and GMP Compliance
1. Maintaining Strict Cleanliness
- Even small particles of dust can contaminate medical components.
- Keeping a cleanroom environment free from contaminants requires constant vigilance.
2. Material Selection and Availability
- Mold makers must ensure that all materials meet strict FDA and ISO standards.
- Sourcing medical-grade materials can be challenging and time-consuming.
3. Process Consistency
- Maintaining consistent molding parameters is difficult but essential for quality.
- Variations in molding pressure, temperature, or cycle time can affect part quality.
4. Staff Training
- Keeping employees up-to-date with the latest GMP standards is critical.
- A lack of training can lead to errors and a failure to meet compliance standards.
5. Record Keeping and Traceability
- Proper documentation and traceability systems are essential but can be cumbersome.
- Mistakes in documentation can lead to serious compliance issues.
The Future of GMP in Medical Injection Molding
1. Automation and Smart Manufacturing
- Automation will streamline the medical injection molding process, improving precision and reducing human error.
- Smart sensors and AI systems will monitor the process in real time, ensuring compliance with GMP.
2. Advanced Materials
- The development of new, more advanced materials will improve the performance and safety of medical devices.
- Mold makers will need to ensure that new materials meet GMP standards.
3. Improved Cleanroom Technologies
- New cleanroom technologies will make it easier to maintain sterility.
- These innovations will help meet the strict cleanliness requirements for medical devices.
4. Enhanced Training Programs
- Advanced training platforms and virtual reality (VR) simulations will improve staff training.
- These tools will ensure that employees stay up-to-date with the latest GMP standards.
Ensuring compliance with Good Manufacturing Practices (GMP) is critical for medical injection molding. It guarantees that medical devices are safe, effective, and reliable. Mold makers play a key role in ensuring that production meets the highest standards. By following best practices, including proper documentation, process control, and regular audits, manufacturers can maintain quality and comply with regulatory requirements. The future of medical injection molding will see even more advancements in automation, materials, and training, making the process even more efficient and reliable.