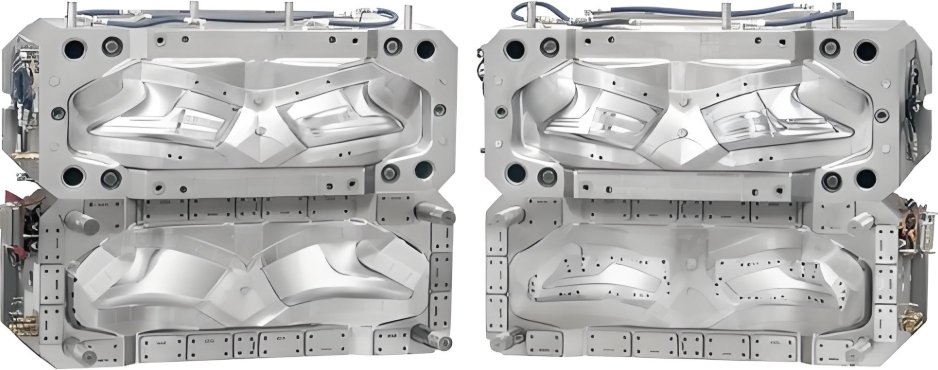
Fuel systems require precision and reliability. Automotive injection molds produce accurate, high-quality components. A skilled mold maker ensures durability and efficiency. These molds help create fuel tanks, pumps, filters, and connectors. Injection molding improves safety, reduces weight, and enhances performance.
Why Injection Molding for Fuel Systems?
1. High Precision Manufacturing
Fuel system components must meet strict standards. Automotive injection molds create precise shapes with minimal errors. A professional mold maker ensures every detail is perfect.
2. Lightweight and Durable Parts
Vehicles need strong but lightweight parts. Injection molding allows the use of advanced plastics. These materials resist fuel corrosion and extreme temperatures. A skilled mold maker selects the best materials for durability.
3. Cost-Effective Mass Production
Injection molding reduces material waste. Automotive injection molds produce large quantities quickly. A mold maker optimizes the process to lower production costs.
4. Complex Designs with High Consistency
Fuel systems require intricate parts. Injection molding allows complex designs with uniform quality. A skilled mold maker ensures precision in every batch.
Key Fuel System Components Made with Injection Molding
1. Fuel Tanks
Fuel tanks must be lightweight, strong, and leak-proof. Automotive injection molds create durable tanks with smooth finishes. A mold maker ensures exact dimensions and strength.
2. Fuel Pumps
Fuel pumps regulate fuel flow. They need precise fittings and durable casings. Injection molding ensures strong and accurate parts. A mold maker guarantees long-lasting components.
3. Fuel Filters
Fuel filters remove impurities. They require fine mesh and high-strength plastic housings. Automotive injection molds create durable, efficient filters. A mold maker ensures perfect sealing and performance.
4. Fuel Lines and Connectors
Fuel lines transport fuel to the engine. Connectors ensure leak-proof fittings. Injection molding provides strong, flexible lines and secure connectors. A mold maker ensures high precision and durability.
5. Vapor Recovery Systems
Vapor recovery prevents fuel evaporation. These systems need airtight components. Automotive injection molds create high-precision parts. A mold maker ensures compliance with emission standards.
Materials for Automotive Fuel System Molding
1. High-Temperature Resistant Plastics
Fuel system components must withstand extreme heat. Materials like POM, PA, and PPS are common. Automotive injection molds shape these materials into durable parts.
2. Fuel-Resistant Polymers
Gasoline and diesel can degrade weak plastics. Special polymers resist fuel corrosion. A skilled mold maker selects the right materials for long-lasting parts.
3. Lightweight Composites
Reducing weight improves fuel efficiency. Automotive injection molds use advanced composites. A mold maker ensures strength without added weight.
Advantages of Injection Molding for Fuel Systems
1. High Precision and Tight Tolerances
Fuel system parts require exact measurements. Automotive injection molds produce accurate, defect-free components. A mold maker guarantees precision.
2. Enhanced Durability
Injection-molded fuel system parts resist wear and tear. They endure extreme conditions. A skilled mold maker ensures longevity.
3. Reduced Production Costs
Injection molding speeds up production. Automotive injection molds lower manufacturing costs. A mold maker optimizes the process for efficiency.
4. Improved Safety and Performance
Fuel system components must be leak-proof and heat-resistant. Injection molding ensures safety and reliability. A mold maker guarantees quality control.
Challenges in Injection Molding for Fuel Systems
1. Material Selection
Choosing the right material is critical. Some plastics degrade over time. A skilled mold maker selects fuel-resistant, durable polymers.
2. Maintaining Tight Tolerances
Fuel system parts require high precision. Even small errors cause leaks. Automotive injection molds must meet strict tolerances. A mold maker ensures accuracy in every part.
3. Mold Design Complexity
Fuel system parts have intricate shapes. Automotive injection molds must capture every detail. A mold maker uses advanced techniques to achieve this.
Future Trends in Injection Molding for Fuel Systems
1. Sustainable Materials
Manufacturers are shifting to eco-friendly materials. Recyclable plastics reduce environmental impact. Mold makers are adapting to these changes.
2. Smart Fuel System Components
Future fuel systems may include sensors and smart features. Automotive injection molds will integrate these technologies. A mold maker ensures compatibility.
3. Improved Heat Resistance
Advanced materials will improve heat resistance. Mold makers are working with high-performance polymers.
Automotive injection molds play a vital role in fuel system production. Every fuel tank, pump, and connector depends on precision molds. A skilled mold maker ensures strength, safety, and efficiency. With innovations in materials and technology, injection molding continues to advance. As fuel systems evolve, mold makers will drive future improvements.