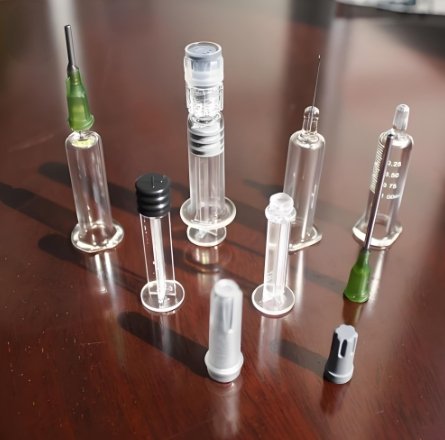
Risk management is essential in medical injection molding. Medical devices must meet strict regulatory standards. Mold makers play a key role in ensuring compliance. Poor risk management can lead to defects, recalls, and legal issues. This article explores the importance of risk management and compliance in medical injection molding.
Why Risk Management Matters in Medical Injection Molding
1. Patient Safety
Defective medical components can cause serious harm. Risk management ensures that each part meets safety standards.
2. Regulatory Compliance
Organizations like the FDA and ISO enforce strict guidelines. Compliance prevents fines, recalls, and legal action.
3. Product Reliability
Medical devices must function correctly every time. Risk management reduces failure rates and increases reliability.
4. Manufacturing Efficiency
Identifying risks early prevents costly errors. Efficient production reduces waste and improves profitability.
Key Regulatory Standards for Medical Injection Molding
1. ISO 13485: Medical Device Quality Management
- Sets quality management standards for medical device manufacturing.
- Ensures that mold makers follow strict documentation and testing protocols.
2. FDA 21 CFR Part 820: Quality System Regulation (QSR)
- Requires manufacturers to establish a quality management system.
- Covers design controls, process validation, and corrective actions.
3. ISO 14971: Medical Device Risk Management
- Provides guidelines for identifying and controlling risks.
- Ensures a systematic approach to risk assessment in medical injection molding.
4. Good Manufacturing Practices (GMP)
- Ensures that medical devices are consistently produced with high quality.
- Focuses on facility cleanliness, equipment maintenance, and employee training.
5. ISO 10993: Biocompatibility Testing
- Ensures that medical-grade plastics are safe for human contact.
- Prevents adverse reactions in patients.
Risk Management Strategies in Medical Injection Molding
1. Hazard Identification
- Identify potential risks in the molding process.
- Common hazards include material contamination, molding defects, and improper sterilization.
2. Failure Mode and Effects Analysis (FMEA)
- Evaluates potential failures in the molding process.
- Assesses the impact of defects on product safety and function.
3. Process Validation
- Ensures that the molding process consistently produces high-quality parts.
- Involves testing molds, measuring product dimensions, and conducting functional tests.
4. Material Selection and Testing
- Use only FDA-approved and ISO-compliant medical-grade plastics.
- Conduct biocompatibility and sterilization tests before production.
5. Mold Design and Maintenance
- Mold makers must design molds with precision.
- Regular maintenance prevents defects and ensures mold longevity.
6. Cleanroom Manufacturing
- Prevents contamination by controlling air quality, humidity, and temperature.
- Meets ISO 14644 cleanroom standards for medical device production.
7. Quality Control and Inspection
- Implement automated inspection systems to detect defects.
- Perform dimensional checks, stress tests, and material analysis.
8. Documentation and Traceability
- Keep detailed records of every production run.
- Ensure full traceability of materials, batches, and test results.
Challenges in Risk Management and Compliance
1. Strict Regulatory Requirements
- Compliance with FDA and ISO standards is complex.
- Frequent regulatory updates require constant monitoring.
2. High Costs of Compliance
- Implementing risk management systems can be expensive.
- Investment in training, equipment, and audits is necessary.
3. Maintaining Consistency in High-Volume Production
- Producing millions of identical parts requires precision.
- Small variations can lead to defects and regulatory violations.
4. Preventing Material Contamination
- Medical-grade plastics must remain sterile.
- Contamination risks increase during storage, handling, and processing.
5. Ensuring Supplier Compliance
- Material suppliers must meet FDA and ISO standards.
- Poor-quality materials can lead to product failure.
Best Practices for Ensuring Compliance in Medical Injection Molding
1. Establish a Strong Quality Management System (QMS)
- Implement ISO 13485-compliant QMS.
- Document every step of the molding process.
2. Conduct Regular Audits and Inspections
- Perform internal and third-party audits.
- Identify non-compliance issues before they become major problems.
3. Train Employees on Regulatory Compliance
- Regular training ensures that all workers understand GMP and FDA requirements.
- Training should cover material handling, cleanroom procedures, and process validation.
4. Use Advanced Testing Methods
- Conduct real-time monitoring of injection molding processes.
- Use AI-powered defect detection for faster quality control.
5. Implement Automated Quality Control Systems
- Optical and laser inspection systems improve accuracy.
- Automated systems reduce human error and improve consistency.
6. Work Closely with Regulatory Experts
- Consult with compliance specialists for the latest FDA and ISO updates.
- Ensure that new molds and materials meet current regulatory standards.
The Role of the Mold Maker in Risk Management and Compliance
1. Designing High-Precision Molds
- Mold makers ensure that medical molds meet strict tolerances.
- Proper design minimizes defects and reduces risk.
2. Selecting the Right Materials
- Mold makers choose materials that are FDA-approved and biocompatible.
- They work with suppliers to guarantee material traceability.
3. Ensuring Mold Longevity and Consistency
- High-quality molds reduce wear and tear.
- Proper mold maintenance prevents production downtime.
4. Supporting Process Validation
- Mold makers help test and refine molding processes.
- They ensure that production runs consistently meet compliance standards.
Future Trends in Risk Management for Medical Injection Molding
1. AI-Powered Compliance Monitoring
- AI will track production in real time.
- Predictive analytics will identify risks before failures occur.
2. 3D Printing for Mold Prototyping
- Rapid prototyping will reduce mold development time.
- It will help refine designs before mass production.
3. Blockchain for Traceability
- Blockchain will improve supply chain transparency.
- It will ensure that all materials meet regulatory standards.
4. Sustainability and Biodegradable Materials
- Future regulations will promote eco-friendly medical plastics.
- Mold makers must adapt to new material requirements.
5. Enhanced Sterilization Technologies
- New sterilization methods will improve product safety.
- UV and plasma sterilization will become more common in cleanrooms.
Risk management and compliance are essential in medical injection molding. Regulatory standards ensure patient safety, product reliability, and manufacturing efficiency. Mold makers play a critical role in designing high-quality molds that meet FDA and ISO requirements. By following best practices, manufacturers can reduce risks, maintain compliance, and produce safe medical devices. As technology advances, risk management will become even more precise and efficient, shaping the future of medical injection molding.